8 error handling: configuring the error handling, Application example: flying saw – Lenze PLC Designer ApplicationTemplate (PLC Designer R3-x) User Manual
Page 170
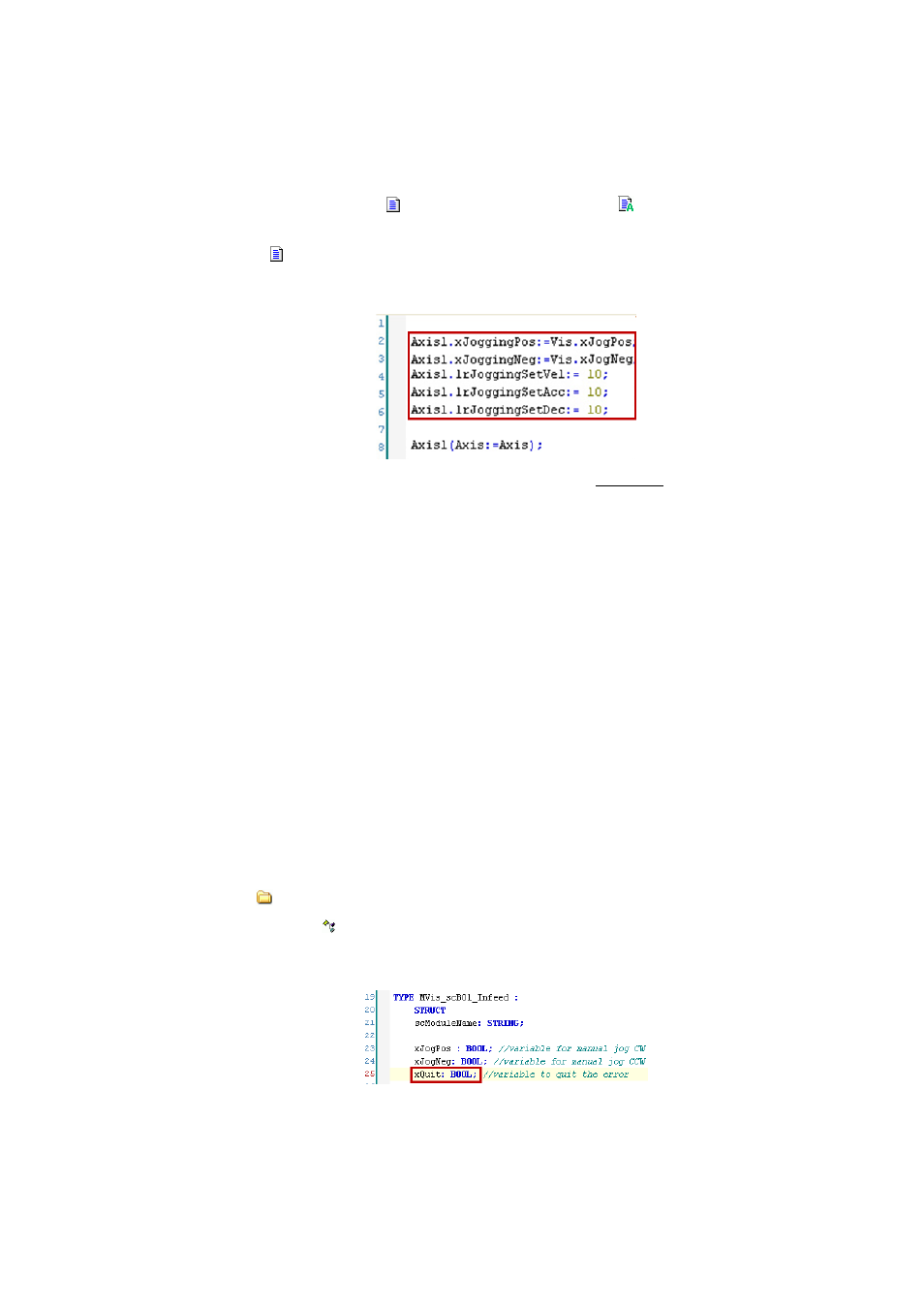
Application example: Flying saw
Error handling: Configuring the error handling
170
Lenze · ApplicationTemplate · 1.3 EN - 04/2013
_ _ _ _ _ _ _ _ _ _ _ _ _ _ _ _ _ _ _ _ _ _ _ _ _ _ _ _ _ _ _ _ _ _ _ _ _ _ _ _ _ _ _ _ _ _ _ _ _ _ _ _ _ _ _ _ _ _ _ _ _ _ _ _
Assign the variables to the AxisBasicControl block.
• Location:
Module application
MAP_B01_Infeed_App1\Action
S00_CYCLIC
• The variables must be interconnected to the xJoggingPos and xJoggingNeg inputs
of
AxisBasicControl.
• Assign the values for speed, acceleration, deceleration to the L_SMC_AxisBasicControl
function block:
The assignments for the variables must be positioned in front of the call of the block
instance. If the assignments are positioned behind, they will not be effective before the
subsequent cycle.
13.8
Error handling: Configuring the error handling
In this example, the enable of the axes must be monitored during a state change:
The error handling is supposed to trigger an error if the axes are not enabled within 200 ms.
• For this purpose, the axes must be inhibited via the hardware input.
• It should be possible to detect and control the error and the error response in the visualization.
• It should be possible to acknowledge the error via a button in the visualization.
The example below shows how the desired error response can be configured in the MM_B01_Infeed
machine module.
How to proceed:
1. Declare the variables in the Mvis_* structure.
Double-click and open:
•
A70_MachineModuleSources\ MM_B01_Infeed
• Structure
MVis_scB01_Infeed
In the structure, declare a variable of the BOOL data type for acknowledging the error,
example: xQuit.
2. Insert the buttons into the visualization.