Raw material production method – Sandvik Coromant Heat resistant super alloys User Manual
Page 8
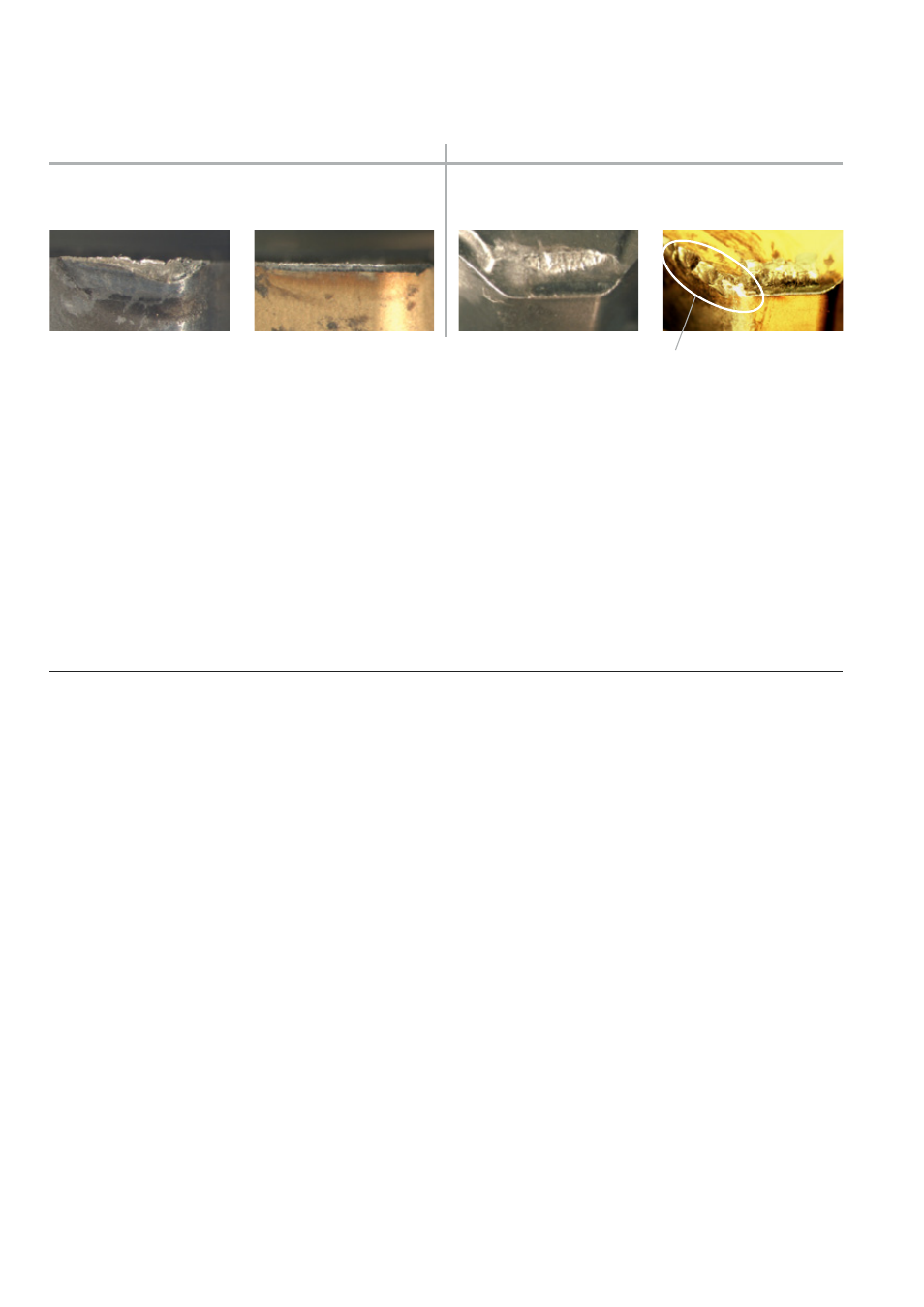
6
S05F
GC1105
GC1105
S05F
3.5 min
Hard material
Soft material
7 min
6 min
12 min
Comparison of wear depending upon
material hardness and insert grade
CNMX 1204A1-SM – v
c
50 m/min, f
n
0.25 mm/r, a
p
1.5 mm
Raw material production method
Depending upon the size, shape and
strength requirements of the component,
various production methods for the blank
material will be adopted.
The production method varies the machina-
bility of the material and will change the
wear characteristics.
Material
Forging
large
medium
Casting
complex shape
poor
Bar stock
<200 mm diameter
good
Components
Advantage/suitability
Machinability
high strength
low strength
availability/strength
Each of these raw material types directly
affects the alloy’s micro structure, and so
also affects the subsequent machining
behaviour:
Forged materials have a finer grain size
than in castings, which improves the
strength and grain flow of the component.
When machining forgings, reducing the
speed and increasing the feed generally
gives the maximum possible metal removal
rate with good tool life.
In castings the opposite applies, and apply-
ing low feeds (0.1 mm chip thickness) and
higher speeds can be beneficial. Castings
have poor machinability and tend to be
most sensitive to notch wear and abrasive
wear. They can be easily identified due to
their visibly mottled surface (the ‘orange
peel’ effect).
Bar stock material is the easiest form of
raw material to deal with. Notching is not
so much of a problem, which allows harder
and more wear resistant insert grades to
be used than for forgings.
Chip hammering