Notch wear – Sandvik Coromant Heat resistant super alloys User Manual
Page 27
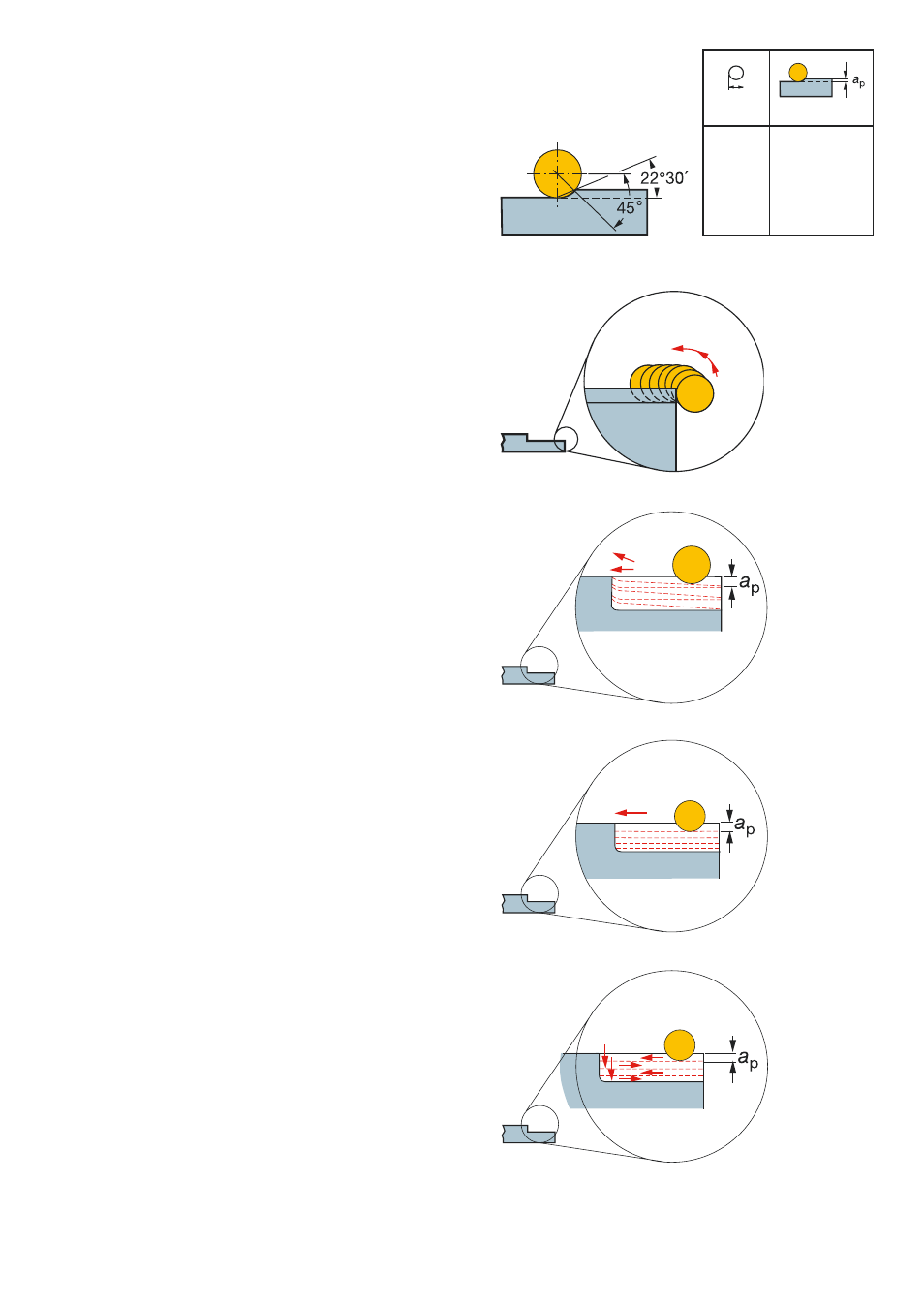
25
Notch wear
Notch wear can be minimized with good
planning and some general advice:
• Use round inserts whenever possible –
ensure the relationship between depth
of cut a
p
and insert diameter does not
exceed 25%.
• Use 45º entering angle when depth of cut
exceeds 25% of iC.
• “Roll over action” in programming to
eliminate the need for pre-chamfering and
minimize the notch wear. There will be
one contact point where the insert hits
the hard scale/surface at the corner of
the component and one different point at
the a
p
line.
• Ramping ensures that any damage is
spread out along the cutting edge. The
depth of cut should be varied between
25% iC to 15% (do not ramp to zero).
• Multiple passes with varying a
p
can be an
alternative.
• For RCGX/RPGX inserts, program in both
directions to utilise more edges on the
insert.
mm
mm
6.35
0.9
9.52
1.4
12.70
1.9
19.06
2.8
25.40
3.8