Carbide insert grades, Engineered solution – Sandvik Coromant Heat resistant super alloys User Manual
Page 60
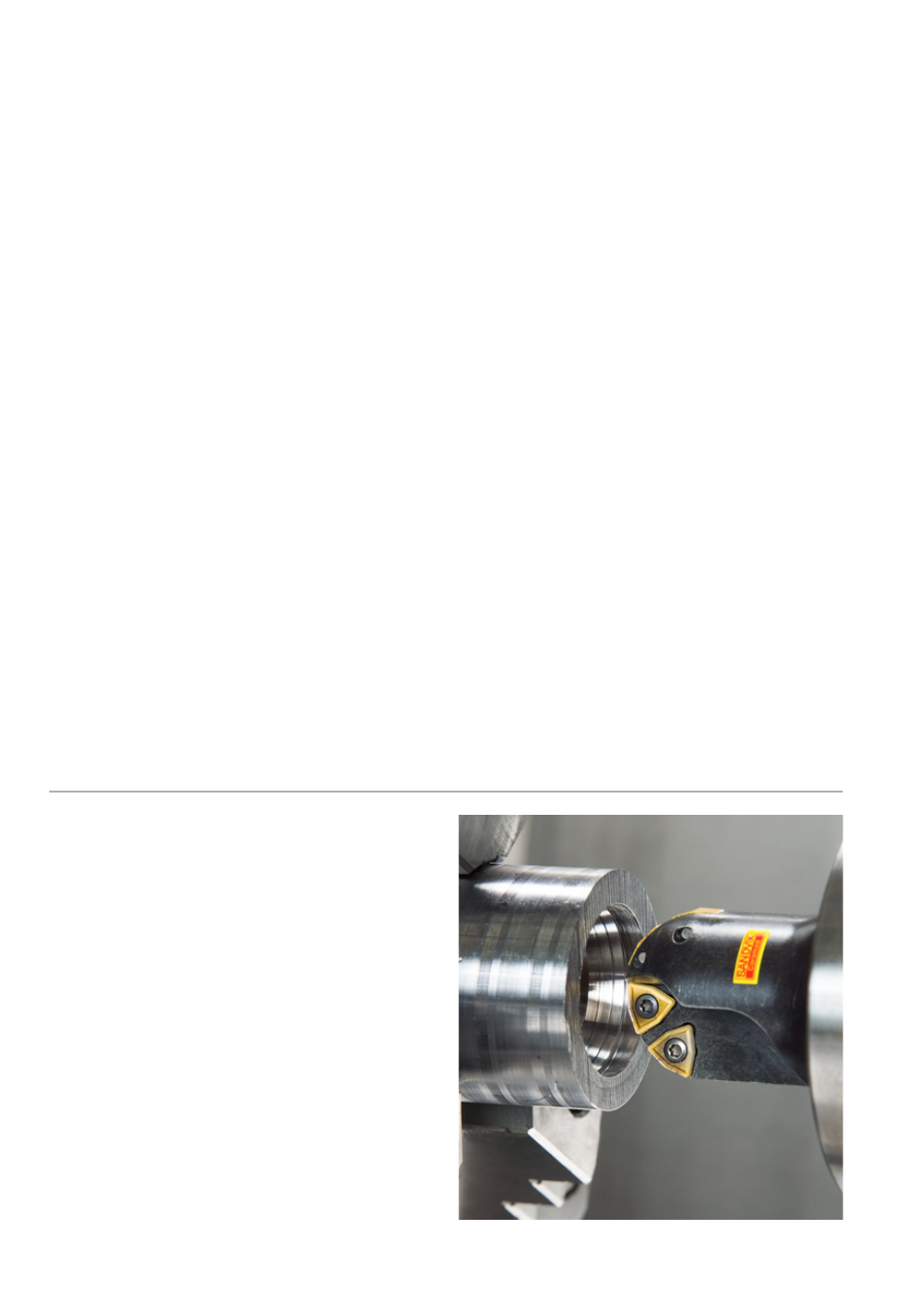
58
• GC1105 – Unique thin PVD (TiAlN)
coating on hard fine grained substrate.
– Excellent adhesion to the substrate
even on sharp edges, good hot hard-
ness.
• GC1115 – Unique oxide PVD coated on
micro-grained carbide.
– Good resistance against built-up forma-
tion and crater wear. Ideal for more
unstable conditions.
• GC1125 – PVD coated micro-grained
carbide.
– Good resistance to thermal shock and
notch wear. First choice for parting-off
operations.
• GC1030 – Unique multi-layer PVD (TiAlN)
coating.
– Improved wear resistance over GC1025
with same toughness. High edge line
security.
• GC1010 – PVD coated micro-grained car-
bide.
– Resistance to plastic deformation and
flank wear due to hot hardness.
• GC5015 – Uncoated cermet.
– Excellent resistance to built-up forma-
tion and plastic deformation.
• S05F – Thin CVD coating on hard fine
grained substrate.
– For applications where notch is not a
significant problem ie round insert and
finishing with small entering angle.
• CT530 – Uncoated cermet grade.
– For finishing operations.
• CB7015 – PVD coated CBN grade with
ceramic binder for continues cuts.
– For good surface finish.
Engineered solution
Developed to optimize the roughing from
bar stock.
• Engineered Coromant U drill
– dia 22-35 mm
– WCMX, GC1020, H13A
• Start cutting data recommendation for
titanium and cobalt chromium.
– Speed v
c
= 50-80 m/min.
– Feed f
n
= 0.08-0.12 mm/r.
Carbide insert grades