Cutting tool materials – Sandvik Coromant Heat resistant super alloys User Manual
Page 23
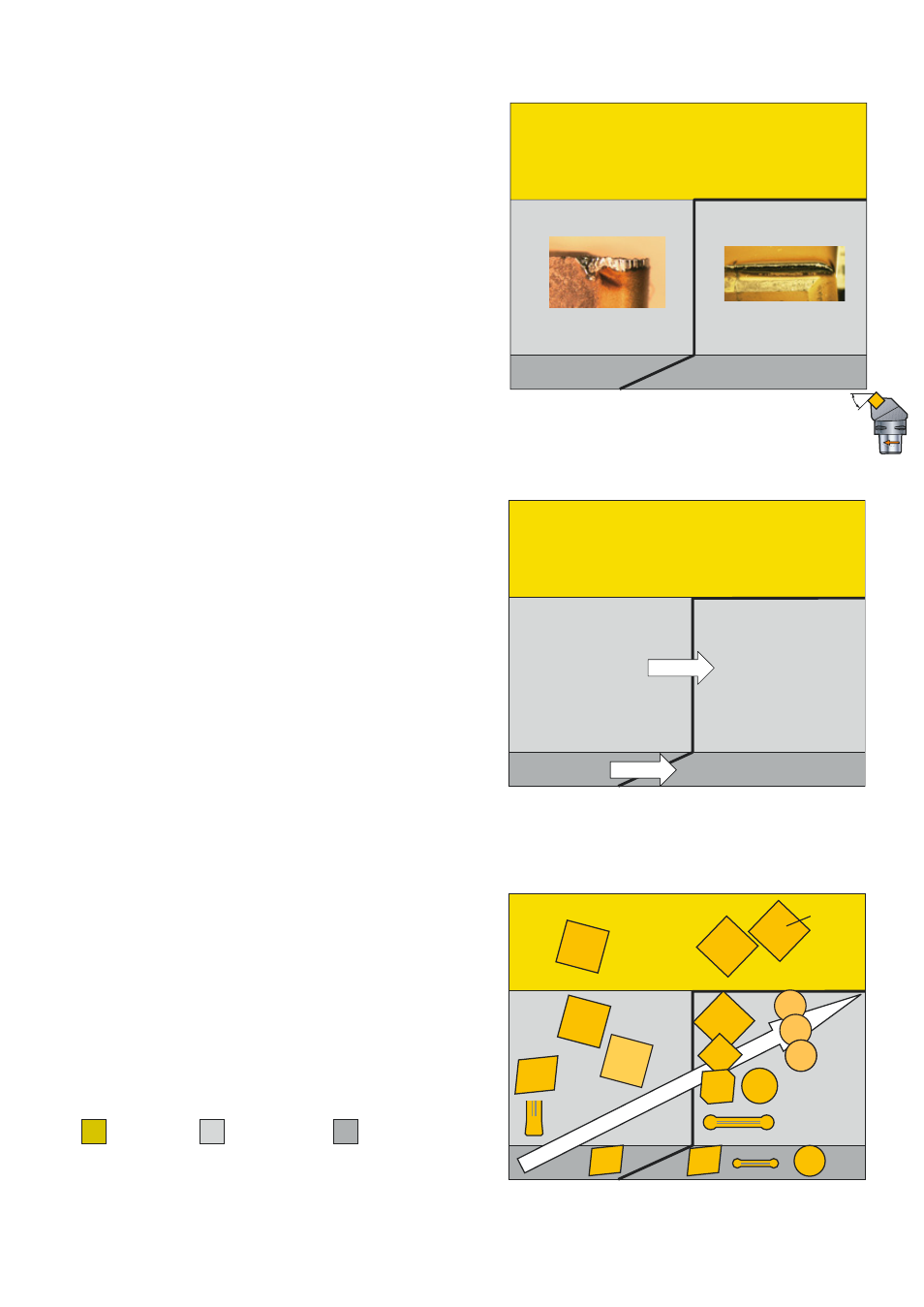
21
GC1105
S05F (GC1105)
1115
1105
1105
S05F
S05F
S05F
1105
1105
S05F
S05F
S05F
6060
6065
670
1115
Grade selection when machining HRSA
should not be considered in terms of finish-
ing and roughing. Plastic deformation (PD)
is present in all operations, however the
formation of notch wear is driven by the
entering angle of the insert.
In practice this means that the grade selec-
tion is optimized depending upon the shape
of the insert.
For an ‘all-round’ grade, working in all areas
GC1105 is the best choice.
The diagram shows the most productive
choice of grade relative to the insert shape.
Wear mechanisms per area
8
5
0.5
8
5
0.5
8
5
0.5
Optimized grade per area
Optimized insert shape per area
90º
75º
60º
45º
30º
15º
Depth of cut (a
p
) mm
90º
75º
60º
45º
30º
15º
90º
75º
60º
45º
30º
15º
Depth of cut (a
p
) mm
Depth of cut (a
p
) mm
Entering angle (
k
r
)
Entering angle (
k
r
)
FSM
= 26 HRC
Entering angle (
k
r
)
ISM
= 46 HRC
LSM
= 46 HRC
Toughness/PD – interrupted cut
PD demanding – continuous cut
Notch = depth of cut notching
PD and notch
demanding
PD demanding
GC2015 – interrupted cut
GC1105/ceramic – continuous cut
PD and notch
demanding
GC1105
GC1115
(GC1125
intermittent)
PD demanding
Ceramic
S05F
(GC1105)
2015
inter-
mittent
Productivity
– Q
cm
3
/min
Cutting tool materials