Production planning process, Typical components – Sandvik Coromant Heat resistant super alloys User Manual
Page 63
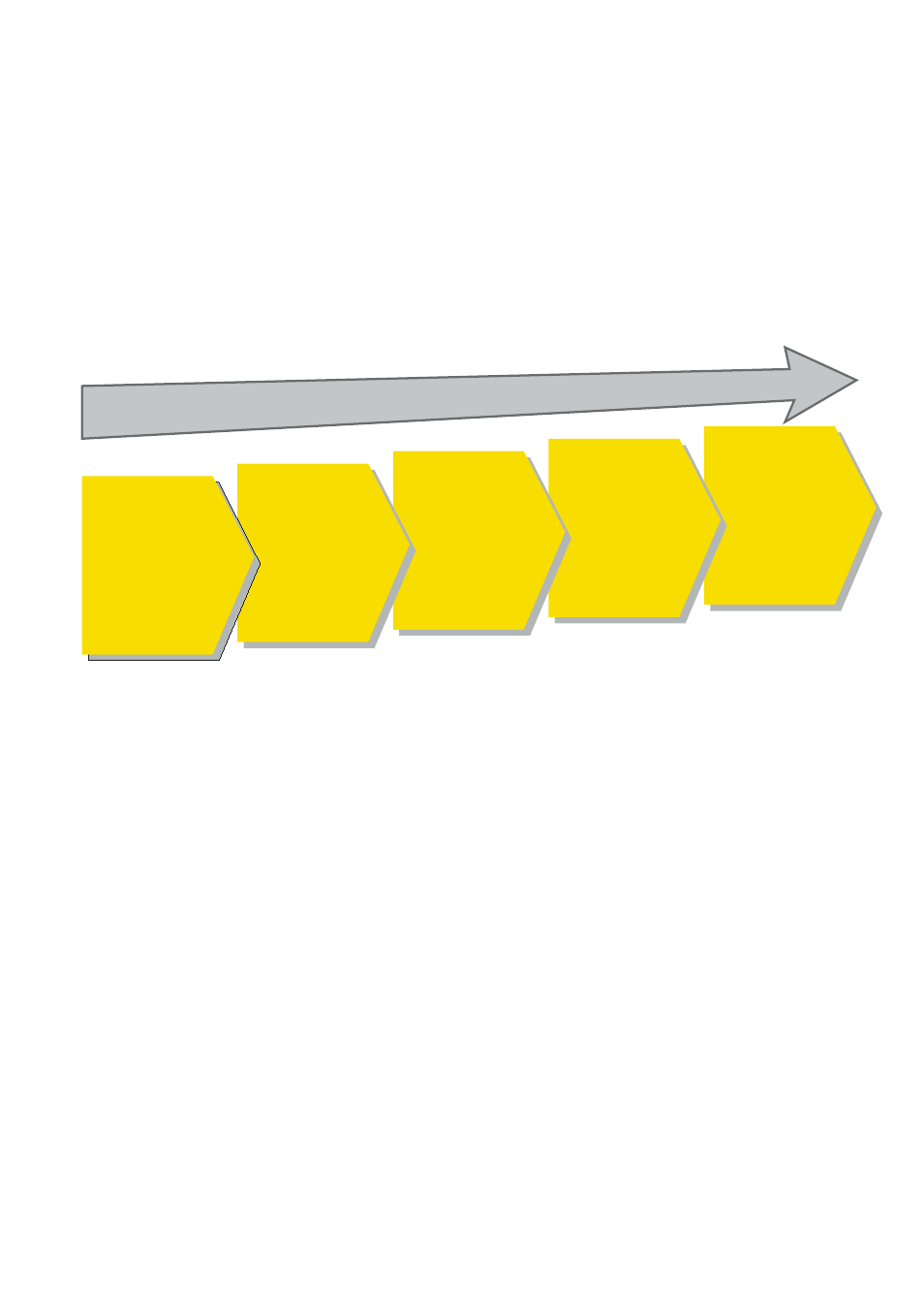
61
Production planning process
To optimise a machining operation all
aspects of the application should be con-
sidered:
• Type of operation?
• Tool paths?
• Conventional or climb milling?
• Cutting tool type and material?
• Change of operation sequence?
Optimising the above is of course neces-
sary, however, to achieve an optimised
process these must be combined with proc-
ess and application ‘know how’ to achieve
secure productive machining. This informa-
tion considers in which order to build an
optimised process for HRSA milling and
discusses important ‘success factors’ for
each stage.
Optimised production planning proces
s
1
Analysis
of features
2
Machining
strategy
3
Cutter style
selection
4
Cutting
data, tool
selection
5
Program
CAM
Typical components
Because of HRSA’s excellent metallurgical
properities they are used in a variety of
industries including:
Aerospace engine
– Combustion & turbine components,
mounting brackets
Selected automotive components
– Turbo chargers, exhaust valves
Medical components
– Dentistry, prosthetic devices
Space vehicle components
– Aerodynamically heated skins, rocket
engine parts
Nuclear power systems
– Valve stems, drive mechanisms
Oil and gas industry
– Marine applications
By far the most common application for
HRSA materials is the aircraft engine. The
use of HRSA in the combustion part of the
engine is increasing. This is typified by the
fact that, whereas in 1950 only about 10%
of the total weight of an aircraft gas tur-
bine engine was made of super alloys, this
has now risen to 50% in today’s modern
engines.
It is predicted that HRSA will continue to be
used extensively in the combustion parts
of an aircraft engine and recent develop-
ments have seen the next generation of
HRSA materials being developed and imple-
mented in production.