Hole making, Hole types and hole making methods, Hole types and hole making methods 104 – Sandvik Coromant Heat resistant super alloys User Manual
Page 106: Hole making in hrsa alloys
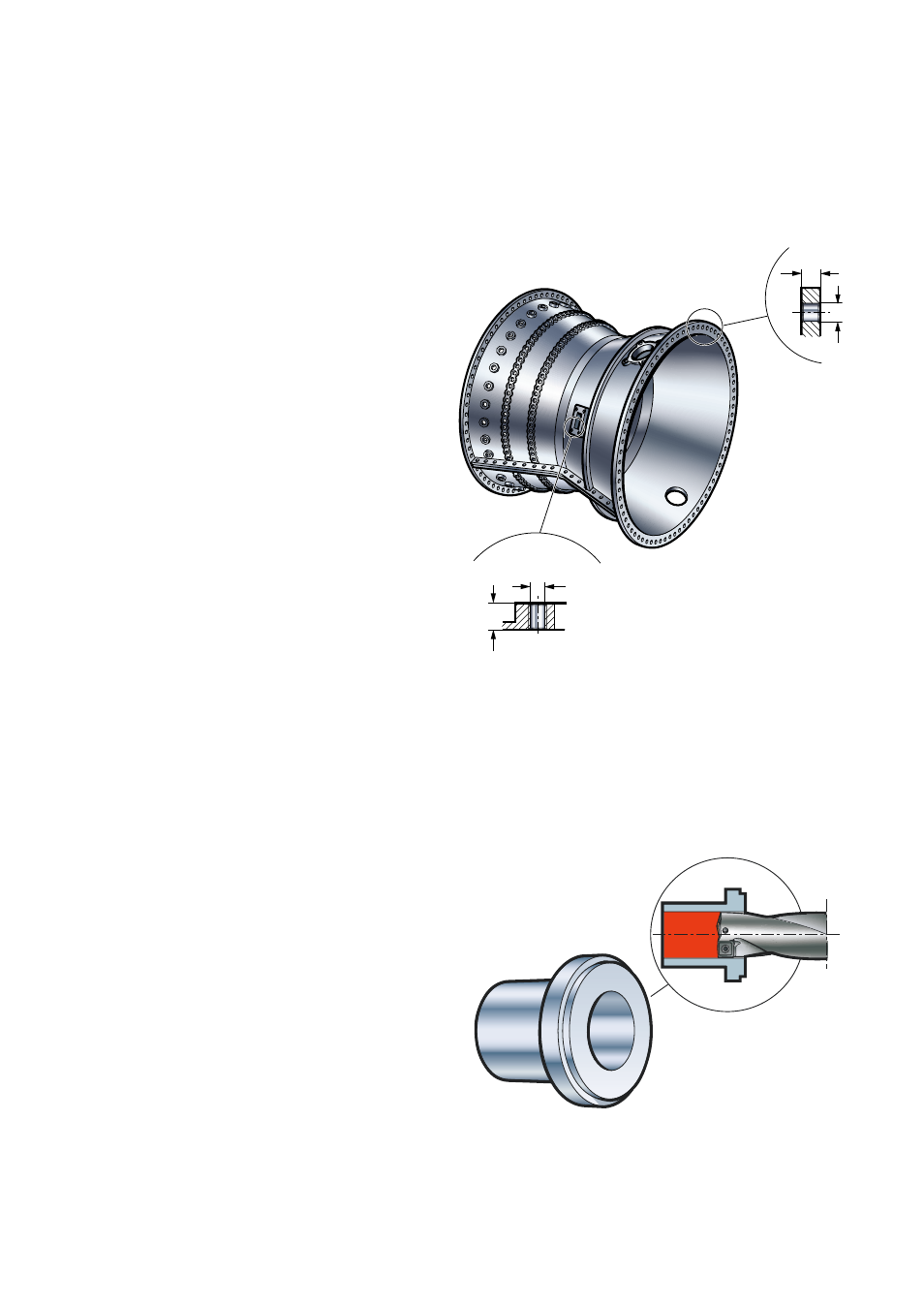
104
Hole making in HRSA can be split up into
5 distinct areas:
> Ø 16 mm through holes for assembly
In aerospace engines: casings, flanges,
rings, discs, shafts, etc usually have identi-
cal, relatively small holes drilled in large
numbers. These are often in diameters
and with limitations suited to solid carbide
drills.
For critical parts the hole is often made
in up to 5 steps to guarantee quality and
consistency.
1. drilled
2. bored (using a sized milling tool) to
make concentric
3. finish bored (using a sized milling tool)
4. chamfer front
5. chamfer back
This is one of the final machining opera-
tions so reliability is paramount, and as
there can be hundreds of holes on just one
component this can naturally be a lengthy
process.
Ø 12 to Ø 60 mm through holes
in stable components
Oil and gas, bearing industry and mechani-
cal engineering where the components are
stable, indexable insert drills are used as
the first roughing operation on either lathes
or machining centres. Subsequent opera-
tions can include boring and turning.
Hole making in HRSA alloys
Hole types and hole making methods