Alloy groups – Sandvik Coromant Heat resistant super alloys User Manual
Page 6
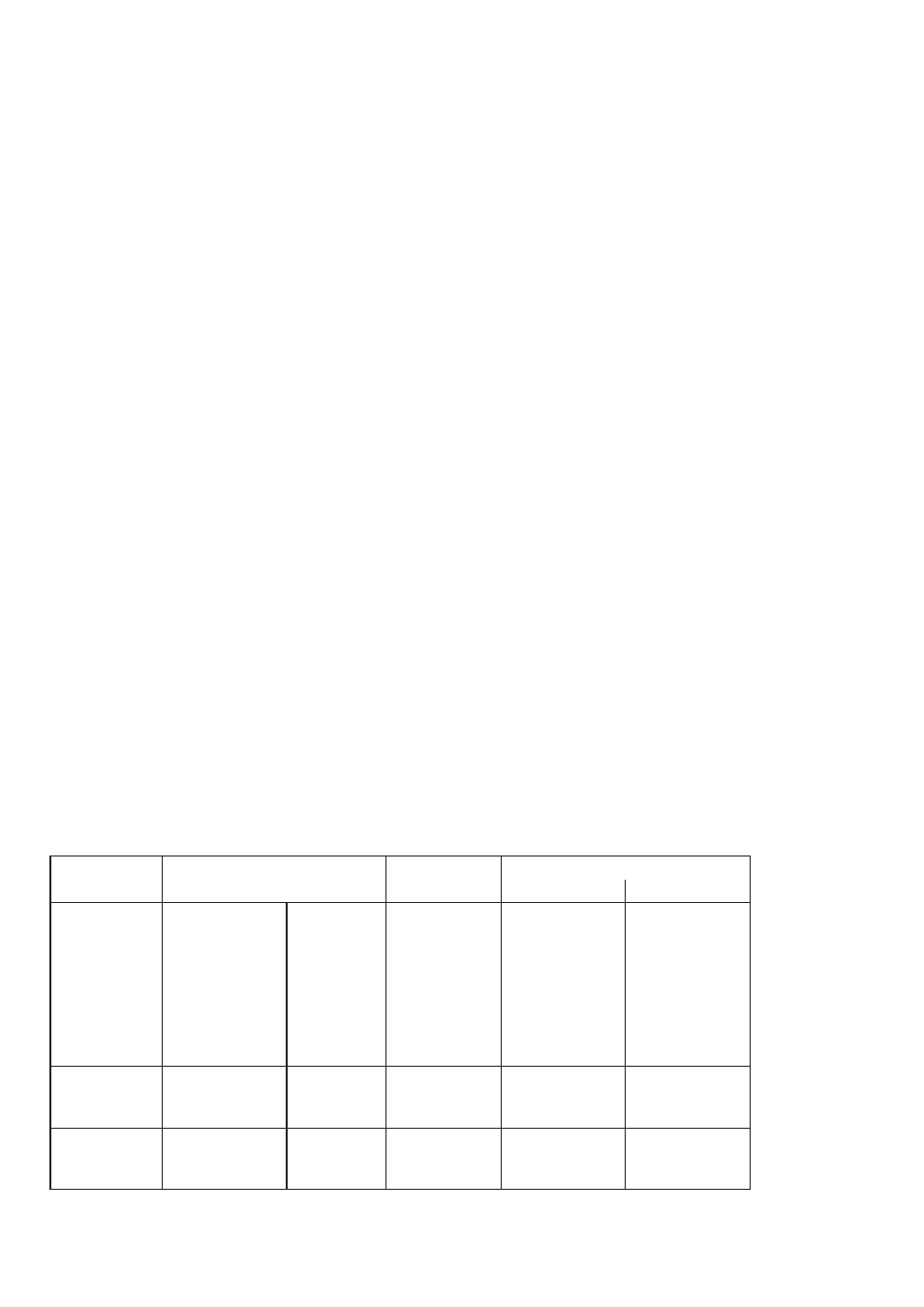
4
MC S2.0.Z.AN
CMC 20.2
425
285
200
Hastelloy S
Hastelloy X
160
Nimonic PK33
350
Udimet 720
Waspaloy
MC P5.0.Z.AN
CMC 05.3
Greek Ascoloy
300
MC M1.0.Z.PH
CMC 05.4
A286
300
MC S2.0.Z.AN
CMC 20.21
Incoloy 909
MC S3.0.Z.AG
CMC 20.3
Haynes 25
Stellite 21
280
340
Stellite 31
HRSA materials fall into three groups:
nickel-based, iron-based and cobalt-based
alloys. The physical properties and machin-
ing behaviour of each varies considerably,
due both to the chemical nature of the alloy
and the precise metallurgical processing it
receives during manufacture. Whether the
metal is annealed or aged is particularly
influential on the subsequent machining
properties.
Nickel-based are the most widely used, and
currently constitute over 50% of the weight
of advanced aircraft engines. The trend is
that this will increase in new engines in the
future.
Common types include:
• Inconel 718, Waspaloy, Udimet 720
– precipitation hardened
• Inconel 625 – solution strengthened
(not hardenable)
Iron-based have been developed from
austenitic stainless steels. Some have very
low thermal expansion coefficients (such as
Incoloy 909) which make them especially
suited for shafts, rings, and casings.
However, they have the poorest hot strength
properties of the three groups.
Common types:
• Inconel 909
• A286
• Greek Ascoloy
Cobalt-based display superior hot corrosion
resistance at high temperatures compared
to nickel-based alloys. They are more expen-
sive and also more difficult to machine due
to their great wearability.
The use in turbines is restricted to combus-
tion parts in the hottest engine areas.
Their main use is seen in surgical implants,
which utilise their inherent corrosion resist-
ance.
Common types:
• CoCr
• Haynes 25
• Stellite 31
Alloy
group
Nickel
Iron
Cobalt
Material
Hardness HB
Ann.
Aged
The most common HRSA alloys (see page 120 for the complete list)
Alloy groups
Code
Inconell 718
Inconell 706
Inconell 625