Machinability/raw materialcondition, Machinability/raw material, Condition – Sandvik Coromant Heat resistant super alloys User Manual
Page 7: Machinability/raw material condition
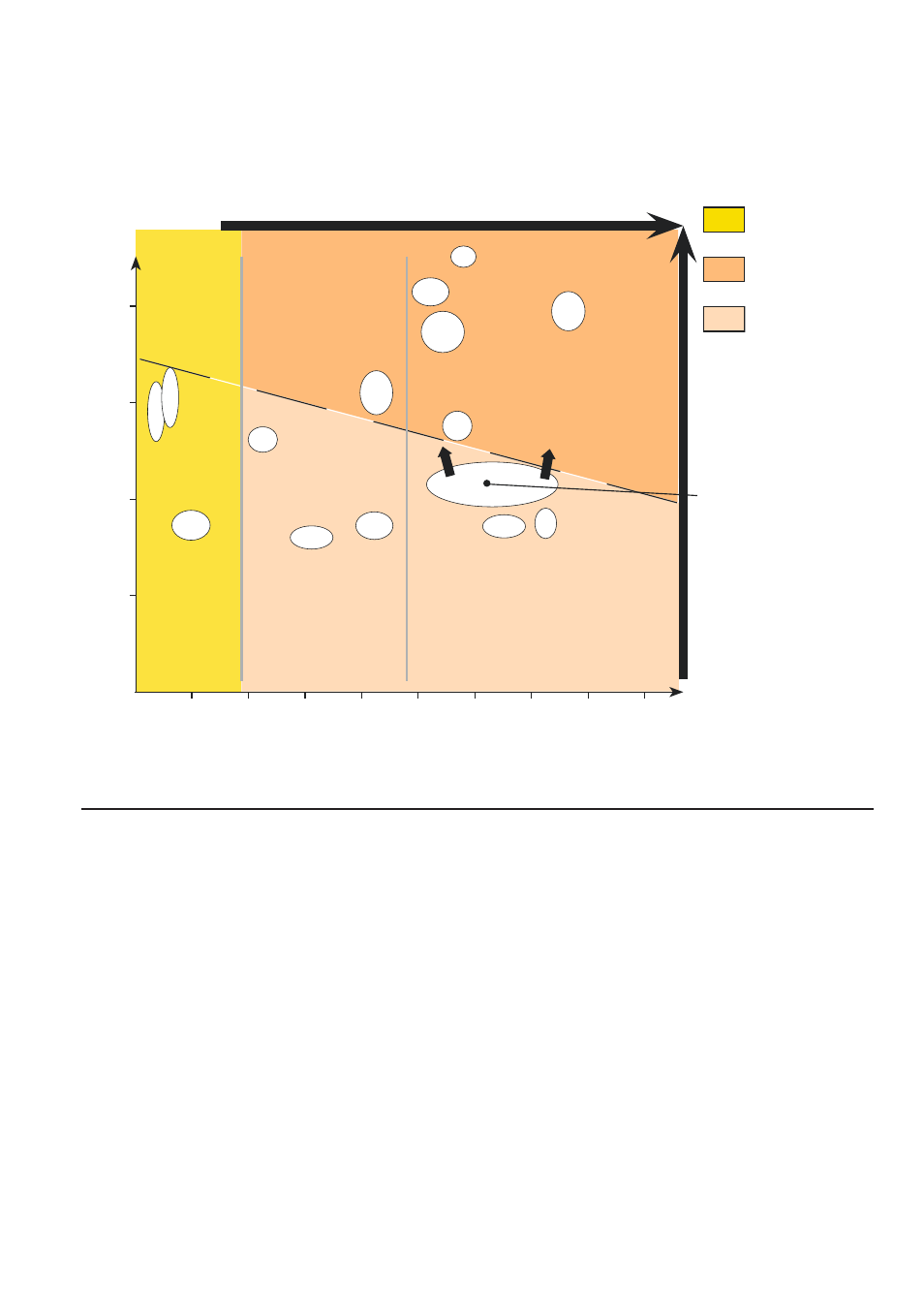
5
17-4 PH
Jethete
M152
Crucible
A286
Incoloy 800
Sanicro 30
Incoloy 901
Incoloy 901
Inconel 625
Nimonic 75
Nimonic 263
Nimonic PK 33
Waspaloy
Nimonic 90
Nimonic 105
Nimonic 80A
Inconel 718
Nimonic 1023
400
300
200
100
10
20
30
40
50
60
70
80
90
With such a wide spread of materials under the generic heading of HRSA the machining
behaviour can vary greatly even within the same alloy group. In fact the same material can
have numerous machining recommendations.
Stainless
steels
Fe based alloys
Ni based alloys
Austenitics
Precipitation hard enable
alloys in annealed conditions
Heat generated during cutting
(tendency for plastic deformation)
Tendency
for notch wear
Hardness
HB
Weight %
Nickel & cobolt
= Heat treated
(aged)
= Solution
treated
(annealed)
Machinability/raw material condition
The state of heat treatment affects the
hardness of the component and hence the
wear mechanisms. The formation of the
chip is a good indicator of the hardness –
with hard materials it is easier to break the
chip.
Hardened materials have increased cut-
ting temperatures and show a tendency to
notching of the cutting edge at the depth
of cut. The combination of a low entering
angle and a hard substrate with a coating
offering a heat barrier is required.
Softer materials machine similarly to the
stainless steel family.
Insert grades with greater toughness and
reduced hot hardness – resistance to high
temperatures – are required due to reduced
cutting temperatures and increased chip
hammering. Here, damage to areas outside
the actual cutting edge is caused by the
chip breaking against the insert.
Heat treatment
Annealing
– heating to controlled temperature then cooling at
controlled rate.
<30HRC
Solution treatment
– heating followed by rapid cooling
<30HRC
Ageing
– slow cooling after solution treatment
up to 48HRC
= Stainless
steel