Effect of a, Entering angle – Sandvik Coromant Heat resistant super alloys User Manual
Page 76
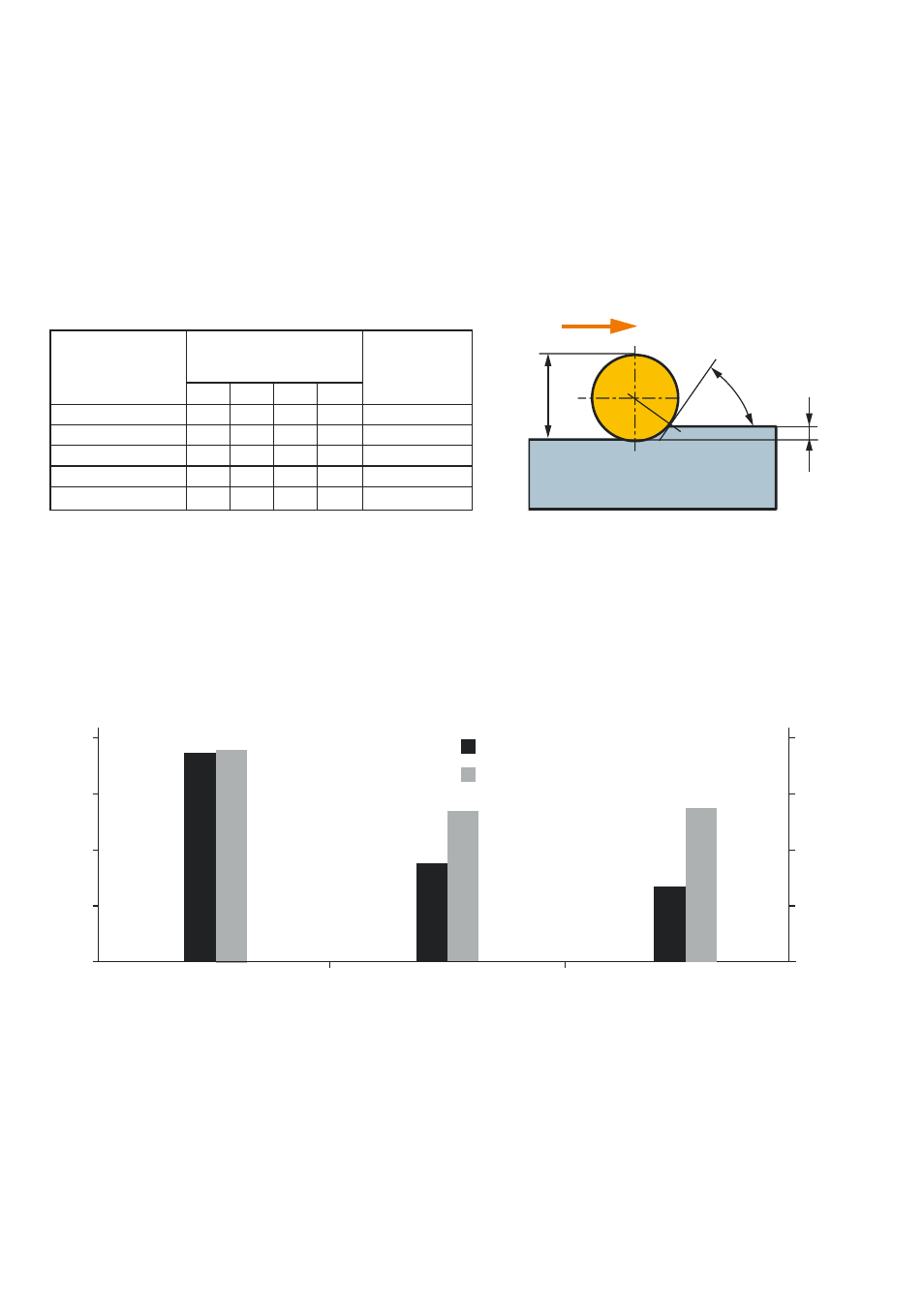
74
iC
k
r
a
p
80
60
40
20
0
Effect of a
p
/entering angle
Selecting the correct cutting depth/entering
angle when face milling in HRSA materials
has an effect on tool life and productivity.
Despite limitations on depth of cut when
using round insert cutters these are still
the most productive method when milling
HRSA. Unlike typical titanium aerospace
frame components HRSA components tend
to have geometries that require high metal
removal rates but not at high depth of
cut, for example blades, casings etc. This
allows optimisation of the entering angle at
varying depth of cut.
8
10
12
16
0.25
2
2.5
3
4
60°
0.2
1.6
2
2.4 3.2 53°
0.15
1.2 1.5 1.8 2.4 46°
0.1
0.8
1
1.2 1.6 37°
0.05
0.4 0.5 0.6 0.8 26°
Depth of cut to
diameter ratio
a
p
/iC
Depth of cut for insert
diameter, in mm
Entering
angle
k
r
Grade/geometry recommendations for milling HRSA
Tool R300-063Q22-12H, insert R300-1240E-MM 2040
z
n
7, D
c
51 mm, v
c
30 m/min,
a
e
36 mm, f
z
0.3 mm/tooth
Material: Inconel 718 (40 HRC)
Minutes in cut
= Average time in cut
= Average volume removed
Total metal removed, cm
3
Recommendation – most productive depth of cut is 1 mm, this gives an entering angle
of 33° when milling using a round insert.
a
p
1.0 mm
a
p
1.5 mm
a
p
2.0 mm
h
ex
0.16 mm
h
ex
0.18 mm
h
ex
0.21 mm
1120
840
560
280
0