Typical wear mechanisms – Sandvik Coromant Heat resistant super alloys User Manual
Page 13
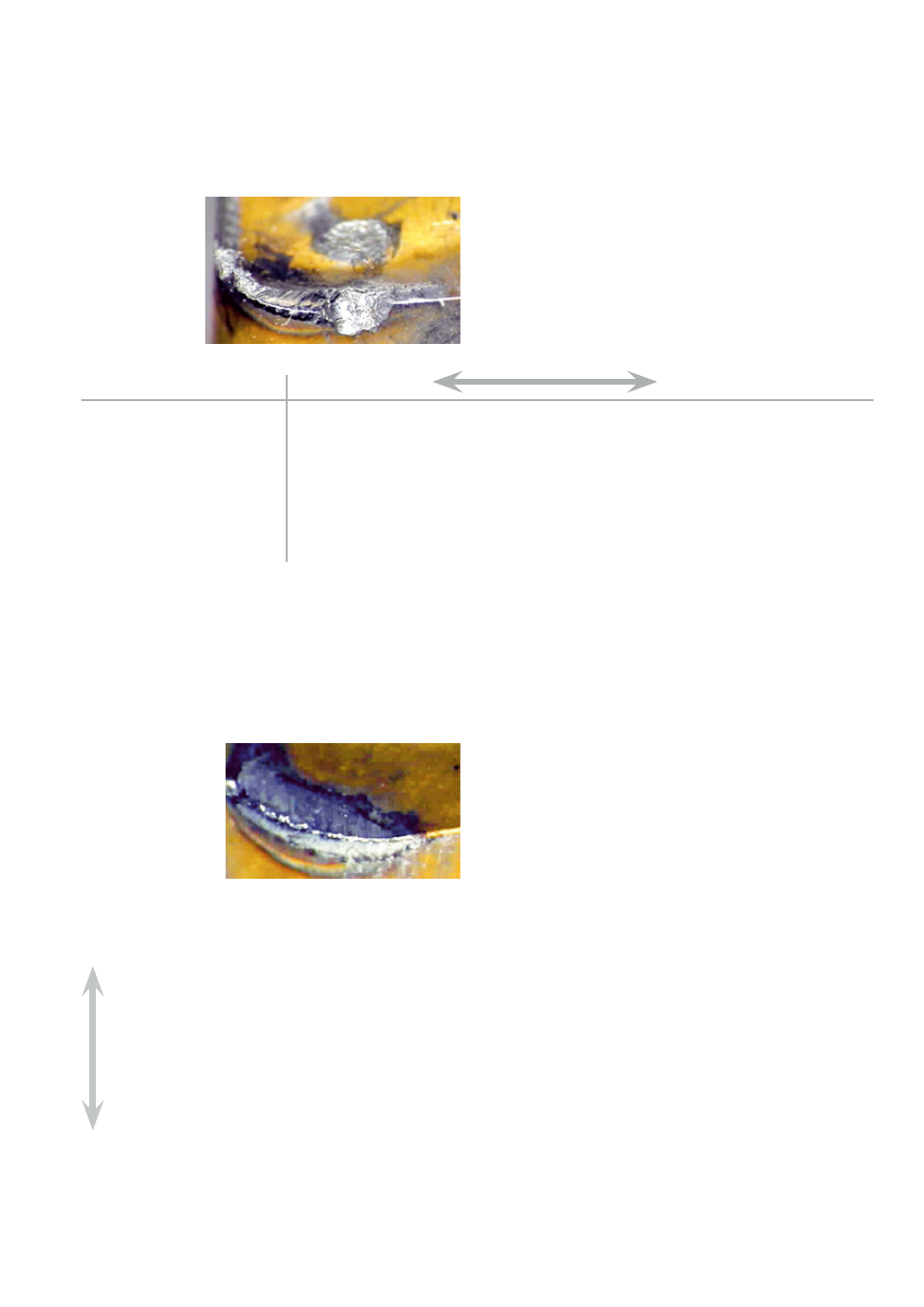
11
CC6060, CC6065
CC670
CC670
S05F
GC1105
GC1105
GC1115
H13A
H13A
GC1125
GC1125
GC2025
GC2135
GC2035
GC1145
Least notch
Most notch
Entering/lead angle
Depth of cut
Geometry
Material hardness
Material condition
Grade
Round inserts
Below nose radius
Positive
Soft condition
Bar stock
PVD fine grain carbide
(GC1115, GC1105)
Forged
CVD
(S05F)
C/DNMG 95 degree
Above nose radius
Negative
Hardened
Cast
Ceramic
(CC6060/CC6065/CC670)
Turning
Grooving
Ceramic
Carbide
Typical wear mechanisms
With carbide grades two wear mechanisms dominate – plastic deformation and notch wear.
It is important to identify which is the most prominent before selecting the correct grade
and strategy.
Notch wear on main cutting edge is a
mechanical wear which is concentrated at
the depth of cut. The extent of notch wear
is directly related to:
Because of these factors, notching is the critical wear for ISM where the material is hard
and the depth of cut is relatively high. To reduce notching, use as small entering angle as
possible.
Plastic deformation (PD)/even flank wear
– as a result of combined high tempera-
tures and high pressure on the cutting
edge. This wear is much more of a grade-
specific issue than notch wear, which is
more application related. Good wear resist-
ance and hot hardness will reduce the likeli-
hood of plastic deformation.
In case of excessive flank wear, use a more
wear resistant grade or reduce the cutting
speed.
Flank wear resistance
Hot hardness
Bulk toughness