Ceramic insert grades – Sandvik Coromant Heat resistant super alloys User Manual
Page 24
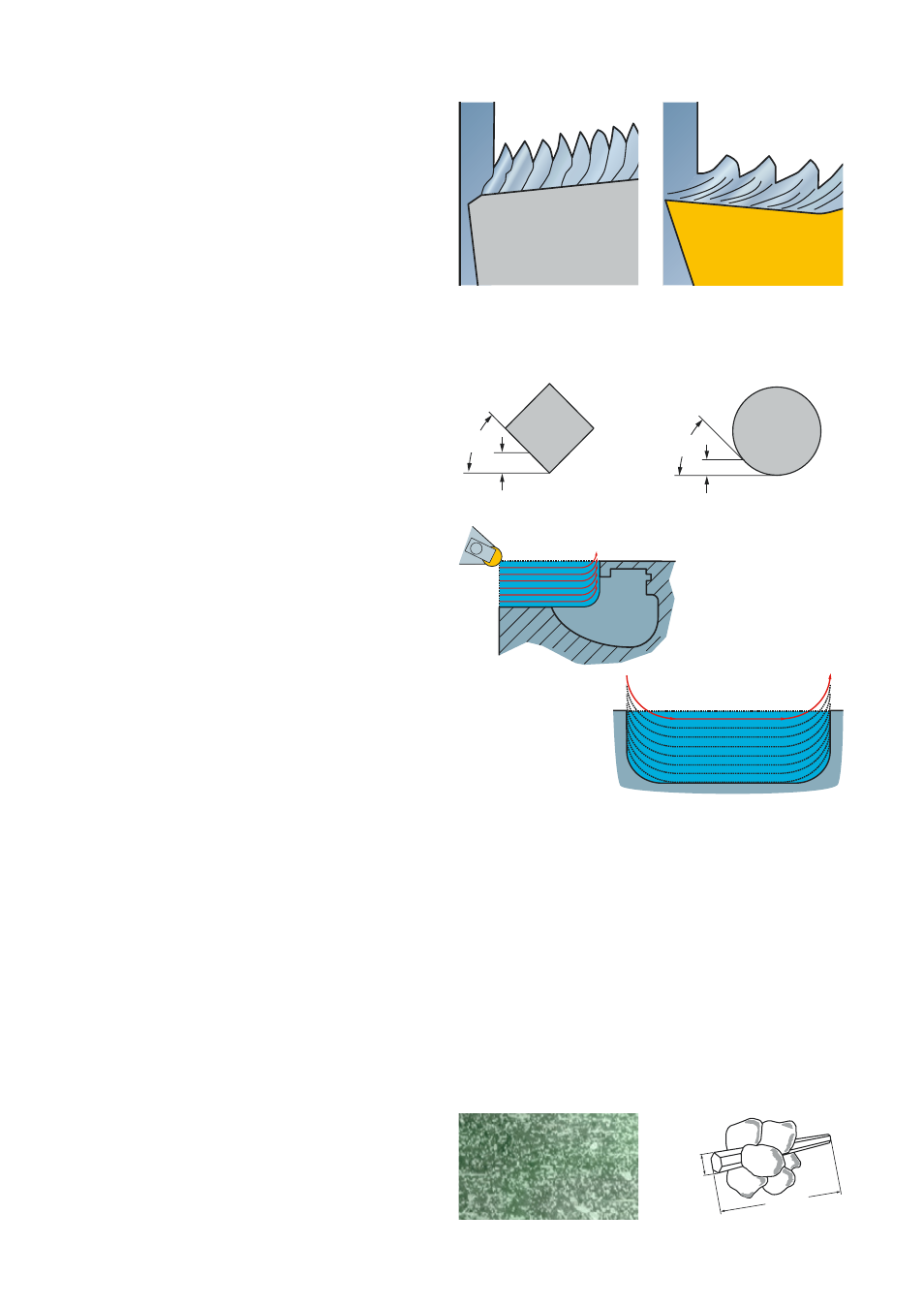
22
Ceramic insert grades
45º
>45º
Ceramic cutting materials offer excellent
productivity in roughing operations in FSM
and ISM. Their application differs greatly
compared to carbide due to their:
• High temperature resistance – allows
high cutting speed to be applied to pro-
duce a highly plasticised and sheared
chip.
• Low toughness – can lead to edge fritter-
ing, top slice and notch wear.
Both of these factors mean that for suc-
cessful application the following rules need
to be applied:
• Optimize entering angle at about 45° to
reduce notch, round or square inserts
should be used.
• Maximum chip thickness – between
0.08 to 0.15 mm.
• Optimized programming techniques
- to minimize notch on entry and long
passes.
- control the cutting arc of engagement in
corners.
There are 2 types of ceramics developed
for use in HRSA:
• Sialon – (Silicon, Aluminium, Oxygen,
Nitrogen) – a mixture of silicon nitride and
aluminium oxide. It has the best chemical
stability resisting notch wear:
- CC6060 – optimized choice for long
cutting lengths in clean material and for
profiling/pocketing with optimized pro-
gramming techniques.
- CC6065 – optimized for heavy roughing
applications, plunging and machining
direct into corner.
• Whiskered ceramic – to provide the
improved toughness and bulk strength
compared to the traditional ceramic,
fibres are included:
- CC670 – first choice for machining of
forged components with rough scale
and ovality.
Ceramics
Carbide
0.5 mm
10–80 mm