KROHNE Summit 8800 Vol 2 User Manual
Page 21
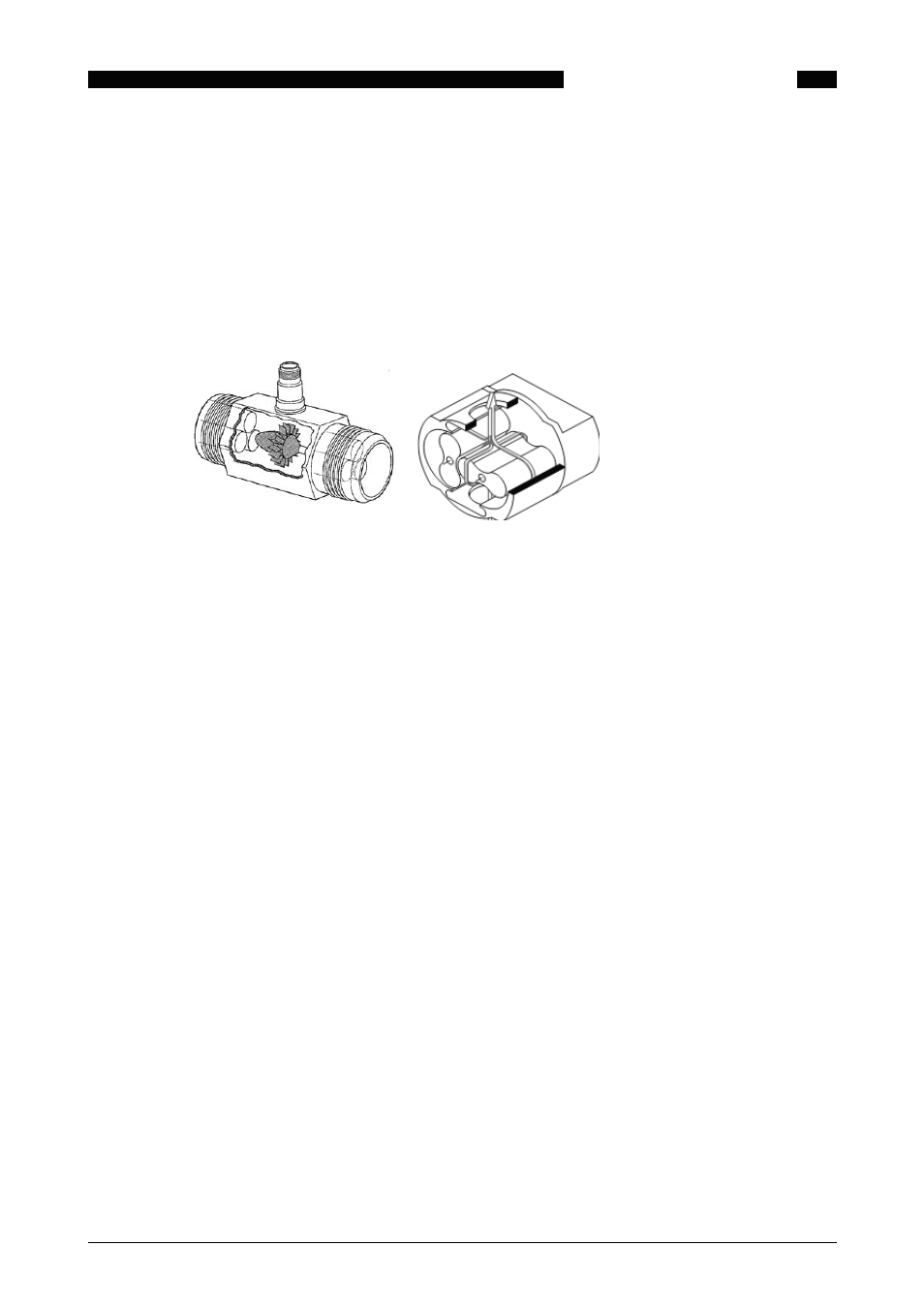
21
www.krohne.com
08/2013 - MA SUMMIT 8800 Vol2 R02 en
SUMMIT 8800
METERING PRINCIPLES
03
3. Metering principles
In this Chapter the different meter technologies supported by the SUMMIT 8800 and the need for
correction and normalization is described. Each of these technologies has its own particularities
which are important to know when configuring the flow computer.
3 .1 Pulse based meters: e .g . turbine/ positive displacement / rotary meter
This method stems from the time when rotating meters where used, such as turbine meters and
rotary (Positive displacement) meters.
Figure 2 Turbine and rotary meter
A turbine meter is basically a fan in a tube. The gas makes the fan rotate and the rotations are
recorded in an index on top of the meter. A positive displacement or rotary meter consists of
two tighly coupled impellers which together create a moving chamber of gas. The rotation of the
impellers drive an index.
A contact switch is operated by the rotating meter. The result is that the periodic closure of the
switch is directly related to the amount of gas going through the meter. Depending on the loca-
tion of the switch there are:
HF pulses or high frequency pulses
• The switch can be mounted just above the turbine blades. This switch is closing at the higher
rate than the meter rotates (typically up to 5000 Hz). The ratio between the two is called
“blade ratio”.
MF pulses or medium frequency pulses
• The switch mounted on the primary axes, so this switch is closing every turn of the meter.
This results in a medium frequency pulse (typically up to 500 Hz)
LF pulses or low frequency pulses
• For low cost meters the switch can be mounted in the index after a gear resulting in slow
pulsing switches and in a low accuracy measurement (typically below 50 Hz)
A problem with this method is that the switches do not always close 100% reliable. This is par-
ticularly true for the HF pulses as non-contact switches are used. This means that we can have
missing pulses. Also too many pulses can occur, e.g. when interference occurs with the high
frequency wires or due to thunder storms. The solution is to have dual pulses and check the
relation between the two.
It may also be that a turbine blade may break off resulting in the wrong measurement. There is
therefore a need for diagnostics. Several solutions have been implemented:
• The dual pulse method with a 90° angle between the two. This allows for diagnostics and even
corrections for missing pulses. An API classification level A to E is available (see below) for
this.
• A second pulse from a turbine wheel with different blade angle.