9 troubleshooting – INFICON SQC-310 Thin Film Deposition Controller User Manual
Page 39
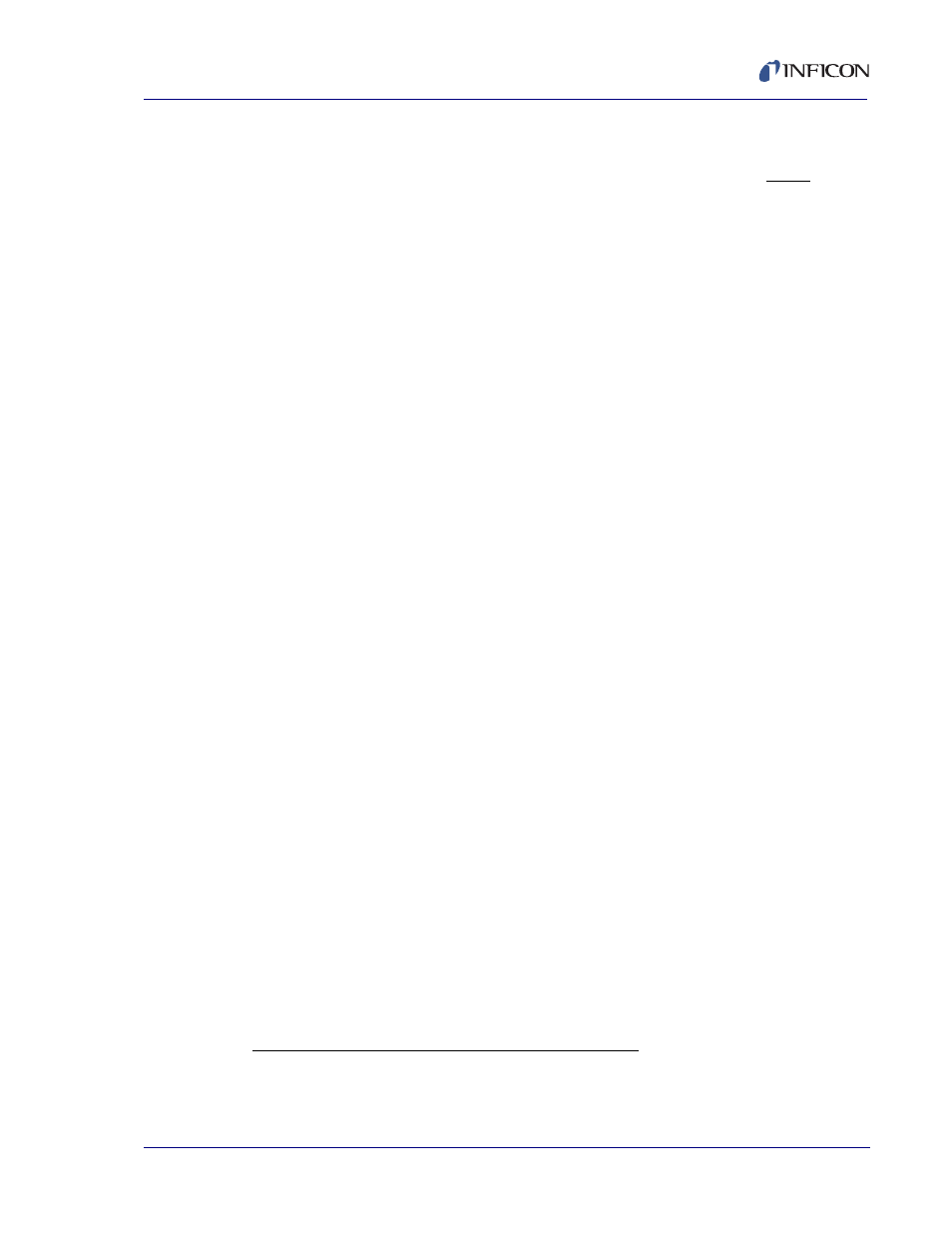
2 - 15
IP
N 07
4-
55
0-
P1
B
SQC-310 Operating Manual
to an input change. Quickly adjust Power (%) to PWR
DR
. Measure the time for the
Rate (
Å
/s) reading to reach RATE
2/3
. You may want to do this several times to get
an average response time. Displaying the Rate graph will also help. Twice the
measured time is the step response time, TIME
SR
. TIME
SR
is typically 0.2 to 1
seconds for E-Beam evaporation, 5 to 20 seconds for thermal evaporation.
Set PID Values: Set the power to zero. In the Quick Edit menu set P=25,
I= TIME
SR
, D=0. Set Max. Pwr to ~20% higher than PWR
DR
. Exit the Quick Edit
menu and press Manual/Auto to move to Auto (PID control) mode and observe the
Power graph. The power should rise from 0%, and stabilize near PWR
DR
with little
ringing or overshoot. If there is more than about 10% overshoot, lower the P Term.
If the time to reach PWR
DR
is very slow, increase the P Term. A lower I Term will
increase response time, a higher value will eliminate ringing and setpoint
deviations. It is unlikely you will need any D Term.
Continue to adjust P & I values, alternating between Manual Power 0% and Auto
mode until steady-state response is smooth and the step response is reasonably
controlled. You don’t need to totally eliminate ringing during the step if the
steady-state response is smooth; preconditioning will minimize step changes.
Typical I values for thermal systems are 4 to 10; Ebeam I values are 0.5 to 2. It’s
impossible to predict P values, but it is best to select the lowest value that provides
adequate rate control.
Ebeam systems may require additional steps to limit the control loop’s response
during arcing. First, be sure Max. & Min. power are set to limit the output to
reasonable values for this material and rate. Slew Rate can further limit
too-aggressive power changes. Remember that slew rate is % of full scale per
second. At rates below 10
Å
/s, a slew rate of 1-2% per second is common. Finally,
decreasing the filter Alpha will limit the PID response to occasional large noise
spikes, such as from arcing.
Set Preconditioning: The power level you recorded as PWR
0R
is the power where
deposition just begins. That’s a good value for Ramp 1 power in the Film Conds
menu. PWR
DR
, or slightly less, is a good value for Ramp 2 Power. This will prevent
a large step change when entering the deposition phase.
Once PID terms are established for a material, they will typically be similar for other
materials. Only the P Term and preconditioning power levels may need adjustment.
2.9 Troubleshooting
Most SQC-310 problems are caused by defective crystals or improper film setup,
particularly incorrect PID settings for the control loop. Follow the procedures below
to identify and correct common problems.
No Readings, or Erratic Readings from Sensors
Disconnect the deposition source power supply. This eliminates the possibility that
a noisy source, or poor loop tuning, are causing an unstable PID loop.