Hypertherm Phoenix 8.0 User Manual
Page 446
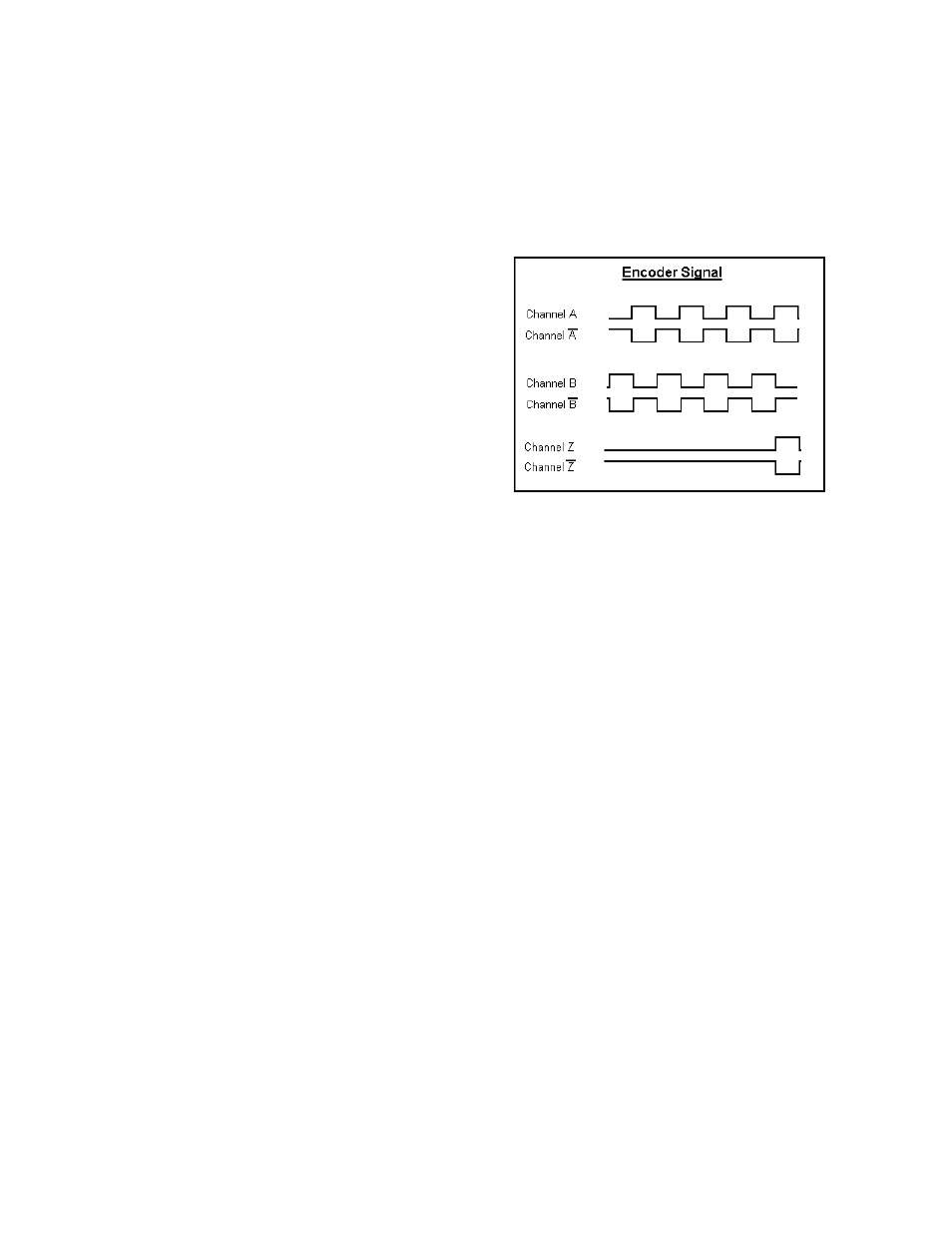
Motion Overview
439
There is a direct relationship between the rotation of the motor shaft, the encoder light
pulses, and the distance of the motion. Therefore, the control is able to calculate distance
by counting the encoder pulses it receives, which closes the position loop. This
relationship, shown as a simplified formula is:
encoder pulses x motor revs = distance
The encoder generates a square wave signal as
illustrated in the Encoder Signal diagram to the
right. Most encoders provide two main signals,
A and B, and the complements, A/ and B/.
These signals are also referred to as channels.
The compliment channels are not always used
but if they are used, they can provide increased
noise immunity. The rotational direction, or
encoder polarity, can be determined by the
signal that is received, either ABABA or
BABAB.
The channel Z signal is produced only once a revolution and is called the marker pulse.
This marker pulse is quite often used for accuracy in homing routines.
The pulses are called counts. The holes in the disk are also called lines. The pulses that
the receiver picks up may actually be the beginning and end of each pulse for a line on
both channels (A&B) so that the receiver picks up four pulses for each line. This is
called a 4x mode encoder. Thus, a 1000 line encoder in 4x mode would produce 4000
counts for each revolution of the motor. The more counts an encoder produces, the more
accurate the motion is.
Following Error
Following error or servo error is the distance between the position that the control
commands and the actual position of motion. Some following error is normal because
the resistance of the load prevents the response of the motor to reach the ideal command
of the system. This latent response is similar to driving a car away from a stop light. It
takes time for the engine to produce the force that is required to move the weight of the
car to the desired speed. Following error for each axis can be selected to be viewed in the
Watch Window / Status Window of the control. This is a quick reference tool for
monitoring the performance of the actual machine motion as compared to the control
command.
The important consideration for X/Y coordinate motion is that the response for the X and
Y motion is similar. If the response is dissimilar, poor results for commanded motion
will result. An example of a dissimilar tuned response would be that when a circular
motion is commanded, an oval or elliptical motion will result as one axis out performs the
other.