Motion overview, Closed loop servo control – Hypertherm Phoenix 8.0 User Manual
Page 444
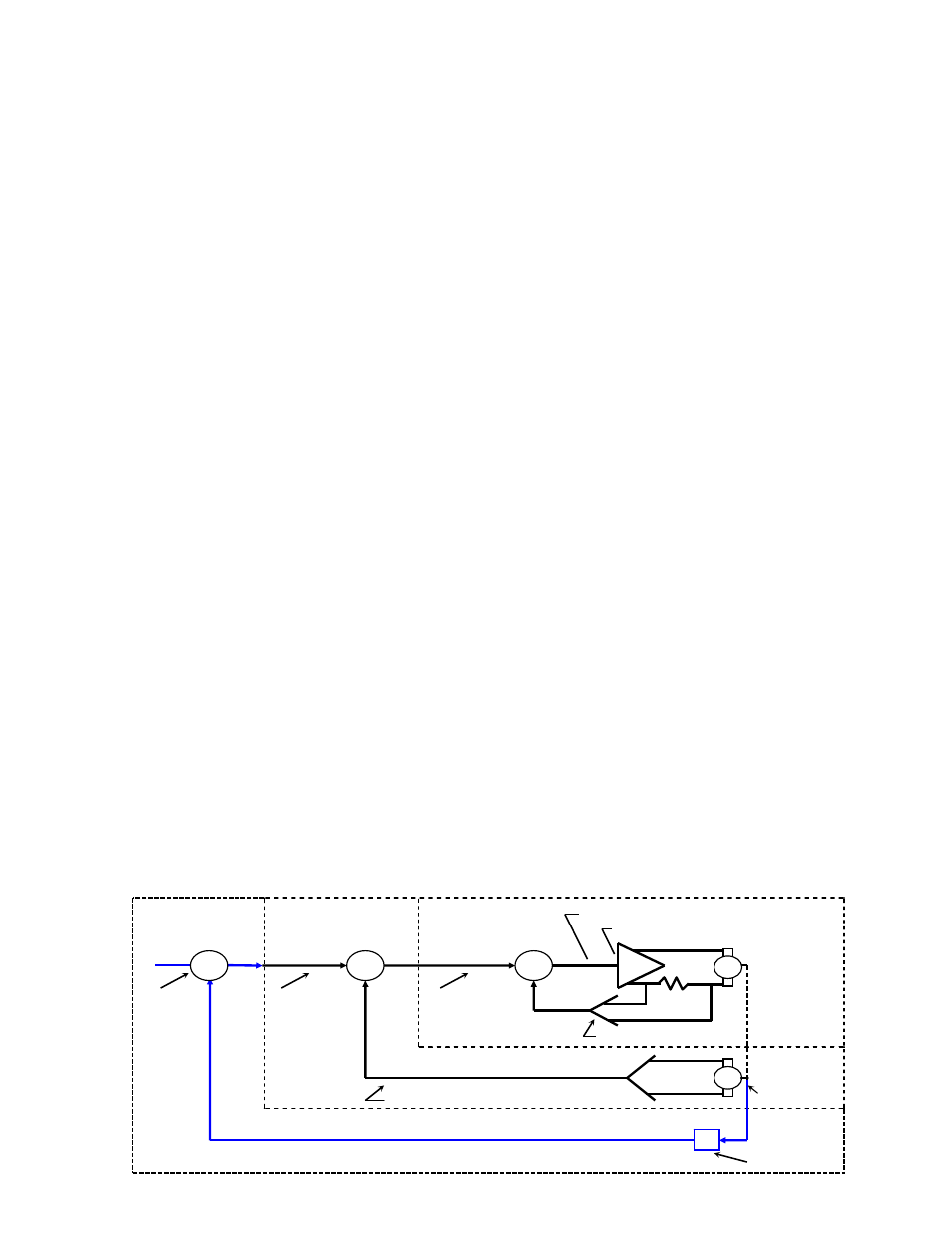
437
Motion Overview
This section provides an introduction to motion theory.
Note: System tuning should be performed by a qualified service technician. Improper
tuning can cause personal injury or damage to the system.
Outline of Information
1. Closed loop servo control
2. Encoders
3. Following error
4. Position and servo error
5. Edge per inch parameter
6. Gain
7. Recommended tuning procedures
Closed Loop Servo Control
A servo system is the means of accurately controlling electrical motors to create force.
The motor output is connected to a gear system to translate the rotational force of the
motor into linear motion. In addition, this gear system modifies the strength and speed of
the motion.
Closed loop servo control is the continuous process of monitoring position, or velocity
commands, or both compared to actual position and velocity and adjusting the output
accordingly. A servo system without feedback devices and automatic adjustment
capabilities is called an open loop servo control.
The drawing below outlines a typical velocity and position loop system. The most
important aspect for motion control is the position loop. The process starts with the
motion control providing a motion command (voltage) to the motor to move at a specific
speed to a position. Position is tracked during the motion by means of a feedback device,
or encoder, that provides both directional and distance information. Based on this
feedback, the control adjusts its motion command, or voltage, to the motor to ensure that
the motor is accurately positioned on the designated motion path at the correct speed.
Current
Command or
Velocity Error
Velocity
Command
Signal
Servo
Motor
Current Amplifier
Current Error Signal
Current
Feedback
Tachometer
Velocity
Loop
Current
Loop
Position
Loop
E
Position
Command
Encoder
+
-
Velocity Feedback Signal
+
+
-
-
∑
∑
∑
M
T
R
S