Control wiring, Chapter 2 installation/wiring, Tb10 – Rockwell Automation 1336T FORCE Series B User Manual
Page 45: J3 j4, Tb11
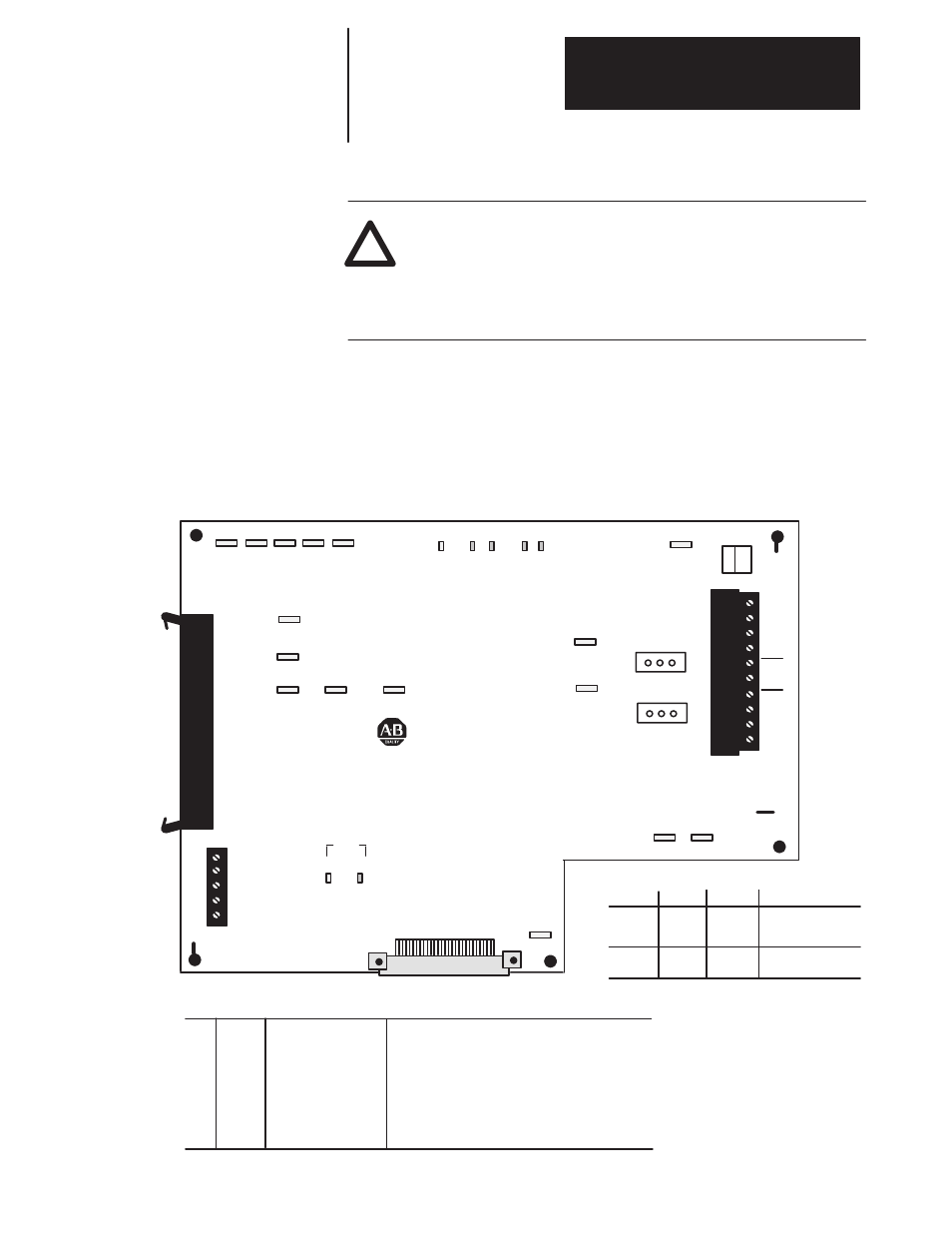
Chapter 2
Installation/Wiring
2–25
Control Wiring
!
ATTENTION: When user installed control and signal wiring
with an insulation rating of less than 600V is used, this wiring
must be routed inside the drive enclosure so that it is separated
from any other wiring and uninsulated live parts. Failure to do so
could result in equipment damage or unsatisfactory Drive
performance.
Encoder, Brake and Drive to Drive interface connections are performed on
the Main Control Board (Fig. 2.11). The maximum and minimum wire
size accepted by TB10 and TB11 on the Main Control Board is 3.3 and
0.06 mm
2
(12 and 30 AWG). Maximum torque for both terminal blocks is
0.79 N–m (7 lb–in.). Use copper wire only.
Figure 2.11.
Terminal Block Locations Main Control Board
Base
Driver
Board
Control
Signals
J7
TE
1
Drive to
Drive
Interface
J5
SHUNT +
Adapter
Board Interface
+15V
TB10
D1
TP1
10
D2
D3
D5
VP Indicator
TP2 TP3
TP5
TP4
AGND –15V
+5V
DGND
D4
Enable
SHUNT –
SHIELD
ENC A
ENC A
ENC B
ENC B
ENC +
ENC –
SHIELD
TP24
TP23
12V ISO ISO COM
TP8
J1
V –
C_L
J3
J4
5V
12V
5V
12V
Encoder Feedback
(J3 & J4 must be set
for same voltage)
CP Indicator
D1
D2
D3
D4
D5
D43
D47
Green
Green
Red
Green
Red
Amber
Green
Drive Enable
VP Indicator
VP Indicator
CP Indicator
CP Indicator
Drive to Drive Status
Drive to Drive Power
ON – Drive Running, OFF – Drive Not Running
ON – No Faults, OFF – See D3
Refer to Fault Codes in Table 4.A
ON – No Faults, OFF – See D5
Refer to Fault Codes in Table 4.A
Solid – OK, Blinking – Fault
ON – Power, OFF – No Power
Flt Trp
1
2 3
1
2 3
Jumper
+5VDC
J3
J4
1–2
1–2
+12VDC
Purpose
2–3
2–3
Encoder Voltage
Selection
Encoder Voltage
Selection
SHD
TB11
C_H
V+
D43
D47
TP25
STS PWR
D2D
DGND
TP13
TP9
TP14
DC Bus
FDBK
TP16
TP17
I
A
FDBK
I
c
FDBK
TP18
I
q
CMD
TP19
I
d
CMD