Lenze ECSCMxxx User Manual
Page 121
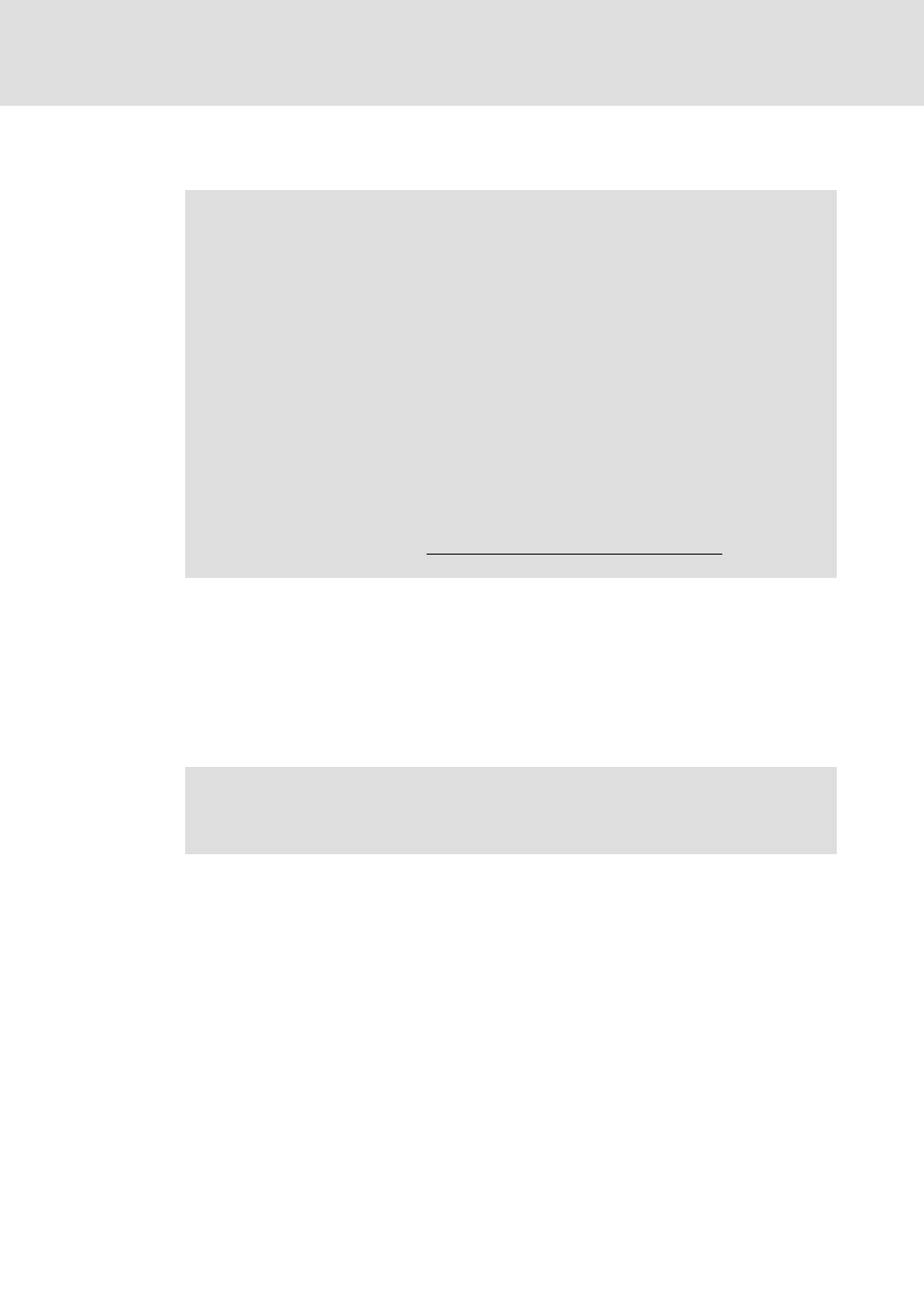
Commissioning
Setting of the feedback system for position and speed control
Absolute value encoder as position and speed encoder
l
121
EDBCSXM064 EN 11.0
6.7.5
Absolute value encoder as position and speed encoder
}
Danger!
Valid when using an operating software up to and including V7.0:
When absolute value encoders are used, uncontrolled movements of the drive
are possible!
If an absolute value encoder is disconnected from the axis module during
operation, the fault OH3−TRIP occurs. If the absolute value encoder now is
connected to X8 again and a TRIP−RESET is carried out, the drive may start up in
an uncontrolled manner with a high speed and a high torque. A SD8−TRIP will
not occur, as would be expected.
Possible consequences:
ƒ
Death or severe injuries
ƒ
Destruction or damage of the machine/drive
Protective measures:
ƒ
If a fault (trip) occurs during commissioning when an absolute value
encoder is used, check the history buffer C0168. If an Sd8−TRIP is at the
second or third place, a reinitialisation is absolutely necessary. For this
purpose, switch off and on again the 24−V supply of the control electronics.
An absolute value encoder mounted on the motor shaft can be used without an additional
resolver as position and speed encoder.
1. Select absolute value encoder for position and speed control.
– Single−turn encoder: C0490 and C0495 = 3
– Multi−turn encoder: C0490 and C0495 = 4
If X8 has been selected as output by changing C0491, X8 will be automatically reset to
input through the encoder selection.
)
Note!
If an encoder (TTL, SinCos, absolute value encoder) is used, for C0490 and
C0495 only identical settings are permissible.
2. Select an absolute value encoder.
– Single−turn encoder: C0419 = 307 ... 311
– Multi−turn encoder: C0419 = 407 ... 411
The encoder data (C0420, C0421, C0427) are set automatically in accordance with the
selection.