Lenze ECSCMxxx User Manual
Page 181
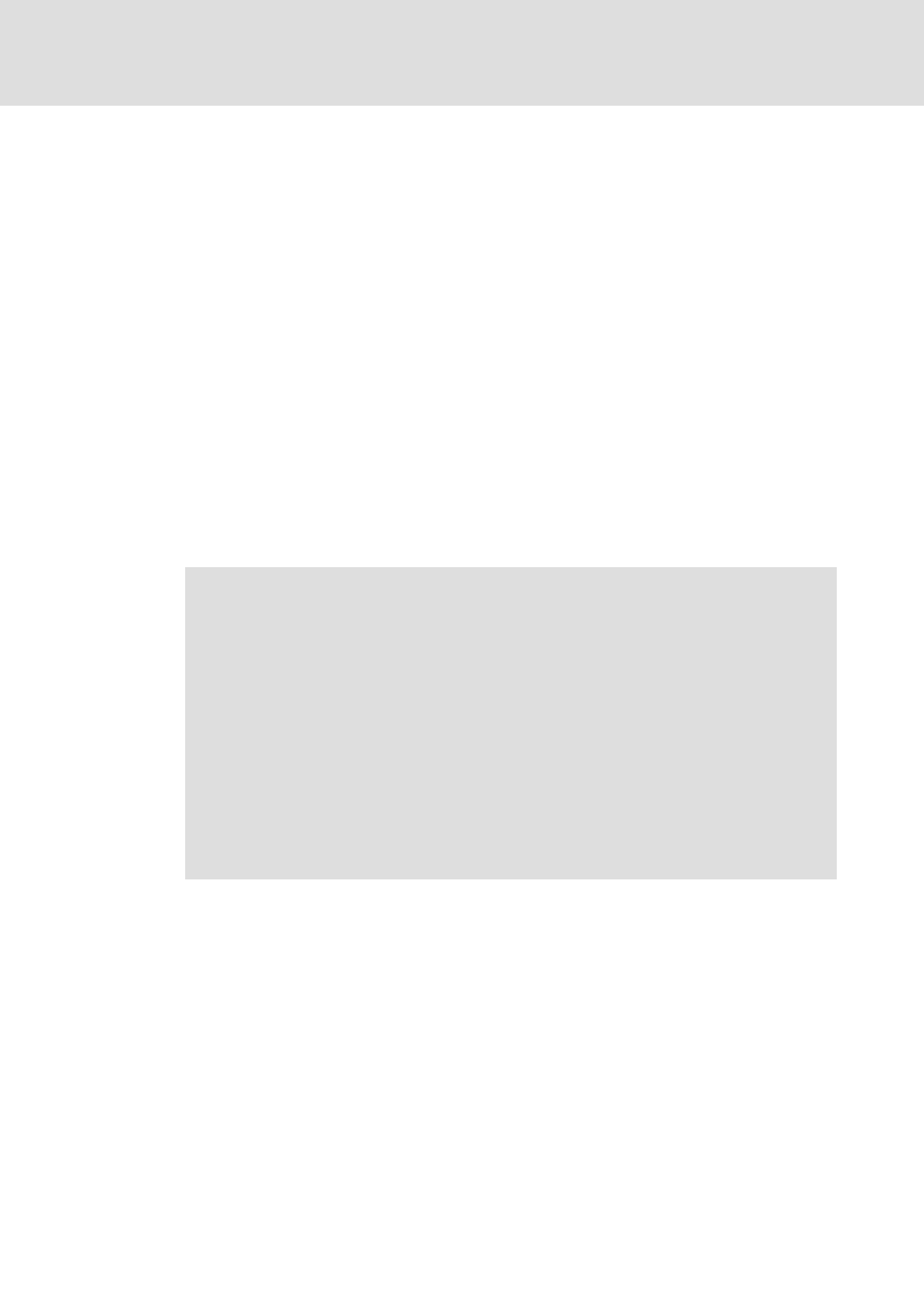
Commissioning
Operation with motors from other manufacturers
Effecting rotor position adjustment
l
181
EDBCSXM064 EN 11.0
Setting sequence
1. Inhibit controller. (
^ 169)
– Press the
– Green LED is blinking, red LED is off
2. Unload motor mechanically.
– Separate the motor from the gearbox or machine so that it can rotate freely.
3. Open holding brake (if available).
4. Activate rotor position adjustment with C0095 = 1.
5. Enable controller. (
^ 169)
– X6/SI1 = HIGH and X6/SI2 = HIGH and press the
The rotor position adjustment program of the controller is started:
– The rotor rotates half a revolution in 16 steps (for resolver with 1 pole pair:
180° electrically
¢ 180° mechanically).
– After one revolution, C0095 is automatically reset to "0".
– The rotor zero phase is stored under C0058. (For absolute value encoders
(Hiperface®, single−turn/multi−turn) at X8, C0058 is always "0".)
}
Danger!
Uncontrolled drive movements after an Sd7 fault with absolute value
encoders
If absolute value encoders are used and the rotor position adjustment is
completed with the fault message "Sd7" (
¶ 270), the rotor position could not
be assigned to the feedback system. In this case, the drive may carry out
uncontrolled movements after controller enable.
Possible consequences:
ƒ
Death or severe injuries
ƒ
The machine/drive may be destroyed or damaged
Protective measures:
ƒ
Repeat rotor position adjustment (starting with step 1).
ƒ
Check wiring and interference immunity of the encoder at X8.
6. Inhibit controller. (
^ 169)
– Press the
– Green LED is blinking, red LED is off
7. Save the data determined by the controller with C0003 = 1.
I
Tip!
The values for C0058 and C0095 are only displayed in GDC if you place the bar
cursor on them and read back the code using function key