Cascade, Cascade setup procedure, Cascade autotuning procedure – Watlow Series F4S/D User Manual
Page 22
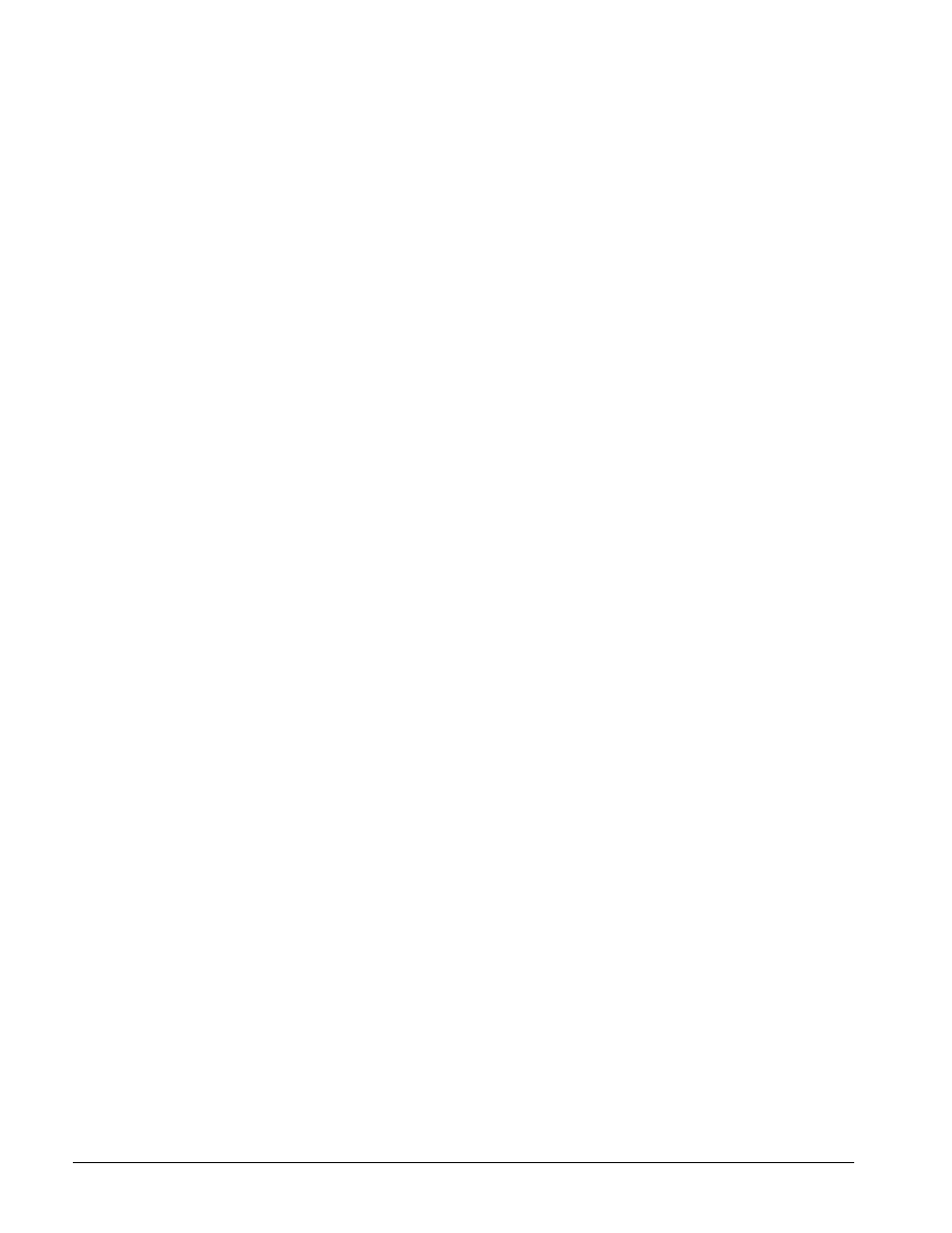
3 . 6
■
O p e r a t i o n s
Wa t l o w S e r i e s F 4 S / D
Cascade
Cascade control is available on the Series F4 con-
trollers. For background information about cascade
control, see the Features Chapter.
Select cascade control through the Analog Input 3
Menu (Setup Page) and choose Process Cascade or
Deviation Cascade. To set the range for the Process
Cascade Inner Loop set point, use Low and High
Range settings. These are independent of the Chan-
nel 1 set point. Deviation Cascade uses Deviation
Low and High settings that are referenced to the
Channel 1 set point.
Deviation Cascade is used in applications with large
set point ranges or where limiting heating or cooling
equipment temperatures is required.
When tuning a cascade system, the inner loop must
be tuned first. The inner loop comprises outputs 1A
and 1B and the Analog Input 1 sensor, which usually
measures the energy source temperature. The output
device controls a power switching device, which in
turn switches the heating and cooling. The set point
for the inner loop is generated by the outer loop. For
Process Cascade, this will have a range between the
Cascade Low Range and Cascade High Range.
Cascade Setup Procedure
1. First, configure Analog Input 3, Cascade Low
Range and Cascade High Range.
Go to the Analog Input 3 Menu (Setup Page).
Choose Process or Deviation Cascade. Deviation
Cascade references Channel 1 set point allowing a
range above and below the current control set
point. For Process Cascade control of a heat/cool or
cool only system, set the Cascade Low Range to a
value slightly lower than the lowest temperature
desired in the chamber. For heat-only systems, set
the Cascade Low Range to a value slightly lower
than the ambient temperature; otherwise the heat
output will never turn fully off.
For heat/cool or heat only systems , set the Cas-
cade High Range to a value slightly higher than
the highest temperature desired in the chamber.
For cool-only systems, set the Cascade High Range
to a value slightly higher than the ambient tem-
perature; otherwise the cooling will never fully
turn off.
2. Next, configure the controller to tune and display
data for the outer loop. To view Inner Loop Set
Point in the upper display, go to the Setup Page,
Custom Main Page Menu, select the Inner Set
point as one of the parameters, P1 to P16, to be
displayed in the Main Page.
To also view Analog Input 3 in the upper display,
go to the Setup Page, Process Display Menu, and
choose Alternating. Under Set Display Time,
choose a duration for the display of the Input 1 and
Input 3 variables.
Cascade Autotuning Procedure
1. Go to Setup Page, Custom Main Page Menu.
Choose Tune Status 1 and Tune Status 2 to ap-
pear as 2 of the 16 parameters that can be dis-
played on the Main Page. The Main Page will now
display the status of the autotuning process.
2. Autotune the inner loop. Go to the Autotune PID
Menu (Operations Page), and select Cascade In-
ner-loop. Choose Cascade Inner Loop PID Set 1 to
5, where PID values will be stored after autotun-
ing. Autotuning begins when you choose the PID
set. While autotuning, the F4 controller will con-
trol the energy source in an on-off mode to a tem-
perature equal to the Cascade High Range setting
x Channel 1 Autotune Set Point. For best results,
use proportional control only on the inner loop.
3. Next, autotune the outer loop. Go to the Auto-
tune PID Menu (Operations Page). Choose
Cascade Outer Loop, then choose Outer Loop PID
set 1 to 5, where PID values will be stored after
autotuning. Autotuning begins when you choose
the PID set. While autotuning, the outer loop will
be controlled in an on-off mode at a set point
equal to static set point x Ch 1 Autotune Set
Point. In most cases, the autotuning feature will
tune for acceptable control. If not, manually tune
the outer loop (step 4 below). Before manually
tuning, record the values generated by the auto-
tuning feature.
4. To manually tune the outer loop, go to the Edit
PID Menu (Operations Page). Choose Cascade
Outer Loop, then choose Outer Loop PID set 1 to
5. Begin manual tuning by setting the Propor-
tional Band to 5, Integral (Reset) to 0, and Rate
to 0. Establish the desired set point and let the
system stabilize. When the system stabilizes,
watch the Inner Loop Set Point on the Main
Page. If this value fluctuates, increase the pro-
portional band until it stabilizes. Adjust the pro-
portional band in 3° to 5° increments, allowing
time for the system to stabilize between adjust-
ments.
5. When Input 1 has stabilized, watch the percent
power on the Main Page. It should be stable,
±2%. At this point, the process temperature
should also be stable, but it will exhibit droop
(stabilized below set point). The droop can be
eliminated with Integral (reset).
6. Start with an integral setting of 99.9 minutes,
and allow 10 minutes for the process tempera-
ture to come up to set point. If it has not,
decrease the setting by half and wait another 10
minutes. Then halve the setting again and wait
another 10 minutes until the process value
equals the set point. If the process becomes
unstable, the integral value is too small. Increase
it until the process stabilizes.