Multiiple pid sets, Multiple pid sets, Manual tuning procedure – Watlow Series F4S/D User Manual
Page 21: Multiple tuning procedure
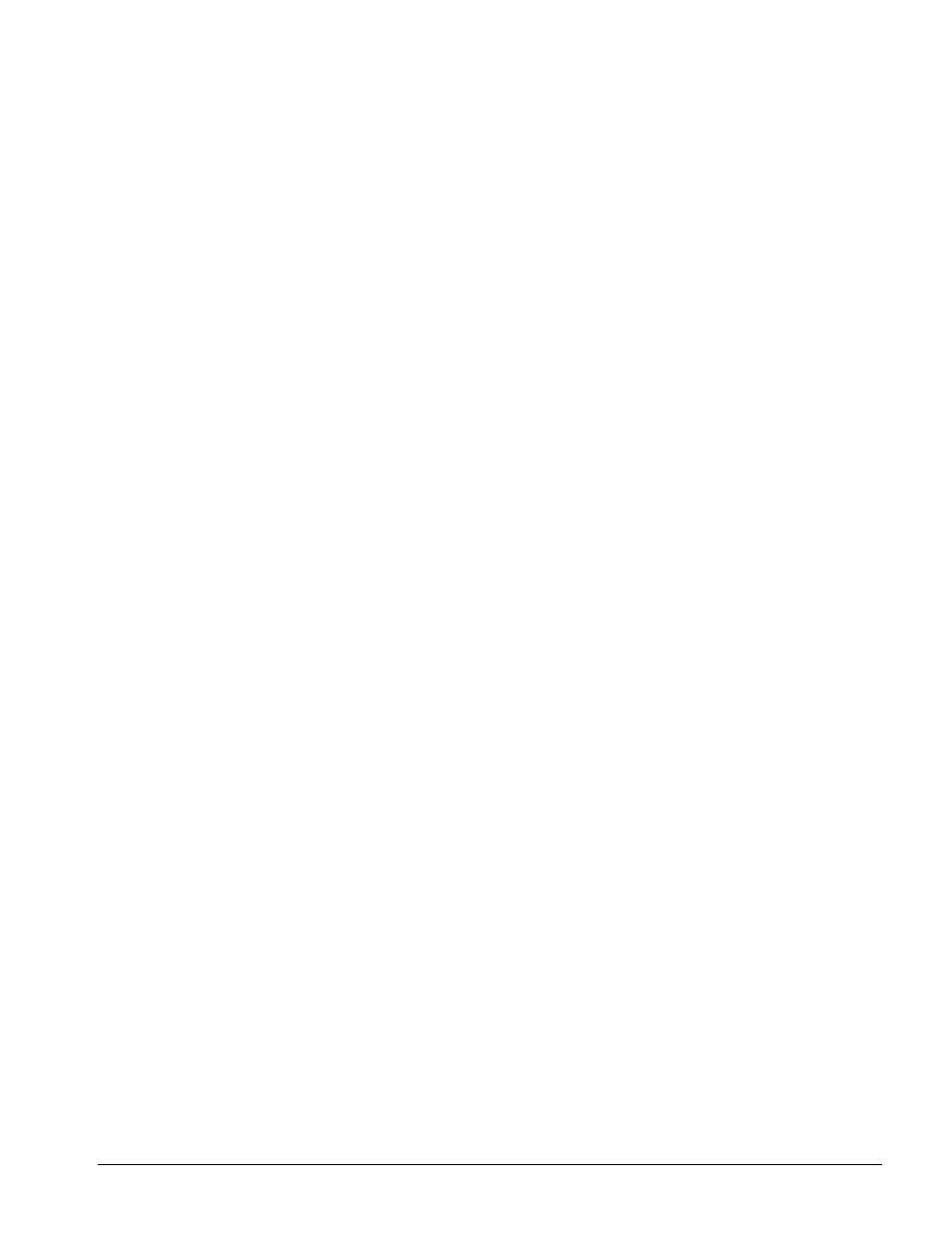
Wa t l o w S e r i e s F 4 S / D
O p e r a t i o n s
■
3 . 5
Integral (Reset):
Define the integral time in min-
utes per repeat; define reset in repeats per minute.
Set repeats per minute if units are U.S.; minutes
per repeat if units are SI.
Derivative (Rate):
Define the derivative (rate)
time in minutes. Large values prevent overshoot
but can cause sluggishness. Decrease if necessary.
Dead Band:
Define the dead band in degrees or
units. Heating dead band shifts the set point down.
Cooling dead band shifts the set point up. For more
information, see the Features Chapter.
Manual Tuning Procedure
1. Apply power to the Series F4 and enter a set
point. Go to the Operations Page, Edit PID Menu
and begin with Proportional Band set to 5; Inte-
gral (Reset) set to 0; Derivative (Rate) set to 0;
and Autotune set to Tune Off.
2. Start manual tuning by entering the desired set
point and let the system stabilize. Once the sys-
tem stabilizes, observe the value of Input 1 on
the Main Page. If the Input 1 value fluctuates,
increase the proportional band setting until it
stabilizes. Adjust the proportional band in 5º to
10º increments, allowing time between adjust-
ments for the system to stabilize.
3. Once Input 1 has stabilized, observe the percent
power on the Main Page. It should be stable,
±2%. At this point, the process temperature
should also be stable, but it will exhibit droop
(stabilized below set point). The droop can be
eliminated with reset or integral.
4. Start with a reset setting of 0.01, and allow 10
minutes for the process temperature to come up
to set point. If it has not, increase the setting to
0.05 and wait another 10 minutes. After this,
double the reset setting and wait another 10
minutes until the process value equals the set
point. If the process becomes unstable, the reset
value is too large. Decrease the setting until the
process stabilizes.
5. Increase Derivative/Rate to 0.10 minute. Then
raise the set point by 20° to 30°F, or 11° to 17°C.
Observe the system's approach to the set point. If
the load process value overshoots the set point,
increase Derivative/Rate to 0.50 minute.
Raise the set point by 20° to 30°F, or 11° to 17°C
and watch the approach to the new set point. If
you increase Derivative/Rate too much, the ap-
proach to the set point will be very sluggish. Re-
peat as necessary until the system rises to the
new set point without overshooting or approach-
ing the set point too slowly.
For additional information about manual tuning
and proportional, integral and derivative control,
see the Features Chapter.
Multiple PID Sets
Environmental chambers, ovens and furnaces typi-
cally have different thermal requirements when
they operate at high and low temperatures or pres-
sures. To accommodate varying thermal require-
ments, the F4 is capable of storing five different
PID sets for each channel. One set for each channel
can be chosen in each profile step.
For example, a controller in an environmental
chamber with PID settings optimized for control at
subzero temperatures may not control well when
the set point is set to temperatures above the boil-
ing point of water. With the F4, one PID set could
be used for subzero operation and another set for
temperatures above boiling.
Multiple Tuning Procedure
1. To auto-tune a single PID set, begin by setting
the static set point on the Main Page.
2. Go to the Autotune PID Menu (Operations Page),
and choose a channel and a set. Autotuning be-
gins when you select the set. The Main Page dis-
plays information about the autotuning process
when Tune Status is selected in the Custom
Main Page.
3. When autotuning is finished, proceed with
another PID set.
In the example above, the user would first auto-
tune a PID set for subzero operation, and then an-
other for operation at boiling temperatures. When
programming a profile, the user could then select a
different PID set for each step, depending on the
thermal requirements.
✔ NOTE:
Autotuning cannot be done while running a profile. It can
only be initiated when the controller is in the Static Set
Point Control mode.