Setting up cascade control, How the secondary set point is determined, Setting up cascade control 69 – Watlow CPC400 User Manual
Page 83
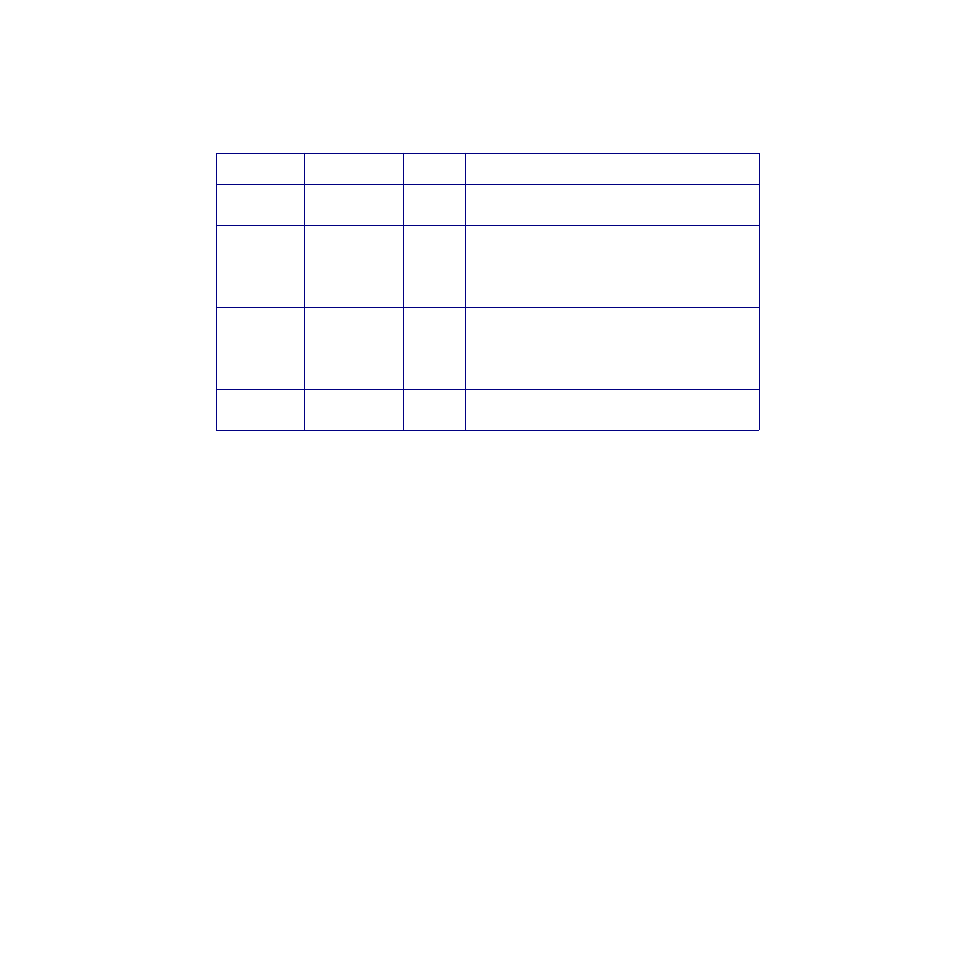
CPC400 Series User’s Guide
Chapter 3: Operation and Setup
Doc. 0600-2900-2000
Watlow Anafaze
69
Table 3.9 shows the parameter setup for this example.
Table 3.9
Parameters Settings for Process
Variable Retransmit Example
To complete this configuration, the output for loop 2 must
be configured to provide the 4 to 20 mA analog signal (via
the Serial DAC) that is required by the data logger.
When setup is completed, the controller will produce an
output on loop 2 which is linear and proportional to the loop
1 process variable.
Setting Up Cascade Control
Cascade control is used to control thermal systems with
long lag times, which cannot be as accurately controlled
with a single control loop. The output of the first (primary)
loop is used to adjust the set point of the second (secondary)
loop. The secondary loop normally executes the actual con-
trol.
Some applications, such as aluminum casting, use two-
zone cascade control where the primary output is used for
the primary heat control and the cascaded output is used
for boost heat. You can use the primary heat output for
both control and for determining the set point of the sec-
ondary loop.
How the Secondary Set Point is Determined
The set point of the secondary loop is determined according
to the heat and cool output values from the primary loop
and user-specified cascade parameters:
Menu
Parameter
Value
Comment
PV retrans
Ht output
retrans
PV 1
Choose to retransmit the loop 1 process variable.
PV retrans
Ht retrans
LowPV
0˚F
This is the input value represented by a 0 percent
output signal. The recorder input is a linear 4 to 20
mA signal representing a range of 0 to 1000°F, so
we will use a 0 percent output signal to represent
0°F.
PV retrans
Ht retrans
HighPV
1000˚F
This is the input value represented by a 100 percent
output signal. The recorder input is a linear 4 to 20
mA signal representing a range of 0 to 1000°F, so
we will use a 100 percent output signal to represent
1000°F.
PV retrans
Cl output
retrans
none
Not using the cool output of loop 2 to retransmit a
process variable.