IAI America ERC2 User Manual
Page 166
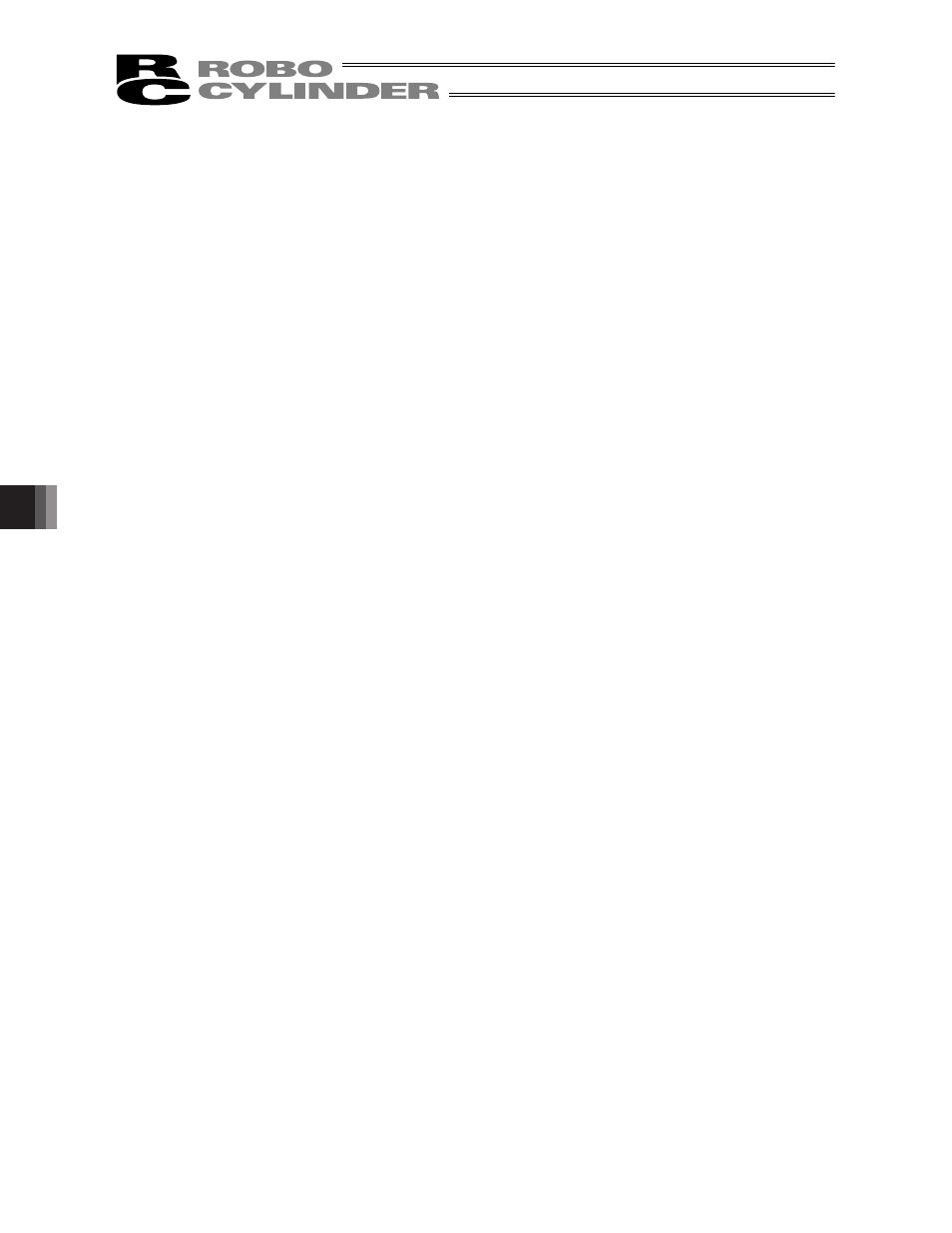
9. T
roubleshooting
143
z
Noise occurs during downward movements in a vertical application.
Cause: The load exceeds the rating.
Action: [1] Decrease the speed.
[2] Decrease the value set in the user parameter No. 7 (Servo gain number). Do not decrease the
parameter setting below “3.”
z
Vibration occurs when the actuator is stopped.
Cause: The slider is receiving an external force.
Action: If the external force cannot be removed, increase the value set in user parameter No. 12 (Current-limiting
value at standstill during positioning).
Increasing this value will cause the holding torque at standstill to increase, so do not increase the
parameter setting above 70%.
z
The actuator overshoots when decelerated to a stop.
Cause: The load inertia is high in view of the balance of load and deceleration.
Action: Decrease the deceleration setting.
z
The home and target positions sometimes shift on the rod-type actuator.
Cause: The added rotational moment to the rod increased the non-rotational accuracy.
Action: The actuator may have to be replaced in some cases. Please contact IAI.
z
The speed is slow during push & hold operation.
Cause: The current-limiting value is lower than what is required in view of the loading mass and slide resistance.
Action: Increase the current-limiting value for push & hold operation.
z
The actuator moves only a half, or as much as twice, the specified travel.
Cause: Pre-shipment setting error at IAI is suspected.
Action: Contact IAI.
z
The actuator operates abnormally when the servo is turned on following the power on.
Cause: The excited phase is not detected correctly when the servo is turned on because of one of the following
conditions at the time of power on:
[1] The slider or rod is contacting the mechanical end.
[2] An excessive external force is exerted to the load.
Action: [1] Check if the slider or rod is contacting the mechanical end. If it is, move the slider/rod away from the
mechanical end. If the actuator is equipped with a brake, move the slider/rod after releasing the brake
by turning on the brake release switch. At this time, pay attention to prevent the load from falling due
to its dead weight and protect your hand, robot, and the work part from injuries/damages.
If the actuator cannot be moved by hand, you can check the direction of excited-phase signal
detection and change the direction, if necessary. If you wish to attempt this course of action, please
contact IAI.
For details, refer to 8.2.2, “Parameters Relating to the Actuator Operating Characteristics.”
[2] Check if the load is in contact with an object in the surroundings. If so, move the load away from the
obstruction to provide a minimum clearance of 1 mm.
If neither of causes [1] and [2] is present, please contact IAI.
z
The LED (green) blinks.
The automatic servo-off mode is currently active. (This is not an error or failure.)