5 specific problems – IAI America ERC2 User Manual
Page 165
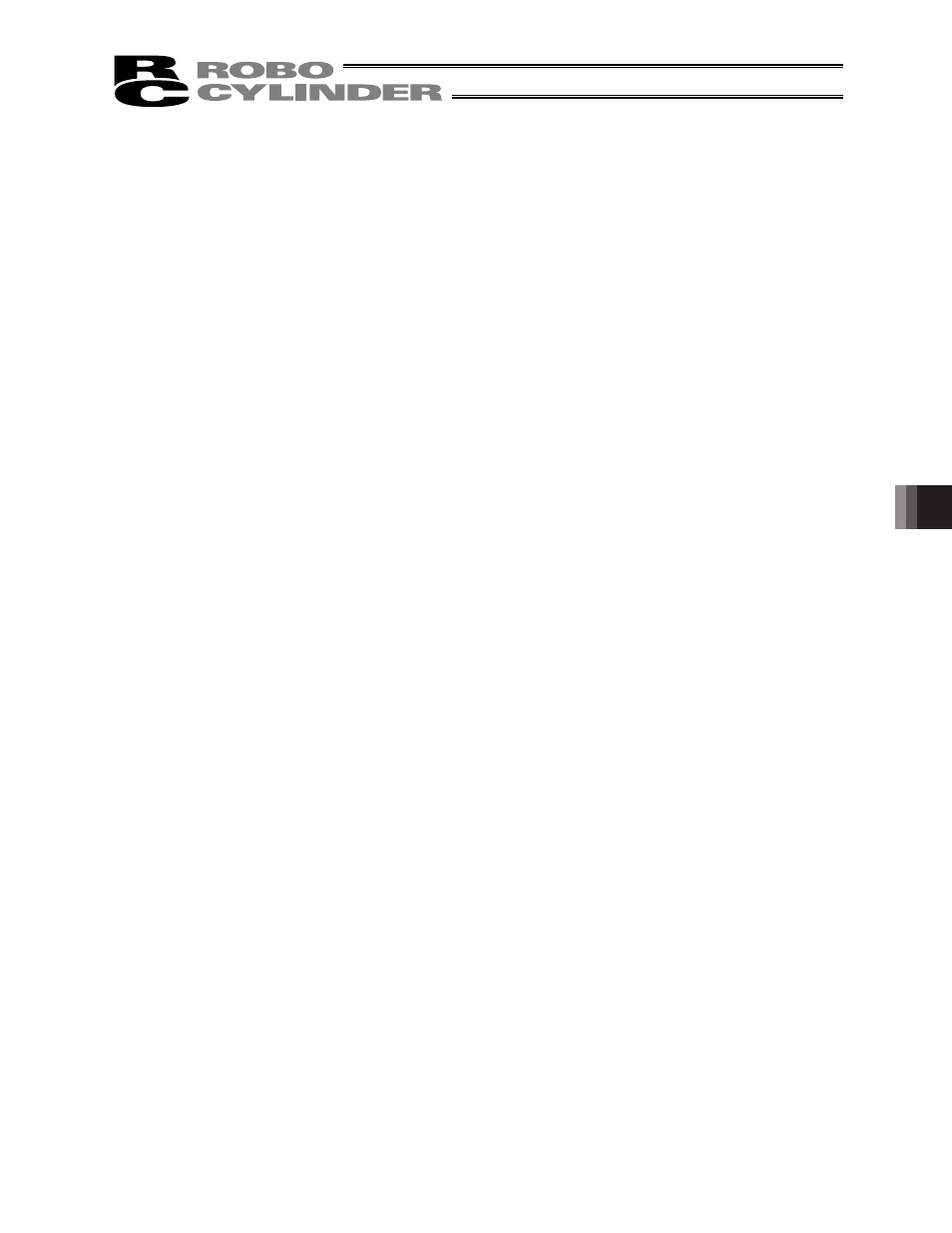
9. T
roubleshooting
142
9.5 Specific Problems
z
I/O signals cannot be exchanged with the PLC.
Cause: [1] The 24-V I/O power supply is connected in reverse.
(This will not affect the input circuits, but the output circuits may be damaged.)
[2] If the problem is with an output circuit, a circuit component may have been damaged due to a large
load that caused the current flowing into the circuit to exceed the maximum level.
[3] Contact failure in the connector or relay terminal block on the PLC end.
Action: Check the connection condition of the power supply and connector, as well as the load on the output side.
If the cause is identified as [1] or [2], the controller board must be replaced. Please contact IAI.
z
The LED lamp does not illuminate after the power is input.
Cause: [1] Reverse connection of the 24-V power supply
[2] Faulty controller board
If the power supply is connected properly, probably the controller board is faulty. Please contact IAI.
(Note) If the 24-V power supply is connected in reverse, the controller may not fail immediately but
its service life will likely be shortened.
z
The LED illuminates in red when the power is turned on.
(An alarm is present or the motor drive power is cut off.)
Check on the I/O monitor screen of the PC or teaching pendant if the alarm signal (*ALM) is output.
If the alarm signal is output, check the description of the error and remove the cause.
If alarm code 41 (motor voltage drop) is displayed, it means the motor drive power is cut off. Check the following
items:
[1] Is the emergency-stop switch on the operation panel pressed? Also confirm that the necessary interlocks are
released.
[2] Is the emergency-stop switch on the teaching pendant pressed?
[3] If a SIO converter is used, is the PORT switch turned ON when a teaching pendant is not connected?
z
Home return ends in the middle in a vertical application.
Cause: [1] The load exceeds the rating.
[2] The ball screw is receiving torsional stress due to the affixing method of the actuator, tightening of
bolts only on one side, etc.
[3] The slide resistance of the actuator itself is large.
Action: [1] Increase the value set in user parameter No. 13 (Current-limiting value during home return).
Increasing this value will cause the home return torque to increase, so do not increase the parameter
setting above 75%.
[2] Loosen the fixing bolts and check if the slider moves smoothly.
If the slider moves smoothly, review the affixing method and bolt tightening condition.
[3] If the slide resistance of the actuator itself is large, please contact IAI.