1 how to start – IAI America ERC2 User Manual
Page 117
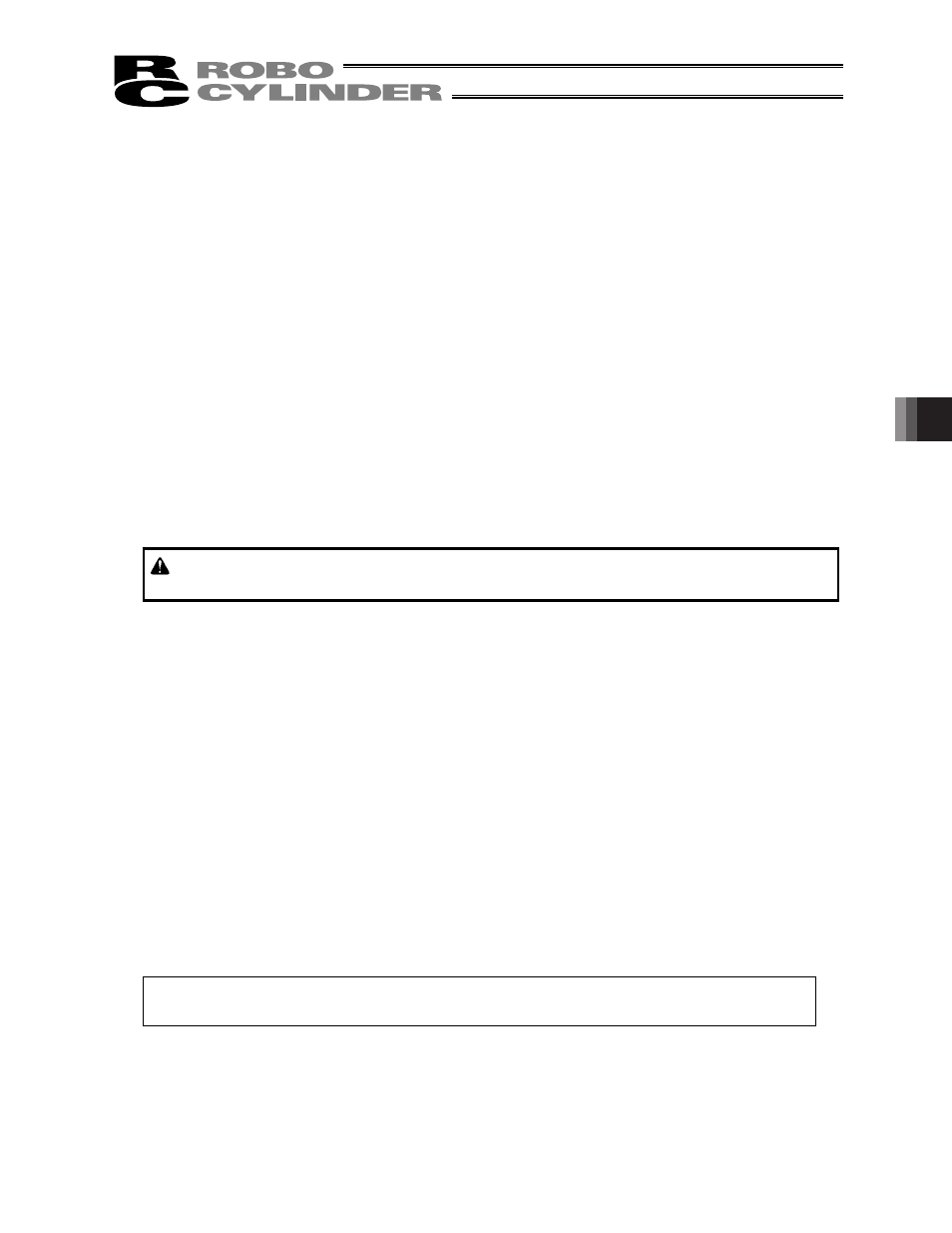
0
7. O
pe
ra
tio
n i
n t
he
“8
P
oin
ts
” a
nd
“1
6 P
oin
ts
” M
od
es
<
Pr
ac
tic
al O
pe
ra
tio
n>
94
7. Operation in the “8 Points” and “16 Points” Modes Operation> 7.1 How to Start (1) Confirm that the connector end (CN1) of the extension cable is firmly plugged into the connector on the actuator cable. (2) Connect the PLC and the parallel I/O. (3) If the actuator has a brake, set the brake release switch to OFF. (4) Supply 24 VDC to the control power supply. Cut off the motor-drive power supply (actuate an emergency stop) beforehand. (5) Confirm that the slider or rod is not contacting the mechanical end. If the slider or rod is contacting the mechanical end, or when the slider or rod is positioned between the mechanical end and home, move the slider/rod away from the home position toward the direction opposite to the mechanical end. If the actuator is equipped with a brake, move the slider/rod after releasing the brake by turning on the brake release switch. At this time, pay attention to prevent the load from falling by its dead weight and protect your hand, robot, and the work part from injuries/damages. If the screw lead is too short and the actuator cannot be moved by hand, change the setting of parameter No. 28, “Direction of excited-phase signal detection” to the direction opposite to the mechanical end. Warning: Turning on the servo while the slider or rod is still contacting the mechanical end may disable accurate detection of the excited phase, resulting in malfunction or excitation detection error. (6) Connect a PC or teaching pendant and set the minimum parameters required. x If the pause input is not used, set parameter No. 15 “Pause input disable selection” to “1.” x To select “16 points,” set parameter No. 25 “PIO pattern selection” to “2” or “3.” (This setting is required.) For details, refer to 8, “Parameter Settings.” (7) Cancel the emergency stop so that the motor drive power will be supplied. The controller servo will be turned on and a green LED lamp will illuminate on the motor cover. (8) If the pause signal (*STP) is enabled, turn the signal ON from the PLC. The position complete output (PEND) will turn ON. A red LED lamp indicates an alarm. Remove the cause of the alarm. For details, refer to 9, “Troubleshooting.” (9) Perform home return. z Overview of operation on the teaching pendant x On the RCM-T, select the Edit/Teach screen, bring the cursor to *Home in the sub-display area, and then press the ENTER key. x On the RCM-E, select the Teach/Play screen, scroll the pages until *Home Return is shown, and then press the ENTER key. z Overview of operation in the PC software In the main window, select the applicable position data, and then click Home. For details of each operation, refer to the operation manual for the applicable teaching pendant or PC software.