1 troubleshooting problems with no alarm display – Yaskawa Sigma II Indexer User Manual
Page 173
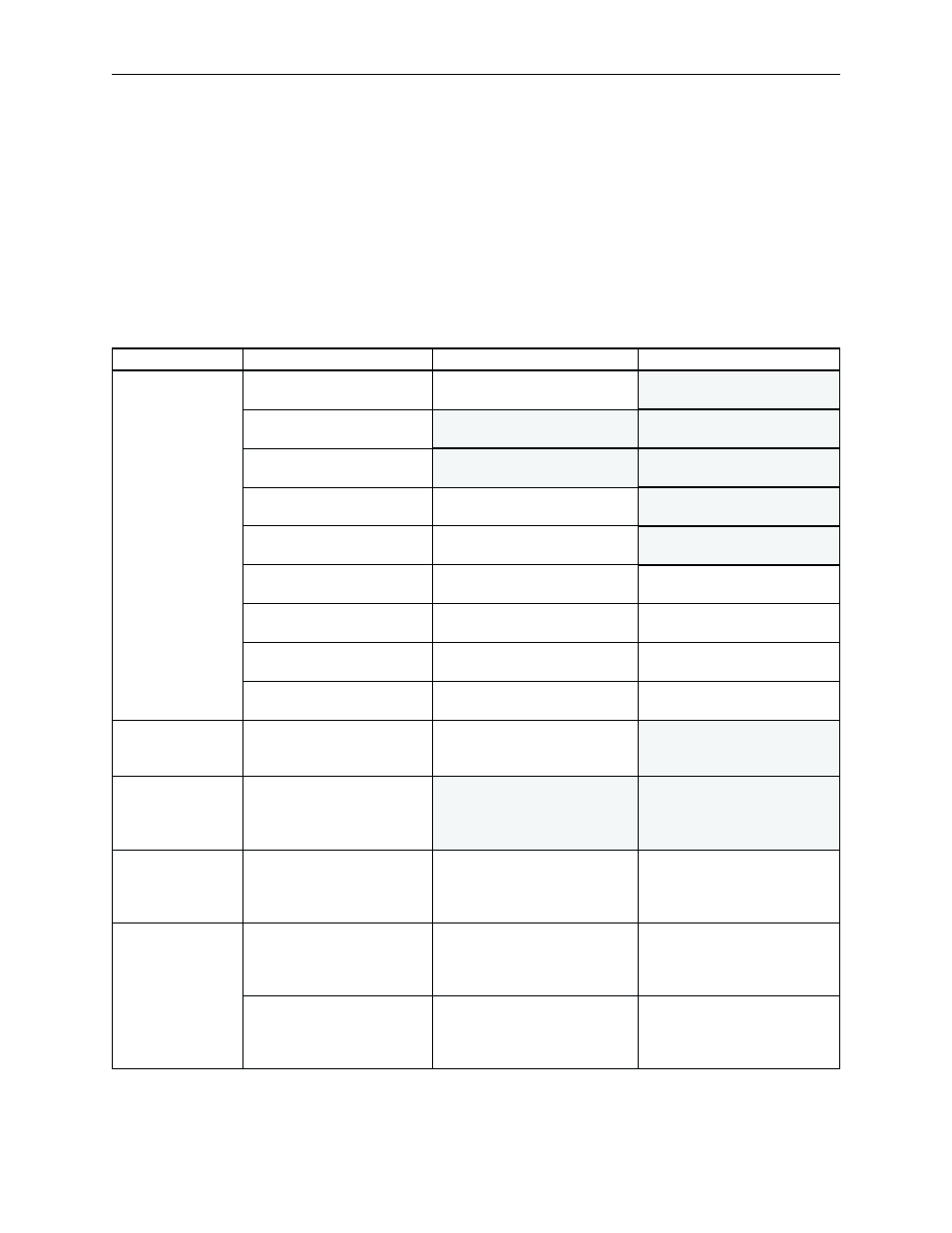
Sigma II Indexer User’s Manual
Troubleshooting Problems with No Alarm Display
9-2
9.1 Troubleshooting Problems with No Alarm Display
Use the tables below to identify the cause of a problem that causes no alarm display and fol-
low the described corrective procedure.
Turn OFF the servo system power supply before starting the shaded procedures.
Contact Yaskawa if the problem cannot be solved by carefully following the described pro-
cedure.
Table 9.1: Troubleshooting Table with No Alarm Display
Symptom
Cause
Comment
Solution
Servomotor does
not start
Power not connected
Check voltage between power
supply terminals.
Correct the power circuit.
Loose connection
Check terminals of connectors
(CN1, CN2, CN4, CN6).
Tighten any loose parts.
Connector (CN1, CN4, CN6)
external wiring incorrect
Check connector (CN1, CN4,
CN6) external wiring
Refer to connection diagram and
correct wiring.
Servomotor or encoder wir-
ing disconnected.
–––
Reconnect wiring
Overloaded
Run under no load.
Reduce load or replace with
larger capacity servomotor.
Servo not enabled
–––
Turn /S-ON input ON or use the
SVON command
P-OT and N-OT inputs are
turned OFF.
Refer to section 5.2.2.
Turn P-OT and N-OT input sig-
nals ON.
Software position limit (P-LS
or N-LS) reached.
Check error code from JUSP-
NS600
Check position of motor and
move off of the position limit.
No position reference
Check error code from JUSP-
NS600
Reserve a position reference
before a program start.
Servomotor moves
suddenly, then
stops
Servomotor or encoder wir-
ing incorrect.
–––
Refer to Chapter 3 of Sigma II
Servo System User’s Manual.
Unstable servomo-
tor speed.
Defective wiring connection
to the motor.
Check the connections of the
power lead (U-, V-, and W-
phases) and the encoder connec-
tors.
Tighten any loose terminals or
connectors
Servomotor
vibrates at approxi-
mately 200 to
400Hz.
Speed loop gain value too
high.
–––
Reduce speed loop gain (Pn100)
preset value.
High rotation speed
overshoot on start-
ing and stopping.
Speed loop gain value too
high.
–––
Reduce speed loop gain (Pn100)
preset value.
Increase integration time con-
stant (Pn101).
Speed loop gain is too low
compared to position loop
gain.
–––
Increase the value of parameter
Pn100 (speed loop gain).
Reduce the integration time con-
stant (Pn101).