HEIDENHAIN TNC 640 (34059x-05) Cycle programming User Manual
Page 461
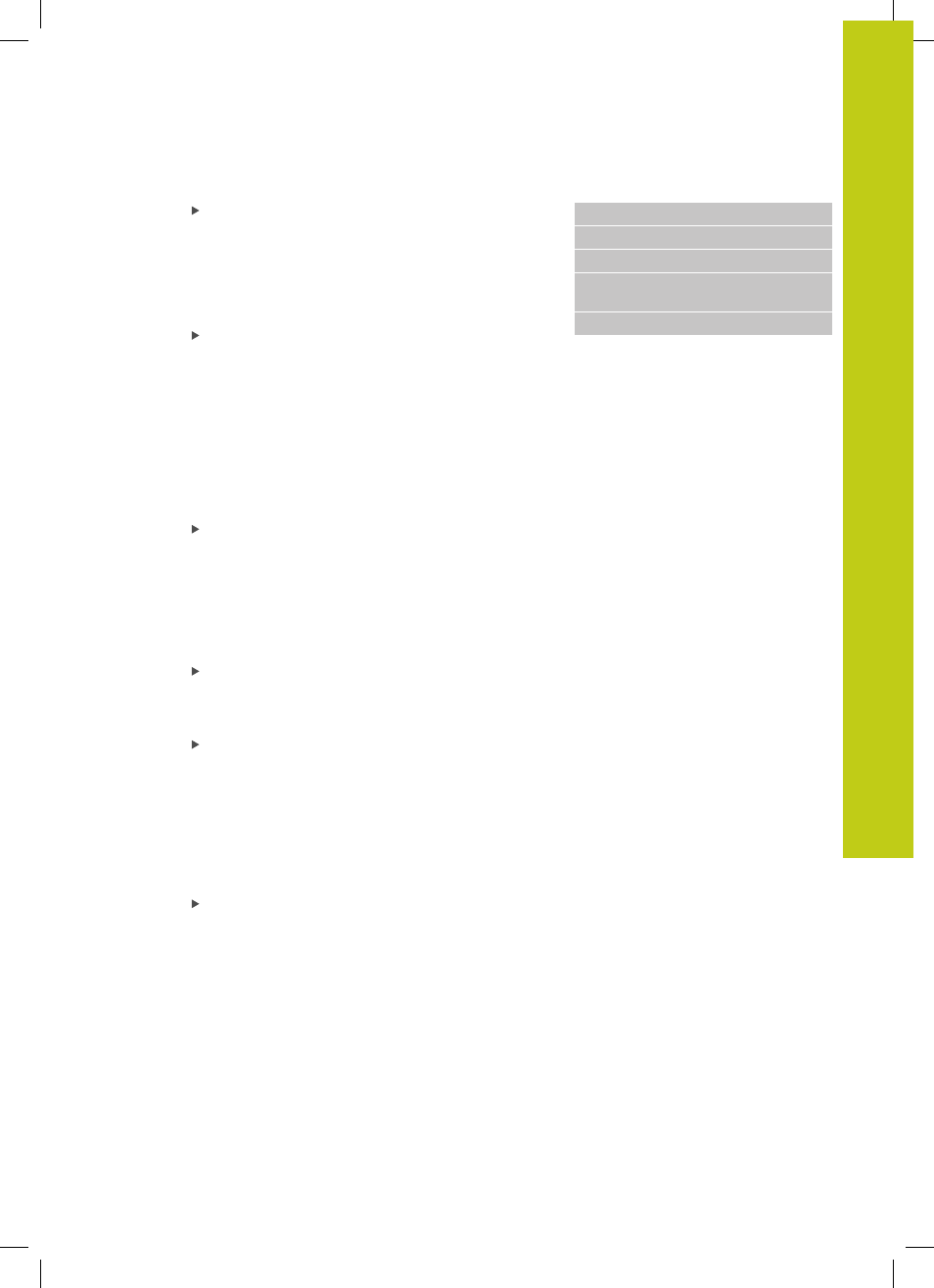
BASIC ROTATION compensation via rotary axis (Cycle 403, DIN/
ISO: G403)
14.5
14
TNC 640 | User's Manual Cycle Programming | 1/2015
461
Traversing to clearance height Q301: definition
of how the touch probe is to move between the
measuring points:
0
: Move at measuring height between measuring
points
1
: Move at clearance height between measuring
points
Axis for compensation movement Q312:
Assignment of the rotary axis in which the TNC is to
compensate the measured misalignment:
0
: Automatic mode – the TNC uses the active
kinematics to determine the rotary axis to be
aligned. In automatic mode the first rotary table
axis (as viewed from the workpiece) is used as
compensation axis. Recommended setting.
4
: Compensate misalignment with rotary axis A
5
: Compensate misalignment with rotary axis B
6
: Compensate misalignment with rotary axis C
Set to zero after alignment Q337: Define whether
the TNC should set the angle of the aligned rotary
axis to 0 in the preset table or in the datum table
after the alignment:
0
: Do not set the angle of the rotary axis to 0 in the
table after alignment
1
: Set the angle of the rotary axis to 0 in the table
after alignment
Number in table Q305: Enter the number in the
preset table/datum table in which the TNC is to set
the rotary axis to zero. Only effective if Q337 is set
to 1. Input range 0 to 99999
Measured value transfer (0, 1) Q303: Specify if
the determined basic rotation is to be saved in the
datum table or in the preset table:
0
: Write the measured basic rotation as datum shift
active datum table. The reference system is the
active workpiece coordinate system
1
: Write the measured basic rotation into the
preset table. The reference system is the machine
coordinate system (REF system).
Reference angle? (0=ref. axis) Q380: Angle with
which the TNC is to align the probed straight line.
Only effective if rotary axis = automatic mode is
selected, or rotary axis = C is selected (Q312 = 0 or
6). Input range -360.000 to 360.000
Q312=0
;COMPENSATION AXIS
Q337=0
;ZERO RESET
Q305=1
;NO. IN TABLE
Q303=+1
;MEAS. VALUE
TRANSFER
Q380=+90
;REFERENCE ANGLE