Cycle run – HEIDENHAIN TNC 640 (34059x-05) Cycle programming User Manual
Page 286
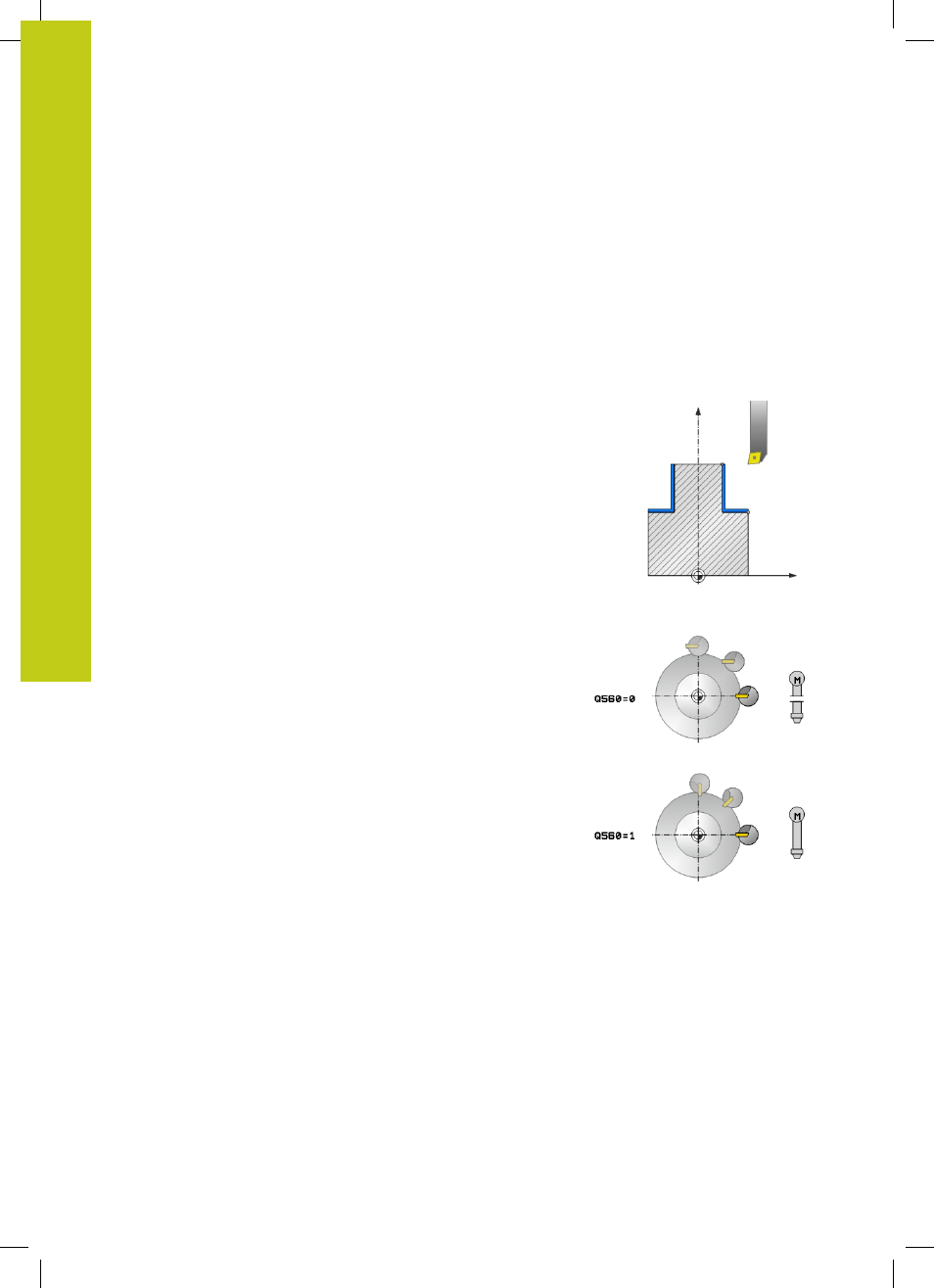
Cycles: Special Functions
11.6
CONTOUR TURNING INTERPOLATION (Cycle 292, DIN/ISO: G292,
software option 96)
11
286
TNC 640 | User's Manual Cycle Programming | 1/2015
11.6
CONTOUR TURNING
INTERPOLATION (Cycle 292, DIN/
ISO: G292, software option 96)
Cycle run
Cycle 292 CONTOUR TURNING INTERPOLATION couples the
tool spindle to the position of the linear axes. This cycle enables
you to machine specific rotationally symmetrical contours in
the active working plane. You can also run this cycle in the tilted
working plane. The center of rotation is the starting point in the
working plane at the time the cycle is called. Cycle 292 CONTOUR
TURNING INTERPOLATION is run in milling mode and is CALL-
active. After executing this cycle, the TNC deactivates the spindle
coupling again.
Before using Cycle 292, you first need to define the desired
contour in a subprogram and refer to this contour with Cycle 14 or
SEL CONTOUR. Program the contour either with monotonically
decreasing or monotonically increasing coordinates. Undercuts
cannot be machined with this cycle. By entering Q560=1 you can
turn the contour; a cutting edge of the tool is oriented to the center
of a circle. When you enter Q560=0 you can mill the contour; the
spindle is not oriented in this case.
Cycle run, Q560=1: Contour turning
1 The TNC first stops the spindle (M5).
2 The TNC orients the tool spindle to the specified center of
rotation. The specified angle Q336 is taken into account. If
defined, the "ORI" value from the turning tool table (toolturn.trn)
is also considered.
3 The tool spindle is now coupled to the position of the linear
axes. The spindle follows the nominal position of the reference
axes.
4 The TNC positions the tool to the contour start radius Q491,
taking the selected machining operation inside/outside Q529
and the clearance to side Q357 into account. The described
contour is not automatically extended by a set-up clearance.
An extension of the contour must be programmed in the
subprogram. At the beginning of the machining operation, the
TNC positions the tool at rapid traverse in the tool axis direction
to the contour starting point!
Make sure that there is no
material at the contour starting point!
5 The TNC uses interpolation turning to machine the defined
contour. In interpolation turning the linear axes of the working
plane move on a circle, whereas the spindle axis is oriented
perpendicularly to the surface.
6 At the end point of the contour, the TNC retracts the tool
perpendicularly by the set-up clearance.
7 Finally, the TNC retracts the tool to the clearance height.
8 The TNC now automatically deactivates the coupling of the tool
spindle to the linear axes.