HEIDENHAIN TNC 640 (34059x-05) Cycle programming User Manual
Page 308
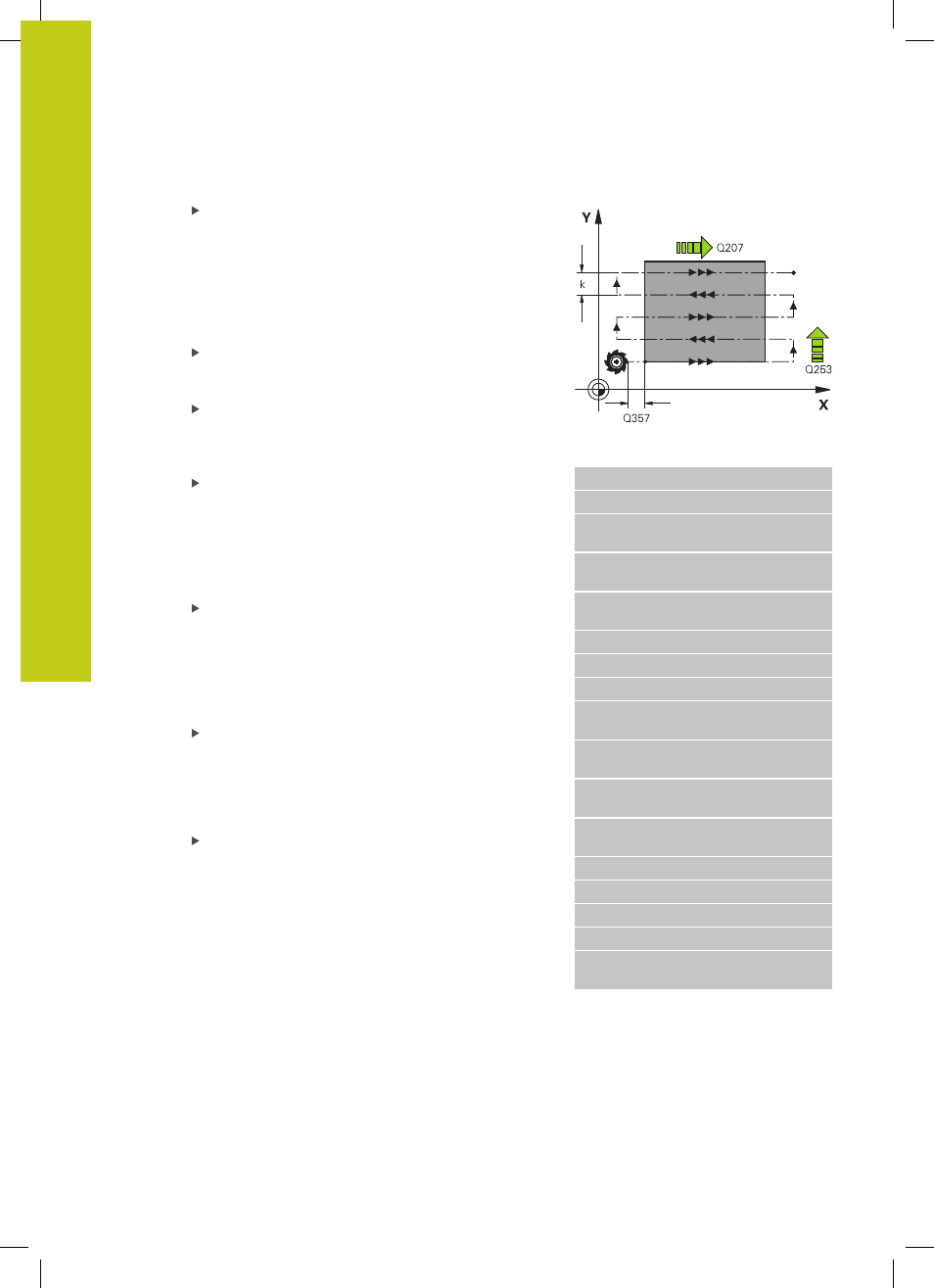
Cycles: Special Functions
11.9
FACE MILLING (Cycle 232, DIN/ISO: G232)
11
308
TNC 640 | User's Manual Cycle Programming | 1/2015
Max. path overlap factor Q370:
Maximum
stepover factor k. The TNC calculates the actual
stepover from the second side length (Q219) and
the tool radius so that a constant stepover is used
for machining. If you have entered a radius R2
in the tool table (e.g. tooth radius when using a
face-milling cutter), the TNC reduces the stepover
accordingly. Input range 0.1 to 1.9999
Feed rate for milling Q207: Traversing speed of
the tool in mm/min while milling. Input range 0 to
99999.999 alternatively
FAUTO, FU, FZ
Feed rate for finishing Q385: Traversing speed of
the tool in mm/min, while milling the last infeed.
Input range 0 to 99999.9999; alternatively
FAUTO,
FU, FZ
Feed rate for pre-positioning Q253: Traversing
speed of the tool in mm/min when approaching
the starting position and when moving to the next
pass. If you are moving the tool transversely to
the material (Q389=1), the TNC moves the tool
at the feed rate for milling Q207. Input range 0 to
99999.9999, alternatively
FMAX, FAUTO
Set-up clearance Q200 (incremental): Distance
between tool tip and the starting position in the
tool axis. If you are milling with machining strategy
Q389=2, the TNC moves the tool at the set-up
clearance over the current plunging depth to the
starting point of the next pass. Input range 0 to
99999.9999
Clearance to side Q357 (incremental): Safety
clearance to the side of the workpiece when
the tool approaches the first plunging depth,
and distance at which the stepover occurs if the
machining strategy Q389=0 or Q389=2 is used.
Input range 0 to 99999.9999
2nd set-up clearance Q204 (incremental):
Coordinate in the spindle axis at which no collision
between tool and workpiece (fixtures) can occur.
Input range 0 to 99999.9999; alternatively
PREDEF
NC blocks
71 CYCL DEF 232 FACE MILLING
Q389=2
;STRATEGY
Q225=+10
;STARTNG PNT 1ST
AXIS
Q226=+12
;STARTNG PNT 2ND
AXIS
Q227=+2.5
;STARTNG PNT 3RD
AXIS
Q386=-3
;END POINT 3RD AXIS
Q218=150
;FIRST SIDE LENGTH
Q219=75
;2ND SIDE LENGTH
Q202=2
;MAX. PLUNGING
DEPTH
Q369=0.5
;ALLOWANCE FOR
FLOOR
Q370=1
;MAX. TOOL PATH
OVERLAP
Q207=500
;FEED RATE FOR
MILLING
Q385=800
;FINISHING FEED RATE
Q253=2000
;F PRE-POSITIONING
Q200=2
;SET-UP CLEARANCE
Q357=2
;CLEARANCE TO SIDE
Q204=2
;2ND SET-UP
CLEARANCE