Flying start (synch motor), Tachometer/encoder option – Rockwell Automation 7000L PowerFlex Medium Voltage AC Drive (C Frame) - Classic Control User Manual
Page 336
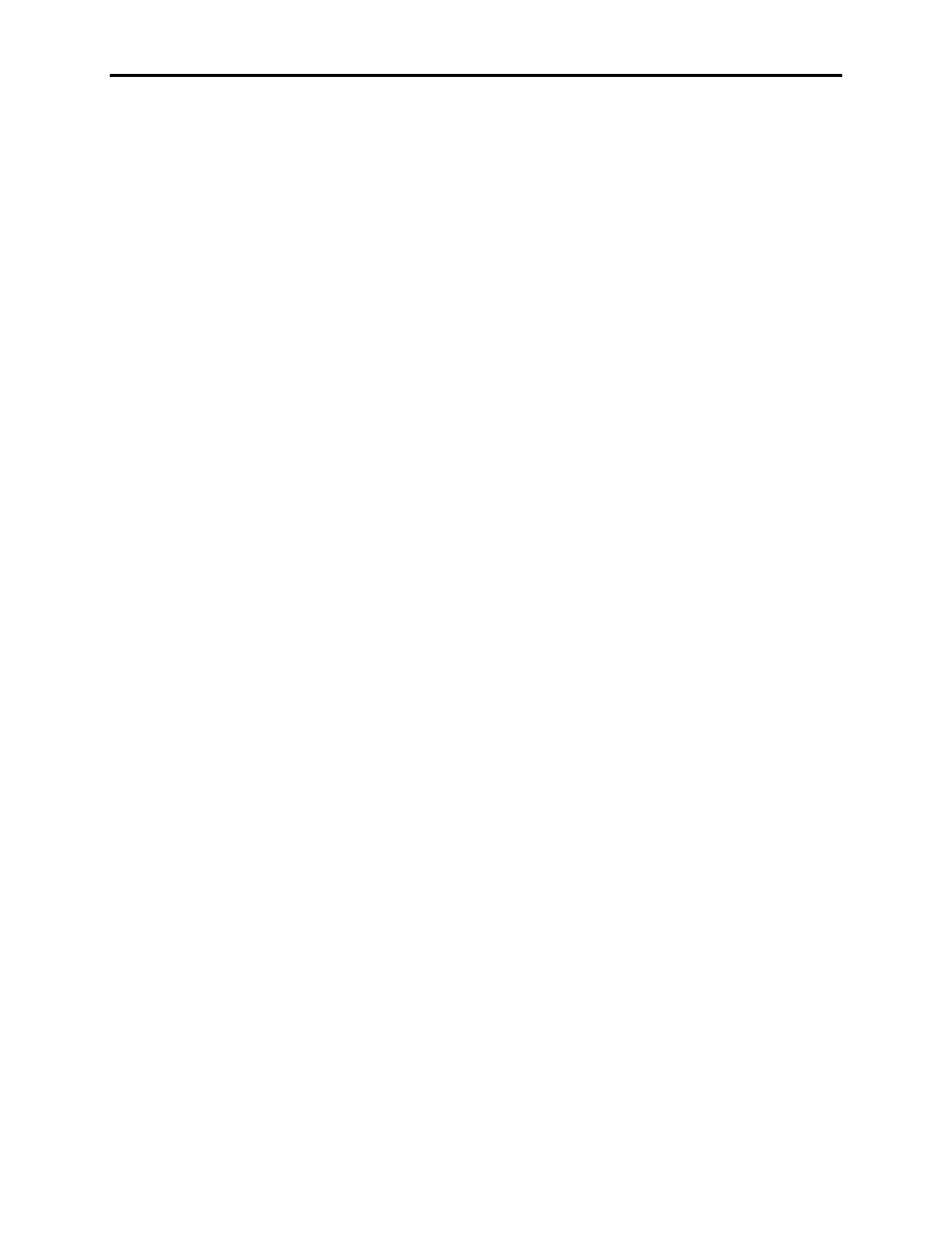
5-28
Functional Description
7000L-UM300I-EN-P – June 2013
7000 “C” Frame
Flying Start (Synch Motor)
With a synchronous motor, flying start is much quicker and more
reliable because a detectable stator voltage is produced whenever the
field is applied and the motor is rotating, even with zero stator current.
When the drive is started, rated field current is applied to the motor
but the stator current remains at zero until the end of the ramp start
delay to allow the rotor flux to build up. If the stator frequency is
greater than about 2 Hz, sufficient stator voltage is generated to
allow the drive to detect the speed and direction of the motor and
synchronize itself to the motor flux. If the flux feedback does not
reach the level specified by parameter Flux minimum (156) the drive
assumes that the motor is stationary and starts from zero frequency.
If an optional position encoder is installed, a flying start can be
performed for any speed or direction of rotation.
Tachometer/Encoder Option
The optional tachometer/encoder provides two significant
enhancements to the drive control:
1. Provides an accurate measurement of motor speed at all times
2. Extends closed loop speed and torque control down to nearly
zero speed.
A pulse tachometer, also called a pulse generator or incremental
encoder, produces a pulse train output with a frequency proportional
to shaft speed. The machine side Signal Conditioning Board
(SCBM) provides optically isolated inputs for a quadrature pulse
tachometer. Single-phase tachometer can be also be used if reverse
rotation never occurs. Parameter Tach Type (233) specifies which
type is used.
Dividing the number of tach pulses by the sampling period yields the
tach output frequency, from which the shaft speed can be calculated
using the tach pulses per revolution (ppr) specified by parameter
Tach pulse/rev (234). The tach resolution determines the minimum
motor speed that can be measured. If high starting torque or very low
speed operation is required, a high resolution such as 1024 or 2048 ppr
must be provided. Otherwise, a low resolution such as 240 or 360 ppr
is adequate.
The analog flux signal is not usable for stator frequencies less than
about 3 Hz. To control flux and torque at low speeds, the PowerFlex
7000 drive switches to current model based on indirect vector control.
With indirect control, the position of the rotor flux is not directly
measured but is indirectly predicted by adding the calculated slip
angle to the measured rotor angle. The rotor angle is obtained by
integrating the output of the pulse tach (the zero position is arbitrary).