9300 servo plc, Appendix – Lenze DDS Target 9300 Servo PLC V8.x User Manual
Page 120
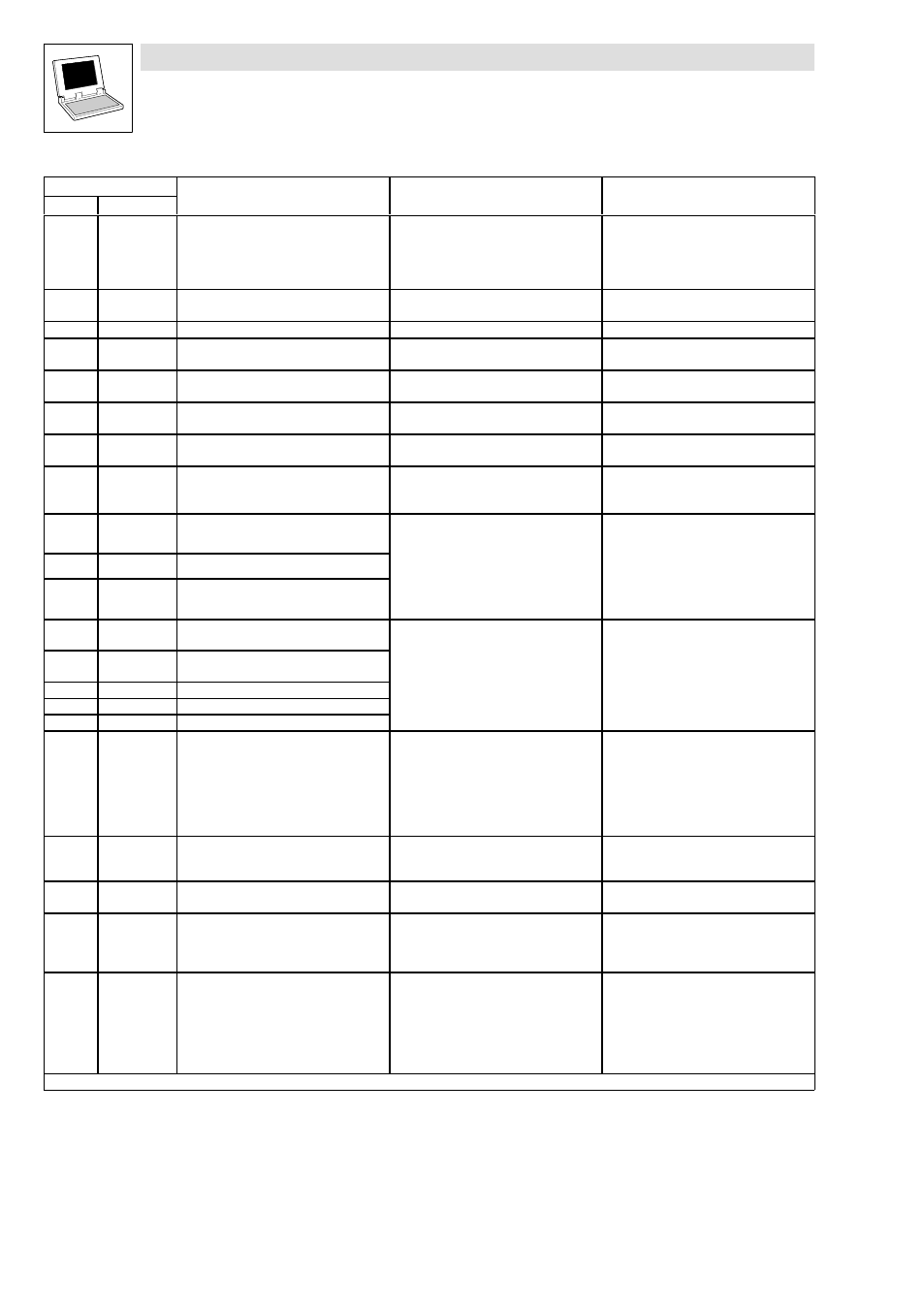
9300 Servo PLC
Appendix
3−114
L
9300 Servo PLC EN 5.1
Fault message
Remedy
Cause
Description
No.
Remedy
Cause
Description
Display
x089
PL
Error during rotor position adjustment
·
Sd7 fault during rotor position
adjustment with absolute value encoder
after mains switching
·
Cancellation of rotor position adjustment
(e.g. by C0095 = 0 or switching off)
1. Activate rotor position adjustment with
C0095 = 1.
2. Carry out TRIP reset.
3. Repeat rotor position adjustment.
x091
EEr
External monitoring has been triggered via
DCTRL.
A digital signal assigned to the TRIP−SET
function has been activated.
·
Check external encoder.
·
Switch off the monitoring (C0581 = 3).
0105
H05
Internal fault (memory)
Contact Lenze.
0107
H07
Internal fault (power stage)
During initialisation of the controller, an
incorrect power stage was detected.
Contact Lenze.
x110
H10
Heatsink temperature sensor error
Sensor for detecting the heatsink
temperature indicates undefined values.
·
Contact Lenze.
·
Switch off the monitoring (C0588 = 3).
x111
H11
Temperature sensor error: Temperature
inside the controller
Sensor for detecting the internal
temperature indicates undefined values.
·
Contact Lenze.
·
Switch off the monitoring (C0588 = 3).
x190
nErr
Speed control error
(Speed out of tolerance margin (C0576))
·
Active load (e.g. for hoists) is too high.
·
Mechanical blockades on the load side
Check drive dimensioning.
x200
NMAX
Maximum system speed (C0596) has been
exceeded.
·
Active load (e.g. for hoists) is too high.
·
Drive is not speed−controlled, torque is
excessively limited.
·
Check drive dimensioning.
·
Increase torque limit, if necessary.
·
Switch off monitoring (C0607 = 3).
0201
overrun
Task1
Time−out in task 1 (ID 2)
Task processing takes longer than the
monitoring time set.
·
Adjust the length of the task runtime.
·
Adjust monitoring time.
·
Determine the cause of time−out by
checking the task runtime at the task
monitor.
·
Swap out time−critical program parts in
a slower task.
...
...
...
0208
overrun
Task8
Time−out in task 8 (ID 9)
0209
float
Sys−T
Float error in system task (ID 0)
Error in real calculation
(e. g. division by 0)
Check calculations (program code).
0210
float
Cycl.−T
Float error in cyclic task (PLC_PRG ID 1)
0211
float Task1
Float error in task 1 (ID 2)
...
...
...
0218
float Task8
Float error in task 8 (ID 9)
0219
overrun
Cyc.−T
Time−out in cyclic task (PLC_PRG ID 1)
Task processing takes longer than the
monitoring time set.
·
Adjust the length of the task runtime.
·
Adjust monitoring time.
·
Determine the cause of time−out by
checking the task runtime at the task
monitor.
·
Swap out time−critical program parts in
a slower task.
0220
noT−Fkt
Credit
Not enough technology units available.
A program with technology functions has
been tried to be loaded to a controller not
providing the corresponding units.
·
Use technology variant of the controller.
·
Contact Lenze, if necessary.
0230
No
Program
Missing PLC program
No PLC program loaded.
Load PLC program.
0231
Unallowed
Lib
PLC program calls invalid library function.
In the PLC program a library function has
been called which is not supported by the
controller (e.g. because the corresponding
hardware is missing).
·
Remove library function or ensure that
the corresponding hardware is available.
·
Contact Lenze, if necessary.
0232
NoCam
Data
Motion profiles (cam data) are not available. When calling functions of the function
library LenzeCamControl.lib it was
detected that there are no motion profiles
(CAM data) loaded in the memory of the
controller.
·
Ensure that the valid cam data has been
attached to the project via the DDS CAM
support.
·
Reload the PLC program into the
controller. (Possibly the command
Online
WReset (origin) has been
executed in DDS.)
x: 0 = TRIP, 1 = Message, 2 = Warning, 3 = FAIL−QSP