Model 3060e – Teledyne 3060e - Ultra Trace oxygen analyzer User Manual
Page 46
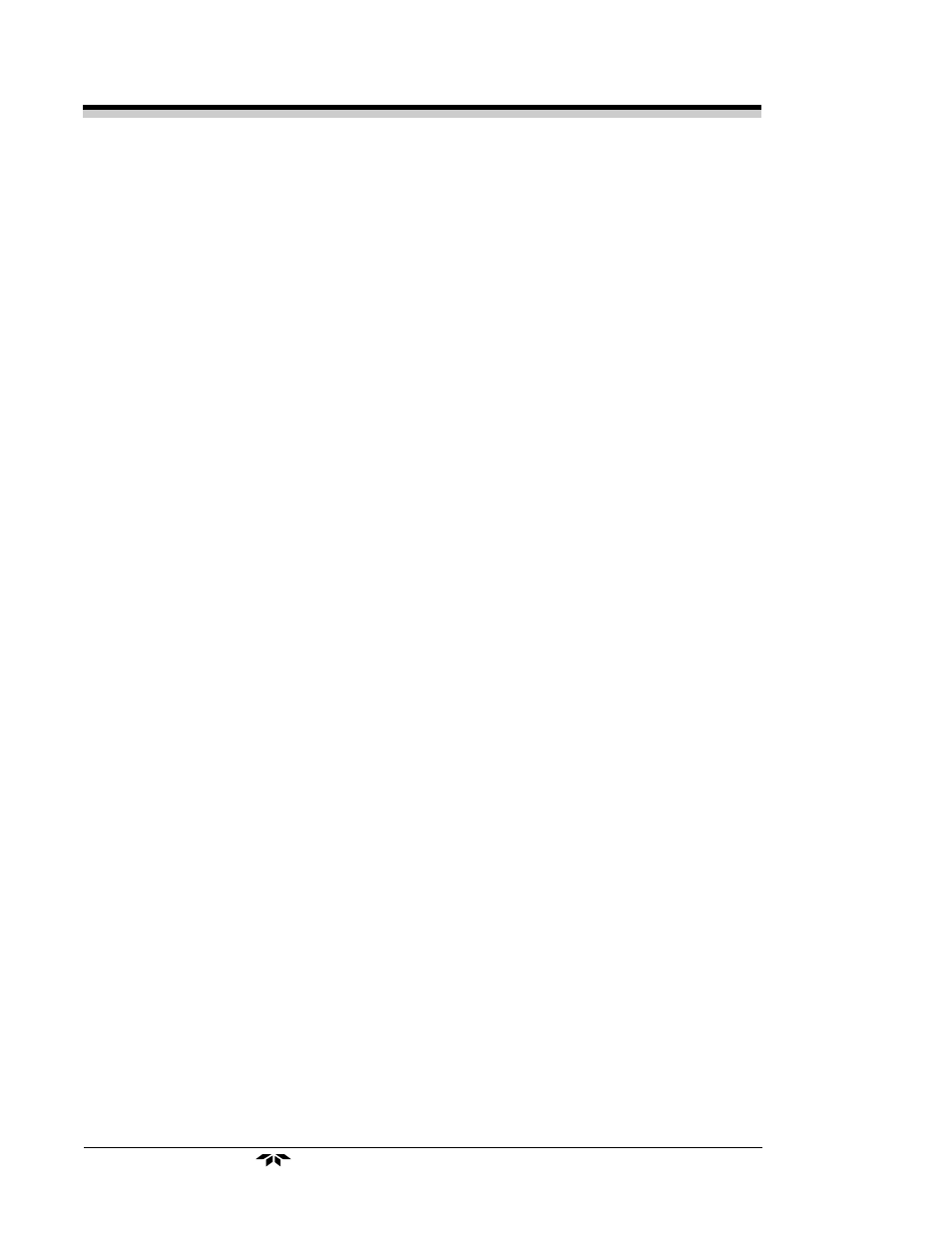
3-20
Model 3060E
Model 3060E
Model 3060E
Model 3060E
Model 3060E
Chapter 3
Chapter 3
Chapter 3
Chapter 3
Chapter 3
Teledyne Electronic Technologies
Analytical Instruments
2. Sparger Vent
The sparger vent transports the oxygen-contaminated gas out of the
system after it leaves the Ultra Trace sensor. The sparge gas vent is
routed through the water reservoir (gas flows above water) to purge
out any oxygen in the water reservoir.
3. Sample Gas In
Hook up the sample gas to the sample gas inlet. Switch the gas
selector on the front panel to the appropriate sample gas coming
into the system: N
2
, Ar, H
2
or He. When the sample gas flows
through the oxygen scrubber, the sample gas becomes the zero gas
and can be used for calibration.
4. Sample Bypass Out
The bypass vent allows a part of the sample gas to come out of the
sample system without entering the Ultra Trace sensor, decreasing
the response and recovery times of the analyzer. The bypass vent is
set at 1 liter/minute at the factory. The metering valve MV2 that
controls the rate of the bypass vent is located near the rear end of
the sampling system. See Figure 3-11. To access this valve, open the
top and back covers of the analyzer.
5. Sample/Span Vent
The sample/span vent transports the sample or span gas out of the
system after exposure to the Ultra Trace sensor.
Caution: The sample/span and sparger vents must be connected to vent
tubes of at least
1
/
4
in OD, preferably
1
/
2
in or larger. Using
smaller tubing may result in significant backpressure which
could force the vent gas to pass through the sensing electrode and
cause damage or even rupture the sensing electrode.
6. Air In
The compressed (instrument) air inlet is a
1
/
4
" tube fitting. Com-
pressed air is used to actuate the pneumatic valves, and is controlled
by the solenoid valves, which are in turn controlled by the micropro-
cessor. The inlet air pressure should be between 75 and 80 psig.
Pressure lower than 75 psig may not actuate the pneumatic valves,
leaving them closed. However, be careful not to exceed 80 psig.
CAUTION:
Pressure higher than 100 psig can damage the solenoid
valves.