Siemens Simatic S7-400 User Manual
Page 282
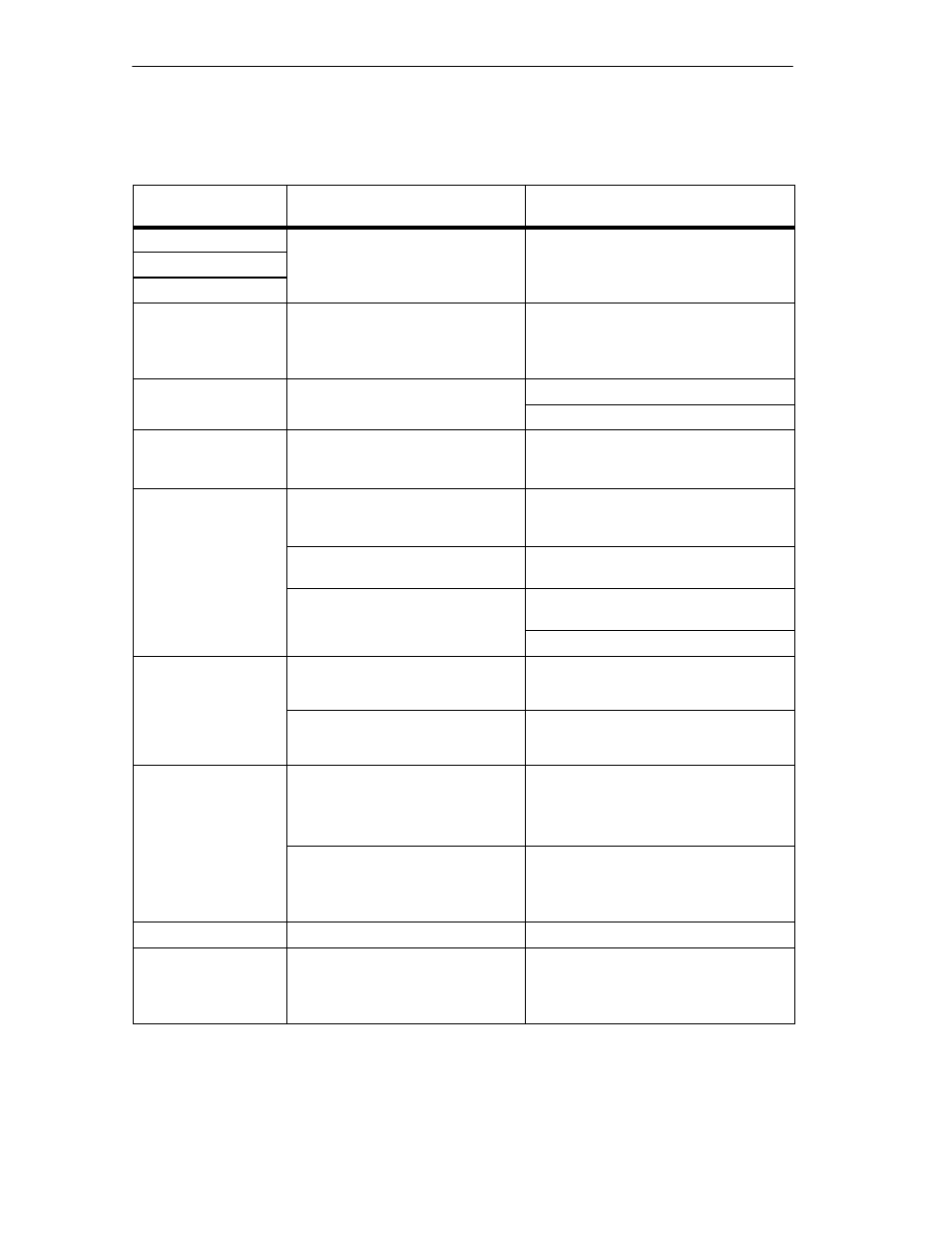
Analog Modules
5-66
S7-400, M7-400 Programmable Controllers Module Specifications
A5E00069467-07
Table 5-47 Diagnostics Messages of the Analog Input Modules, Causes of Errors and Remedial
Measures, continued
Diagnostics
Message
Remedy
Possible Error Cause
EPROM error
The module is defective
Replace module
RAM error
ADC/DAC error
Hardware interrupt lost
The module cannot send an
interrupt, since the previous
interrupt was not acknowledged;
configuration error possible
Change interrupt handling in the CPU
(change priority for interrupt OB; shorten
interrupt program)
Configuring/parameter
i
t
Illegal parameters transferred to
d l
Check measuring range module
assignment error
module
Reassign module parameter
Short circuit to M
A short circuit to the M potential has
occurred on the sensor supply of
two-wire transmitters
Eliminate short circuit
Wire break
Resistance too high in the sensor
connection
Use different type of sensor or
connection, e.g. use conductors with a
larger cross-sectional core area
Open circuit between module and
sensor
Close circuit
Channel not connected (open)
Disable channel (“Measuring Type”
parameter)
Connect channel
Reference channel
error
The reference junction connected at
channel 0 is faulty due to a wire
break, for example
Check terminals
The reference temperature value
transferred is not within the value
range
Reparameterize the reference
temperature
Underflow
Input value violates underrange,
error may be caused:
Wrong measuring range selected
Configure other measuring range
With the measuring ranges 4 to
20 mA and 1 to 5 V, if necessary by
polarity reversal of sensor
connection
Check terminals
Overflow
Input value overflows overrange
Configure other measuring range
Run time calibration
error
A wiring fault has occurred on a
channel during the calibration cycle
Eliminate the wiring fault (fault remains
until the next calibration; in other words,
a maximum 6 minutes or until there is a
STOP-RUN transition of the CPU)