Containment obstacles, Tool flange rotation extremes – Adept s650H Quattro User Manual
Page 77
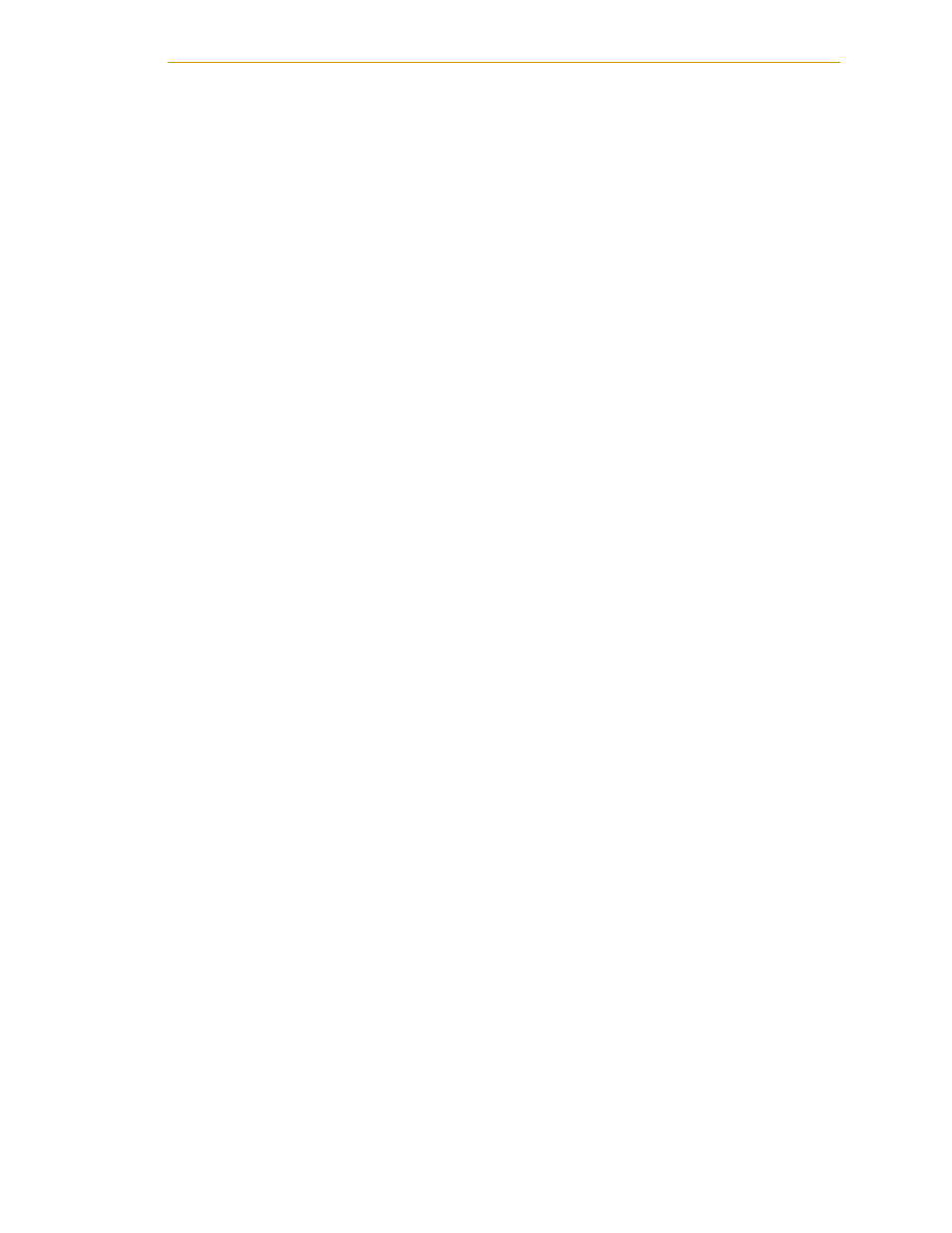
Quattro Motions
Adept Quattro s650 Robot User’s Guide, Rev B
77
Containment Obstacles
The work space of the robot is defined by an inclusion obstacle. This is done because,
unlike other robots, joint limits are not meaningful in defining the work space. The V+
version that supports the Quattro defines a cone-like shape as a containment obstacle.
This is actually the work envelope. See
“Work Envelope, Side View” on page 87
. Other
obstacles can be defined within this obstacle.
Tool Flange Rotation Extremes
This section addresses an ambiguity that can occur at extremes of the tool flange rotation.
Note the following exceptions:
• Quattro robots with tool flange rotation of less than 360° (e.g., 1:1 platform) are not
affected.
• Manual control is not affected.
• Program-controlled motions with destinations not near the extremes of tool flange
rotation, or that start and stop on the same side (either + or -) of the center angle of
rotation of the tool flange are not affected. That means that most of the range of
tool rotation is not affected.
Since there is no robot axis directly associated with the tool flange rotation, that rotation is
specified by the roll component of the destination transformation.
The V+ system considers the center angle of rotation of the tool flange to have a roll
component of 180°, and the roll component approaches 0° as the tool-rotation angle
approaches ±180°.
NOTE: The roll is -180 on one side of the center of rotation, and +180 on
the other side. See
An ambiguity, however, exists at a roll angle of 0°, since the tool-rotation angle can be
either +180° or -180° at that roll angle. Furthermore, due to the resolution of the tool flange
rotation, the ambiguity actually exists for roll values between about -0.1° and +0.1°. This is
considered to be the “ambiguity zone” for the tool rotation. (The “ambiguity zone”
increases if the total tool rotation is greater than 360° by the amount that the total tool
rotation exceeds 360°.)
In order to address this ambiguity, the following rule has been implemented in the
motion-planning software:
When a motion destination has a tool rotation within the “ambiguity zone” (i.e.,
tool rotation greater than +179.9°, or less [more negative] than -179.9°), the tool is
permitted to rotate only in the direction of the shortest distance from the starting
position to the destination position. But if that rotation would exceed the range of
motion in that direction, the error “*Location out of range*” is reported and the
motion is not performed.