Frame orientation, Frame construction, Robot-to-frame considerations – Adept s650H Quattro User Manual
Page 40
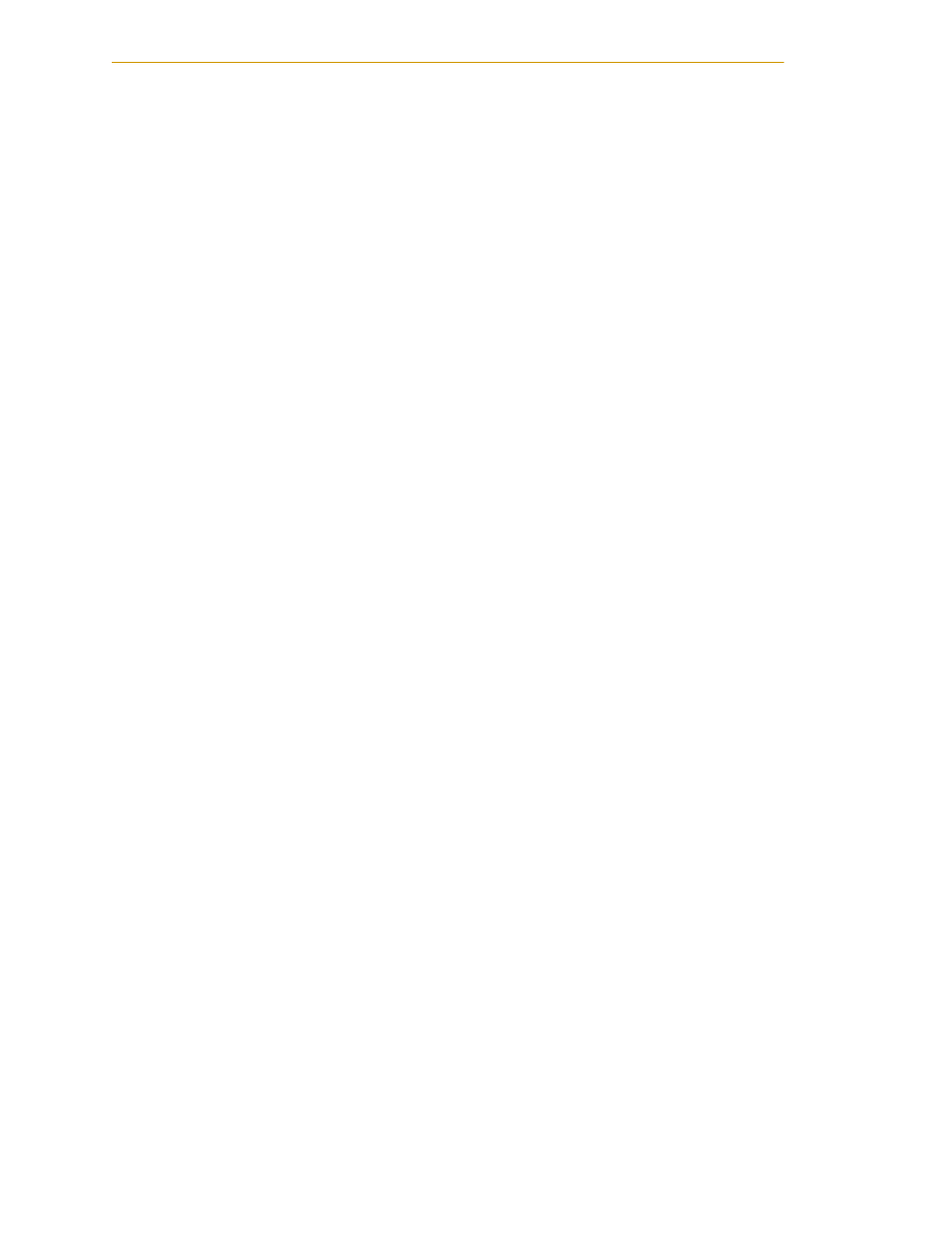
Chapter 3 - Robot Installation
40
Adept Quattro s650 Robot User’s Guide, Rev B
Frame Orientation
The sample robot frame design is stiffer in one direction than the other. This is to
accommodate belt conveyor applications where the robot is moving with much more
acceleration across a conveyor belt than along it. The conveyor should generally be
aligned so the belt travel is along the robot world Y axis, and the mid-height frame
members cross the belt at a 90° angle. The across-the-belt dimension of the frame should
be minimized to get the best performance of the robot in that direction. While this frame
design assumed a 1.8 m across-the-belt frame dimension, a 1.5 m dimension would offer
increased stiffness and possibly increased robot performance at high accelerations and
payloads. The mid-height horizontal members are important to the frame stiffness, and
should be located as close to the belt as possible.
For applications requiring high accelerations along the direction of belt travel,
consideration should be given to strengthening the frame in that direction.
Frame Construction
Typically, the frame is constructed of welded steel members. Hygiene-sensitive
applications may call for stainless steel fabrication, with care taken to seal up all possible
voids and grind smooth all weld joints. For other applications it may be suitable to
manufacture the frame of carbon steel and paint the resulting assembly. The frame design
presented here is based on a steel construction using 10 mm thick members.
Some
customers
may choose to use tubular members - or turn horizontal members at 45° angles
to allow
for water runoff from the flat frame surfaces.
Robot-to-Frame Considerations
The Quattro has a moderately-complex mounting requirement due to the nature of the
parallel-arm kinematics and the need to minimize the robot size and mass.
Figure 7-3 on
page 87
and
Figure 7-4 on page 88
show the inner arm travel and how it may encroach on
the robot mounting points. The design suggested here uses transition pieces to allow for
butt welds and mating interfaces where there will be no protruding surfaces to collect
contamination. This mounting design results in a natural frequency of about 90 Hz for just
the robot mounting members, but not the entire frame assembly. Alternate designs should
consider 90 Hz as a goal for this part of the frame. Note that this design allows for
lengthening the frame in the direction along the belt travel without significantly changing
the natural frequency.
The robot mounts in four locations, as detailed in the drawings. The holes are tapped for
an M20 or M16 bolt clearance, which provides flexibility in mounting and robot
installation. The Adept Quattro s650 robot may be mounted from the top or bottom of the
frame. A crane or forklift should be used to position the robot. If lifted from above, the
robot must be lifted by the provided eyebolts using slings or other user-supplied
fasteners.
Figure 7-1 on page 85
shows the mounting hole pattern for the Adept Quattro s650 robot.
Note the hole location and mounting pad tolerances for position and flatness (
Figure 7-7
on page 95
).