EVCO EPU2LXP1CH Installer manual User Manual
Page 80
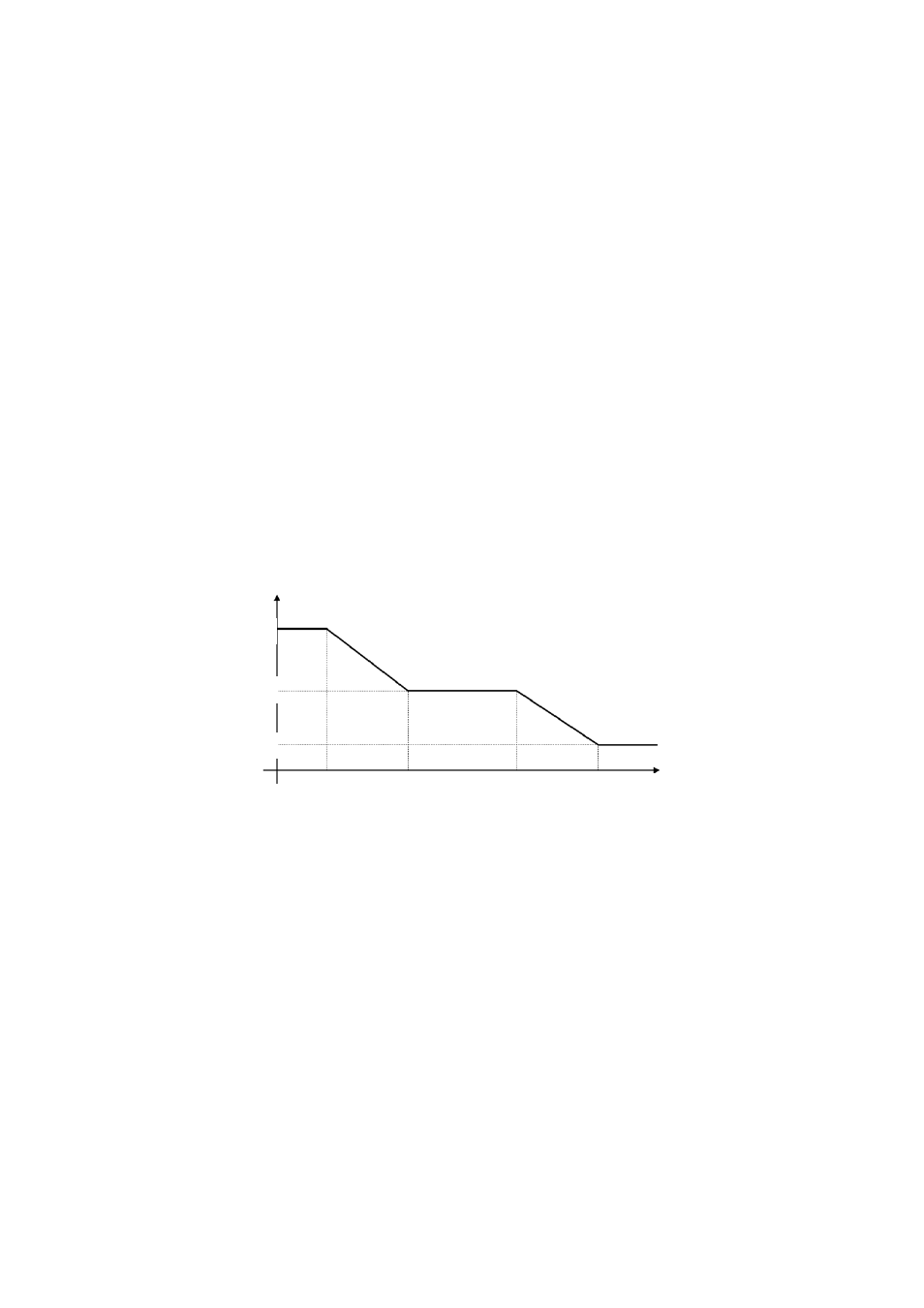
EVCO S.p.A.
c-pro 3 micro CHIL | Application manual ver. 1.0 | Codice 144CP3CHE104
page 80 of 120
8.20
Management of EVDRIVE03 integrated into the system
The management of the electronic valve must be optimised and not limited to a classical overheating control.
There are several conditions and regulations that must consider other system variables as a whole, as well as the overheating variables
(evaporation temperature and pressure) in a way to limit the problems due to the delays introduced by the temperature probe in the
same and its positioning. These functions must be enabled from parameter in a way that the manufacturer can exclude them.
8.20.1
Enabling of EEV operation
The controller knows when it is the time to activate the unit (switch a compressor on) and must consequently enable operation of the
EVDRIVE03 driver via CAN bus.
Operation enabling must precede compressor switch-on by a few seconds. The valve must be "prepared" in an open manner by a
suitable percentage for the compressor being switched on.
8.20.2
PID parameters set
EVDRIVE03 envisions 2 independent sets of parameter to use in the cooling (and defrosting) and heating operating modes. The
controller must be able to select the most appropriate parameters set on the basis of the operating mode. The set to use may simply be
selected from the 2 available or the parameters could be passed directly (PV parameters can be reached from the manufacturer menu).
8.20.3
Modulation of the SH set
•
If the DSH is lower than 10K, liquid may return to the compressor - to counter this phenomena it is useful to raise the SH set.
•
If the differential is higher than 20K there is no risk of liquid returning – considering the “favourable” condition in relation to
safety of the compressor the SH set can be reduced to increase system efficiency (reduction of the condensation pressure and
increase of the evaporation pressure).
These variations will have a minimum and a maximum and will be parameter sable as per figure.
In this way, the risk of liquid return to the compressor is limited and system efficiency is increased according to the machine work
conditions.
8.20.4
CAN Configuration
In order to correctly configure the valves of the two circuits, the CAN address and the baud-rate of each EVDRIVE03 need to be set.
The Circuit 1 valve must have the address CAN=11, while the Circuit 2 valvemust have the address CAN=12.
The baud-rate forCAN communicationmust be set according to parameter PH99.
Actual
Set SH
Max Set SH
Set SH
Min Set SH
Min DSH
DSH OK
Min (10K)
DSH OK
Min (20K)
Max DSH
DSH