EVCO EPD4DF3 User Manual
Evdrive03 - electronic expansion valves drivers
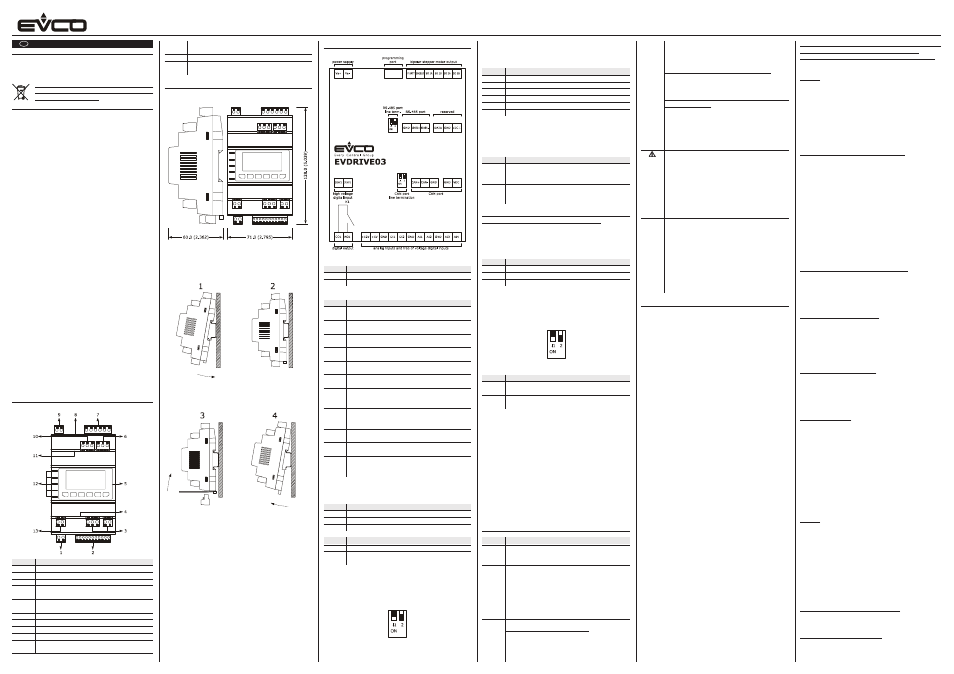
EVCO S.p.A. | Code 104EPDE113 | Page 1 of 2 | PT 34/12
EVDRIVE03 - Electronic expansion valves drivers
GB
ENGLISH
IMPORTANT
Read this document carefully before installing and using
the device and follow all the additional information; keep
this document close to the device for future consultations.
For further information consult the “Application manual”.
The device must be disposed according to the
local legislation about the collection for electrical
and electronic equipment.
1
INTRODUCTION
1.1
Introduction
The drivers of the EVDRIVE03 series are devices studied
for the management of bipolar stepper electronic expan-
sion valves.
They are available in built-in and blind version (according
to the model).
The user interface of the built-in versions consists of a LCD
graphic display, of six buttons and guarantees an index of
protection IP40.
The blind versions must be used with a remote user inter-
face.
They can be powered both in alternating and in direct cur-
rent (24 VAC/24... 37 VDC).
The drivers can work with the most common temperature
probes (NTC and Pt 1000) and with the most common pres-
sure transducers (0-20 mA, 4-20 mA, 0-5 V ratiometric
and 0-10 V).
They have configurable digital inputs (enable the opera-
tion, change parameters set, backup module status, etc.)
and a 5 res. A @ 250 VAC digital output (electromechani-
cal relay) configurable as alarm output, solenoid valve or
resynchronization valve.
Through the programming port it is possible to make the
upload and the download of the configuration parameters
(using the programming key EVKEY10); through this port
(or the RS-485 one, with MODBUS communication proto-
col), it is also possible to connect the devices to the set-up
software system Parameters Manager or to the plants moni-
toring and supervision one RICS (through a serial inter-
face).
Through the CAN communication port (or the RS-485 one)
it is finally possible to connect the devices to a controller
or to a remote user interface.
Through the backup module EPS4B it is finally possible to
close the valve in case of lack of power supply of the driv-
ers.
Installation is on DIN rail.
Among the several functions one highlights the possibility
to work both in stand alone mode and under the supervi-
sion of a controller, the management both of generic elec-
tronic expansion valves and of the most common valves
Sporlan and Alco and the management of the backup probes.
2
DESCRIPTION
2.1
Description
Term. Meaning
1
digital output
2
analog inputs and free of voltage digital inputs
3
CAN port (not available in model EPD4BX3)
4
CAN port line termination (not available in model
EPD4BX3)
5
display and keyboard (not available in models
EPD4BX3, EPD4BC3 and EPD4BF3)
6
reserved
7
bipolar stepper motor output
8
programming port
9
power supply
10
RS-485 port (not available in models EPD4BX3
and EPD4BC3)
11
RS-485 port line termination (not available in mod-
els EPD4BX3 and EPD4BC3)
12
signalling LEDs
13
high voltage digital input (not available in model
EPD4BX3)
3
SIZE AND INSTALLATION
3.1
Size
4 DIN modules; size in mm (in).
3.2
Installation
On DIN rail 35.0 x 7.5 mm (1.377 x 0.295 in) or
35.0 x 15.0 mm (1.377 x 0.590 in).
To install EVDRIVE03 operate as shown in the following draw-
ing.
To remove EVDRIVE03 remove possible extractable screw ter-
minal blocks plugged at the bottom first, then operate on the
DIN rail clips with a screwdriver as shown in the following
drawing.
To install EVDRIVE03 again press the DIN rail clips to the end
first.
3.3
Additional information for the installation
-
make sure the working conditions of the device (operat-
ing temperature, operating humidity, etc.) are in the limits
indicated; look at chapter “TECHNICAL DATA”
-
do not install the device close to heating sources (heat-
ers, hot air ducts, etc.), devices having big magnetos
(big speakers, etc.), locations subject to direct sunlight,
rain, humidity, dust, mechanical vibrations or bumps
-
according to the safety legislation, the protection against
possible contacts with the electrical parts must be en-
sured by a correct installation of the device; all the parts
which ensure the protection must be fixed so that you
can not remove them if not by using a tool.
4
ELECTRICAL CONNECTION
4.1
Electrical connection
Digital output
Electromechanical relay.
Term. Meaning
CO1
common digital output
NO1
normally open contact digital output
Analog inputs and free of voltage digital inputs
Term. Meaning
+12V power supply 0-20 mA/4-20 mA/0-10 V transducers
(12 VDC ±10%, 60 mA max.)
+5V
power supply 0-5 V ratiometric transducers (5 VDC
±5%, 40 mA max.)
GND
ground analog inputs and free of voltage digital in-
puts
DI1
digital input 1 (non optoisolated free of voltage con-
tact; 5 V when not loaded, 3.3 mA when loaded)
DI2
digital input 2 (non optoisolated free of voltage con-
tact; 5 V when not loaded, 3.3 mA when loaded)
GND
common analog inputs and free of voltage digital
inputs
AI1
analog input 1 (which can be set via configuration
parameter for NTC/Pt 1000 probes and for 0-20 mA/
4-20 mA/0-5 V ratiometric transducers)
AI2
analog input 2 (which can be set via configuration
parameter for NTC/Pt 1000 probes and for 0-20 mA/
4-20 mA/0-5 V ratiometric transducers)
GND
common analog inputs and free of voltage digital
inputs
AI3
analog input 3 (which can be set via configuration
parameter for NTC/Pt 1000 probes)
AI4
analog input 4 (which can be set via configuration
parameter for 0-20 mA/4-20 mA/0-5 V ratiometric/
0-10 V transducers)
CAN port (not available in model EPD4BX3)
Non optoisolated CAN port, with CANBUS communication pro-
tocol.
Term. Meaning
CAN+ signal +
CAN- signal -
GND
ground
Term. Meaning
GND
ground
VDC
power supply remote user interface (22... 35 VDC,
100 mA max.)
CAN port line termination (not available in model
EPD4BX3)
Position microswitch 1 on position on (120 Ω, 0.25 W) to plug
in the CAN port line termination (plug in the termination of
the first and of the last element of the network).
Reserved
Reserved.
Bipolar stepper motor output
Term. Meaning
V BATT backup power supply input
SHIELD common bipolar stepper motor shielded cable
SO 1A bipolar stepper motor coil 1
SO 1B bipolar stepper motor coil 1
SO 2A bipolar stepper motor coil 2
SO 2B bipolar stepper motor coil 2
Programming port
Non optoisolated programming port, with MODBUS communi-
cation protocol.
Power supply
Term. Meaning
V≅+ power supply device (not isolated; 24 VAC +10%
-15%, 50/60 Hz ±3 Hz, 40 VA max. or 24... 37 VDC,
22 W max.)
V≅-
power supply device (not isolated; 24 VAC +10%
-15%, 50/60 Hz ±3 Hz, 40 VA max. or 24... 37 VDC,
22 W max.)
If the device is powered in direct current, it is necessary to
respect the polarity of the power supply voltage.
RS-485 port (not available in models EPD4BX3 and
EPD4BC3)
Non optoisolated RS-485 port, with MODBUS communication
protocol.
Term. Meaning
GND
ground
RS485+ D1 = A = + (terminal 1 of the transceiver)
RS485- D0 = B = - (terminal 0 of the transceiver)
RS-485 port line termination (not available in models
EPD4BX3 and EPD4BC3)
Position microswitch 1 on position on (120 Ω, 0.25 W) to plug
in the RS-485 port line termination (plug in the termination
of the first and of the last element of the network).
High voltage digital input
Term. Meaning
DIHV1 high voltage digital input (optoisolated contact;
115 VAC -10%... 230 VAC +10%)
DIHV1 high voltage digital input (optoisolated contact;
115 VAC -10%... 230 VAC +10%)
4.2
Additional information for electrical connection
-
do not operate on the terminal blocks of the device using
electrical or pneumatic screwers
-
if the device has been moved from a cold location to a
warm one, the humidity could condense on the inside;
wait about an hour before supplying it
-
make sure the power supply voltage, the electrical fre-
quency and the electrical power of the device correspond
to those of the local power supply; look at chapter “TECH-
NICAL DATA”
-
disconnect the power supply of the device before servic-
ing it
-
do not use the device as safety device
-
for the repairs and for information about the device please
contact the EVCO sales network.
5
SIGNALINGS
5.1
Signalings
LED
Meaning
ON
LED power supply
if it is lit, the device will be powered
if it is out, the device will not be powered
STEP 1 LED stepper output 1
if it is lit, the valve will be stopped and completely
closed
if it flashes slowly, the valve will be stopped and
completely open
if it flashes quickly, the valve will be moving
if it is out, the valve will be stopped and open in an
intermediary position
STEP 2 LED auxiliary
if parameter Ph80 = 0, LED status
if it is lit, the device will be working in superheating
algorithm modality
if it flashes slowly, the device will be working in ana-
log positioner modality
if it flashes quickly, the device will be working in
manual or in debugger modality
if it is out, the device will be in a status different
from the ones related for parameter Ph80 = 0
if parameter Ph80 = 1, LED MOP/LOP alarm
if it flashes slowly, the LOP alarm will be running
if it flashes quickly, the MOP alarm will be running
if it is out, no MOP/LOP alarm will be running
if parameter Ph80 = 2, LED high superheating/low
superheating alarm
if it flashes slowly, the low superheating alarm will
be running
if it flashes quickly, the high superheating alarm will
be running
if it is out, no high superheating/low superheating
alarm will be running
LED alarm
if it is on, an alarm will be running
if it flashes slowly, it is necessary to disable/enable
the device to the operation in order that the modifi-
cation of the configuration parameters has effect
if it flashes quickly, it is necessary to switch off/on
the power supply of the device in order that the
modification of the configuration parameters has
effect
if it is out, no alarm will be running
COM LED communication
if it is lit, a communication alarm device-controller
will be running
if it flashes slowly, the communication device-con-
troller will not be completely correct
if it flashes quickly, a communication alarm device-
controller will be happened and the device (if fore-
seen) will be working in stand alone modality
if it is out, the device will be working in stand alone
modality or no communication alarm device-control-
ler will be running
6
TECHNICAL DATA
6.1
Technical data
Purpose of the device: electronic expansion valves driver.
Box: self-extinguishing grey.
Size: 71.0 x 128.0 x 60.0 mm (2.795 x 5.039 x 2.362 in;
W x H x D); 4 DIN modules.
Size refers to the device with the extractable screw terminal
blocks properly plugged.
Installation: on DIN rail 35.0 x 7.5 mm (1.377 x 0.295 in) or
35.0 x 15.0 mm (1.377 x 0.590 in).
Index of protection: IP20 (IP40 the front).
Connections: male extractable screw terminal blocks pitch
3.5 mm (0.137 in; analog inputs and free of voltage digital
inputs), male extractable screw terminal blocks pitch 5.0 mm
(0.196 in; power supply, high voltage digital inputs, outputs,
CAN port and RS-485 port) for conductors up to 2.5 mm²
(0.0038 in²) and 6 poles female RJ11 telephone connector
(programming port).
The maximum lengths allowed for the connecting cables are
the following:
-
power supply device: 30 m (98 ft)
-
analog inputs: 100 m (328 ft)
-
power supply 0-20 mA/4-20 mA/0-5 V ratiometric/
0-10 V transducers: 100 m (328 ft)
-
free of voltage digital inputs: 100 m (328 ft)
-
high voltage digital input: 100 m (328 ft)
-
digital output: 100 m (328 ft)
-
bipolar stepper motor output: 5 m (16 ft; 10 m (32 ft)
with shielded cable)
-
CAN port:
-
1,000 m (3,280 ft) with baud rate 20,000 baud
-
500 m (1,640 ft) with baud rate 50,000 baud
-
250 m (820 ft) with baud rate 125,000 baud
-
50 m (164 ft) with baud rate 500,000 baud
-
power supply remote user interface: 30 m (98 ft)
-
RS-485 port: 1,000 m (3,280 ft); also look at the MODBUS
specifications and implementation guides manual.
One suggests using the connecting kit CJAV17 (female ex-
tractable screw terminal blocks pitch 5.0 mm (0.196 in), to
order separately).
Operating temperature: from -10 to 60 °C (from 14 to
140 °F).
Storage temperature: from -20 to 70 °C (from -4 to
158 °F).
Operating humidity: from 10 to 90% of relative humidity
not condensing.
Pollution situation: 2.
Power supply:
-
24 VAC +10% -15%, 50/60 Hz ±3 Hz, 40 VA max. not
isolated
-
24... 37 VDC, 22 W max. not isolated
supplied by a class 2 circuit.
If the device is powered in direct current, it is necessary to
respect the polarity of the power supply voltage.
Protect the power supply with a fuse rated 2 A-T 250 V.
Overvoltage category: III.
Analog inputs:
4 inputs
-
2 inputs (which can be set via configuration param-
eter for NTC/Pt 1000 probes and for 0-20 mA/
4-20 mA/0-5 V ratiometric transducers) which can be
set via configuration parameter for suction tempera-
ture backup probe/suction pressure backup probe
-
1 input (which can be set via configuration parameter
for NTC/Pt 1000) as suction temperature probe
-
1 input (which can be set via configuration parameter
for 0-20 mA/4-20 mA/0-5 V ratiometric/0-10 V trans-
ducers) as suction pressure probe.
NTC analog inputs (10K Ω @ 25 °C, 77 °F)
Kind of sensor:
ß3435.
Working range:
from -40 to 110 °C (from -40
to 230 °F) for standard NTC
probes
from -50 to 150 °C (from -58
to 302 °F) for high tempera-
ture NTC probes
from -50 to 110 °C (from -58
to 230 °F) for fast NTC probes.
Accuracy:
±0.6% of the full scale for
standard and fast NTC probes
±0.5% of the full scale for high
temperature NTC probes.
Resolution:
0.1 °C (1 °F).
Conversion time:
100 ms.
Protection:
none.
Pt 1000 analog inputs (1K Ω @ 0 °C, 32 °F)
Working range:
from -100 to 400 °C (from
-148 to 752 °F).
Accuracy:
±0.5% of the full scale.
Resolution:
0.5 °C (1 °F).
Conversion time:
100 ms.
Protection:
none.
0-20 mA/4-20 mA analog inputs
Input resistance:
≤ to 200 Ω.
Accuracy:
±1% of the full scale.
Resolution:
0.01 mA.
Conversion time:
100 ms.
Protection:
none; the maximum current
allowed on each input is
25 mA.
0-5 V ratiometric analog inputs
Input resistance:
≥ to 10 KΩ.
Accuracy:
±1% of the full scale.
Resolution:
0.01 V.
Conversion time:
100 ms.
Protection:
against the reversal of polar-
ity.
0-10 V analog inputs
Input resistance:
≥ to 10 KΩ.
Accuracy:
±1% of the full scale.
Resolution:
0.01 V.
Conversion time:
100 ms.
Protection:
against the reversal of polar-
ity.
Power supply 0-20 mA/4-20 mA/0-10 V transducers:
12 VDC ±10%, 60 mA max.
Power supply 0-5 V ratiometric transducers: 5 VDC ±5%,
40 mA max.
The device incorporate a restorable thermal protection of
the power supplies against the short circuit and the over-
load.
Digital inputs:
3 inputs
-
2 inputs (non optoisolated free of voltage contacts,
which can be set via configuration parameter as nor-
mally open/normally closed contact) which can be set
via configuration parameter as enable the operation/
change parameters set/resynchronization command/
backup module status
-
1 input (optoisolated high voltage contact, which can
be set via configuration parameter as normally open/
normally closed contact) which can be set via configu-
ration parameter as enable the operation/change pa-
rameters set/resynchronization command/backup
module status (not available in model EPD4BX3).
Non optoisolated free of voltage contacts
Power supply:
none (5 V when not loaded,
3.3 mA when loaded).
Protection:
none.
Optoisolated high voltage contact
Power supply:
115 VAC -10%... 230 VAC
+10%.
Protection:
none.