Rockwell Automation CHPS-250 Linear Stage Installation User Manual
Page 95
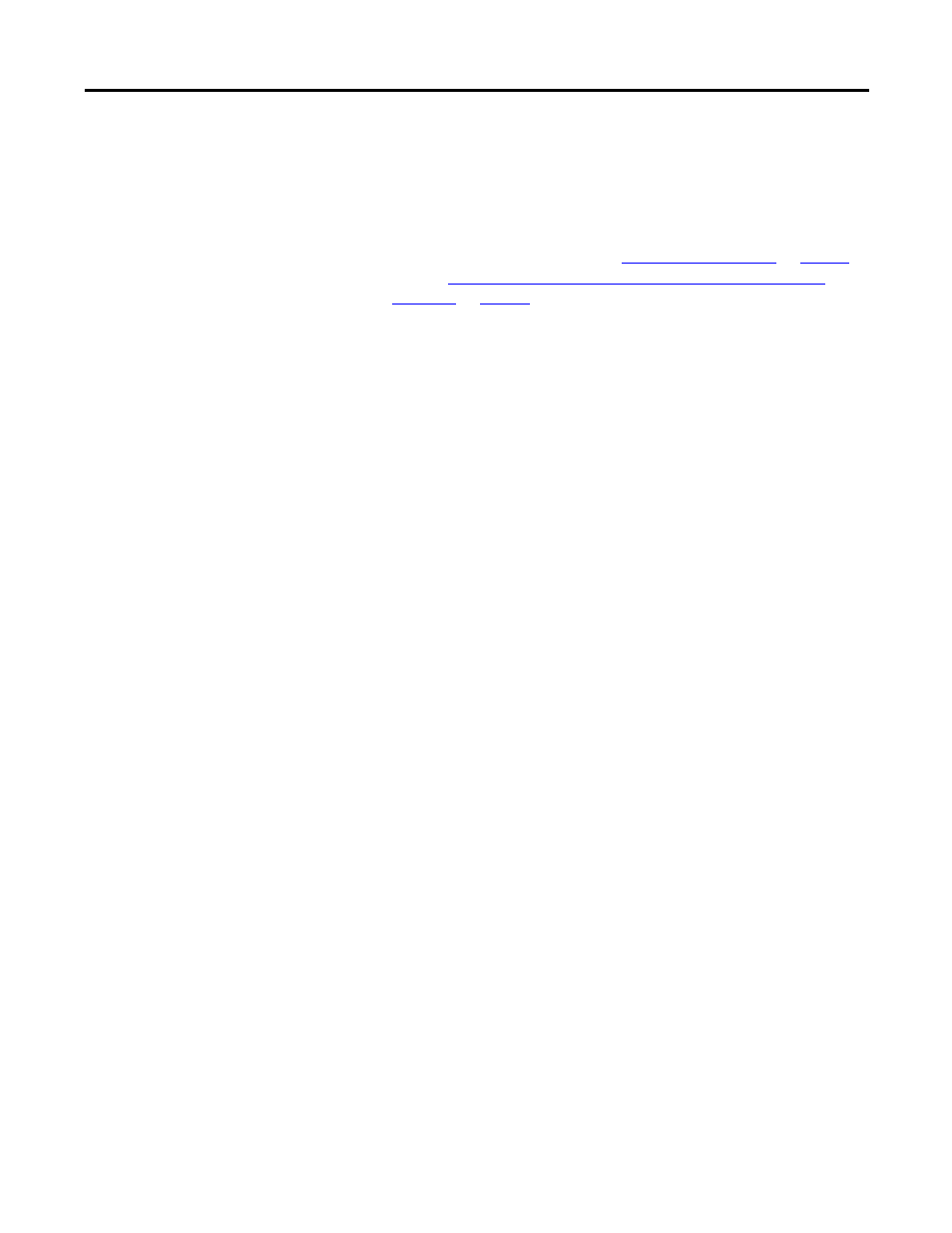
Rockwell Automation Publication CHPS-UM001D-EN-P - July 2014
95
Start-up Guide for CHPS-Series Stage with Ultra3000 Drive and Ultraware Software Appendix D
6. Current Limit parameters - the positive and negative current limit, must
not exceed the CHPS-Series stage motor’s intermittent current rating. Set
per the application requirements.
7. Verify correct encoder polarity and test distance count. Encoder must
count in positive direction when CHPS-Series stage is moving in the
positive stage direction as shown in
.
Also see
CHPS-Series Stage and Ultra3000 Drive Troubleshooting
. Incorrect encoder sequencing can cause a runaway
motor condition or incorrect commutation.
8. Perform Commutation Diagnostics only if enough free +/- travel distance
is available. You can guarantee optimal commutation only by doing
oscilloscope verification.
You can use the following checks for non-optimal commutation
verification. These tests cannot detect bad spots and other anomalies.
• Use Current Control Panel mode to give a small positive current
command. Verify the stage moves in the positive direction.
• Check for consistent force resistance over whole travel by pushing the
slide to multiple locations.
• Check that the amount of current to move the load and overcome
friction forces at a low steady speed are correct.
• The motor’s force constant (Kf ) can also be verified with a force gauge.
The Ultraware software command units for current scaling are in
A
0-peak
/V.
9. When current mode tests successfully, perform auto velocity or manual
velocity tuning with the Ultraware oscilloscope function, do this even if
you are using current mode to control your application. This further
evaluates commutation and check for a good step response.