Recommended start-up sequence – Rockwell Automation CHPS-250 Linear Stage Installation User Manual
Page 94
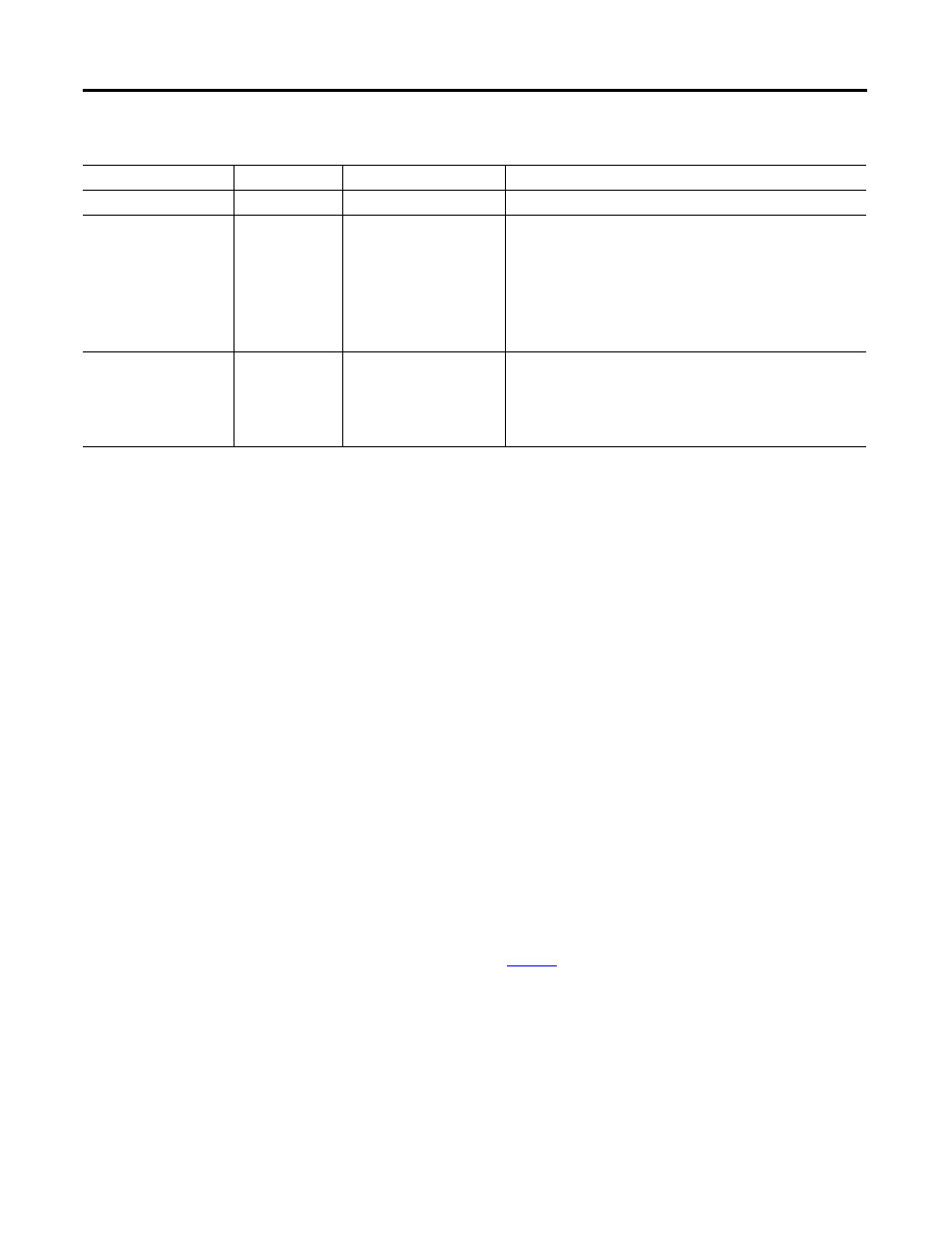
94
Rockwell Automation Publication CHPS-UM001D-EN-P - July 2014
Appendix D Start-up Guide for CHPS-Series Stage with Ultra3000 Drive and Ultraware Software
Recommended Start-up
Sequence
Follow these steps for optimal motor commutation, performance, overcurrent,
and overtemperature protection.
1. Set General Axis Parameters (.udb file extension)
a. Auto Motor Iden = disabled for linear motors.
b. Motor Model: select as needed.
c. Total Moving Mass in kg = coil mass or magnet mass + moving
structure mass+ moving cable assembly mass + customer load.
d. Current Limits in Amperes peak - set as needed for the application. The
drive uses the lowest value between the drive rating and the motor
rating.
e. Display Precision - Set to 2 decimal places.
f. User Current Fault in Amperes peak - this is the continuous current. Set
as needed for the application. The drive uses the lowest value between
drive rating and the motor rating. To avoid nuisance tripping of the fast-
acting protection, it can need to be set slightly higher.
2. Follow instructions from the standard drive manual and other applicable
documentation. Pay special attention to electrical noise control by using
cable shielding, shield termination, grounding, and bonding.
3. Wiring must match the CHPS-Series stage and Ultra drive connectivity
. Incorrect wiring or Hall offset combinations
can result in motor motion that has excessive force ripple and increased
current, temperature, or reduced force per unit of current.
4. Verify that the correct motor file is selected or correct custom motor
parameter values are entered.
5. User Current Fault parameter - this value must not exceed the CHPS-
Series stage motor’s continuous current rating.
Software Protection
—
—
—
Thermal Protection
Rth(w-a)
º
C /W
Calculate
The thermal resistance with the winding at ambient temperature:
For LC motors, enter the rated thermal resistance value, multiply by 1.1 for covered
and sealed stages.
For 150 frame stage that use only LZ motor, enter the rated thermal resistance
value.
For 200 and 250 frame stages:
LZ motors, enter 1.1x the rated thermal resistance value.
In addition for all stages with LZ motors, multiply this value again by 1.1 for a
covered and sealed stage.
Thermal Protection
Cth(w-a)
W/s/
º
C
Calculate
Energy absorption: Cth = tm/Rth where tm is the motor's thermal time constant
in seconds. Leave the value as found if a valid LC or LZ file is used.
If necessary, use the following tm values based on the heat sink size and cooling
method:
LC motors: tm = 1800 (seconds)
LZ motors: tm = 1200 (seconds)
Table 14 - Linear Motor Parameter File (.mdb extension)
Parameter
Units
Enter
Comment