Self-sensing commutation and startup – Rockwell Automation CHPS-250 Linear Stage Installation User Manual
Page 100
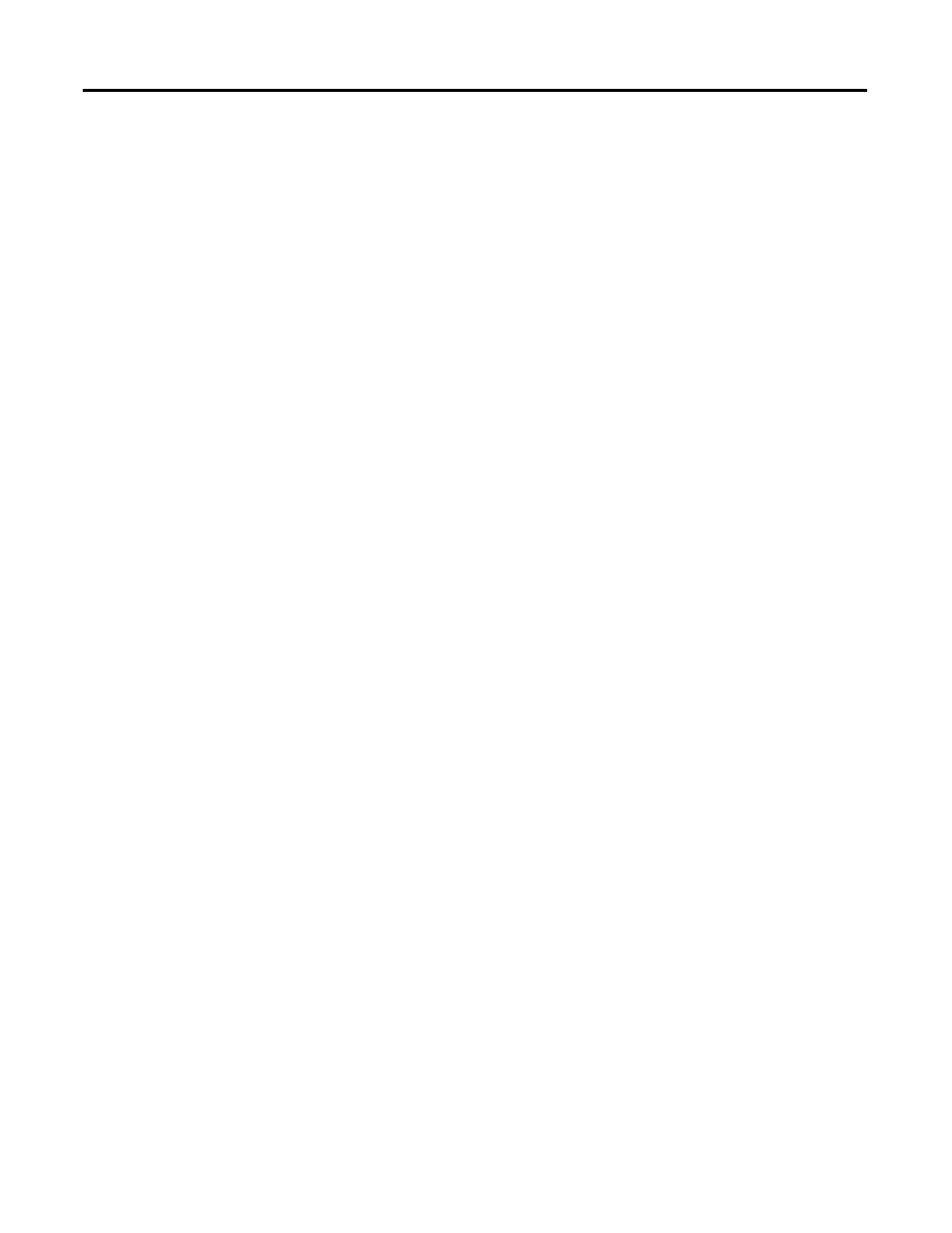
100
Rockwell Automation Publication CHPS-UM001D-EN-P - July 2014
Appendix D Start-up Guide for CHPS-Series Stage with Ultra3000 Drive and Ultraware Software
Self-sensing Commutation and Startup
This type of commutation does not use the Hall effect sensor. Motors with a Hall
effect sensor connection can be set to self-sensing commutation, the Hall effect
signals are ignored. Self-sensing start-up is not commutation diagnostics. You can
perform commutation diagnostics at any time on Hall effect or self-sensing
motors. Self-sensing start-up refers to the motor motion initialization that is
executed automatically after every power-up and enabling of the system. It
synchronizes the arbitrary encoder position or count to the drive’s initial
commutation angle.
This is the self-sensing start-up sequence:
• Enable is activated.
• Motor locks into detent or zero force position > up to ± one magnet pitch
(½ electrical cycle) of motion jerk.
• After jerk motion settles out in 1 or 2 seconds, motor executes a slow speed
test move of approximately two magnet pitches or one electrical cycle in
the positive direction.
• Drive disables, ready for normal operation.
During this startup, the drive evaluates the test motion. A fault indicates that the
motor motion was not as expected. Possible reasons include the following:
• Mechanical problem with the stage such as excessive stiction, friction, or
cable drag.
• Obstruction during test motion.
• Incorrect coil or encoder wiring.
• Encoder or signal problems, device fault, wiring problem, noise.
• During startup, the drive uses a fixed 1/6 of the peak motor or drive
current, whichever is lower.
Ultraware software version 1.3 with firmware revision 1.16 (or greater) has
improved functionality with proper alignment under any single obstruction:
• If during the positive test move, after detent, an obstruction is
encountered, a test move is done in the opposite direction after re-
initializing the new detent.
• If an obstruction prevents the motor from going to the real detent, for
example, detent past negative hard stop, the Ultra drive senses a false detent
during the test move due to false alignment. After re-initializing of the new
detent a second test move is done in the positive direction.
• The self-sensing routine can take 2x longer because of obstructions.
• If a second obstruction is detected during whole routine, such as low test
current or too high friction, the test faults.
• The new versions lets a user programmable test current value.
• Limit signals sent to the Ultra Drive are ignored during self-sensing start-
up.