Build your own cables, Route power and signal wiring, Determine the input power configuration – Rockwell Automation 2097-Vxxx Kinetix 300 EtherNet/IP Indexing Servo Drive User Manual User Manual
Page 58
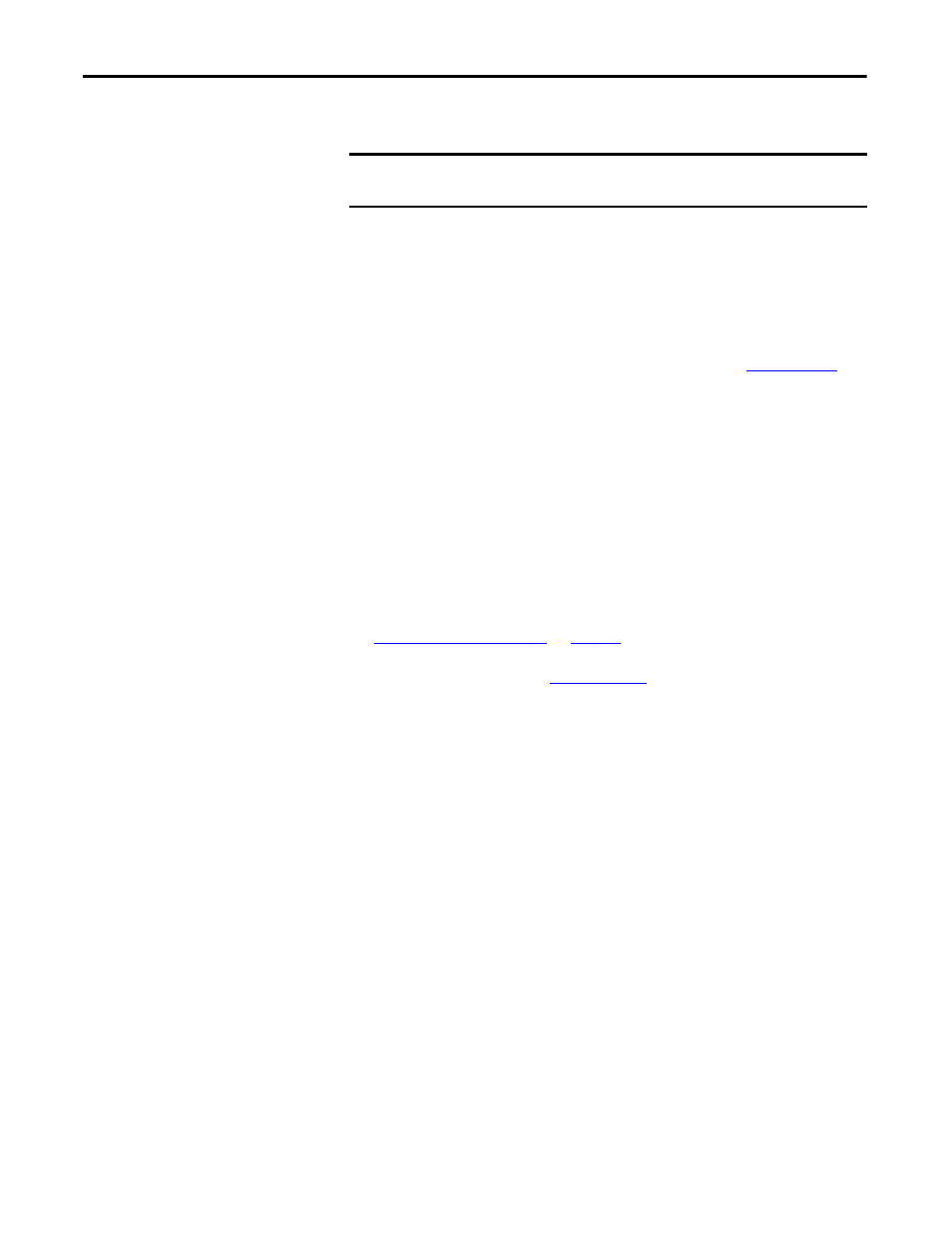
58
Rockwell Automation Publication 2097-UM001D-EN-P - November 2012
Chapter 4
Connecting the Kinetix 300 Drive System
Build Your Own Cables
• Connect the cable shield to the connector shells on both ends of the cable
with a complete 360° connection.
• Use twisted pair cable whenever possible. Twist differential signals with
each other and twist single-ended signals with the appropriate ground
return.
See the Kinetix Motion Control Selection Guide, publication
, for
low-profile connector kit, drive-end (mating) connector kit, and motor-end
connector kit catalog numbers.
Route Power and Signal Wiring
Be aware that when you route power and signal wiring on a machine or system,
radiated noise from nearby relays, transformers, and other electronic drives can be
induced into motor or encoder feedback signals, input/output communication,
or other sensitive low voltage signals. This can cause system faults and
communication anomalies.
See
for examples of routing high and low
voltage cables in wireways. See the System Design for Control of Electrical Noise
Reference Manual, publicatio
Determine the Input Power
Configuration
This section contains examples of typical single-phase and three-phase facility
input power wired to single-phase and three-phase Kinetix 300 drives.
The grounded power configuration lets you ground your single-phase or three-
phase power at a neutral point. Match your secondary to one of the examples and
be certain to include the grounded neutral connection.
IMPORTANT
Factory-made cables are designed to minimize EMI and are recommended over
hand-built cables to optimize system performance.