Description of operation, Functional proof tests, Description of operation functional proof tests – Rockwell Automation 2097-Vxxx Kinetix 300 EtherNet/IP Indexing Servo Drive User Manual User Manual
Page 161
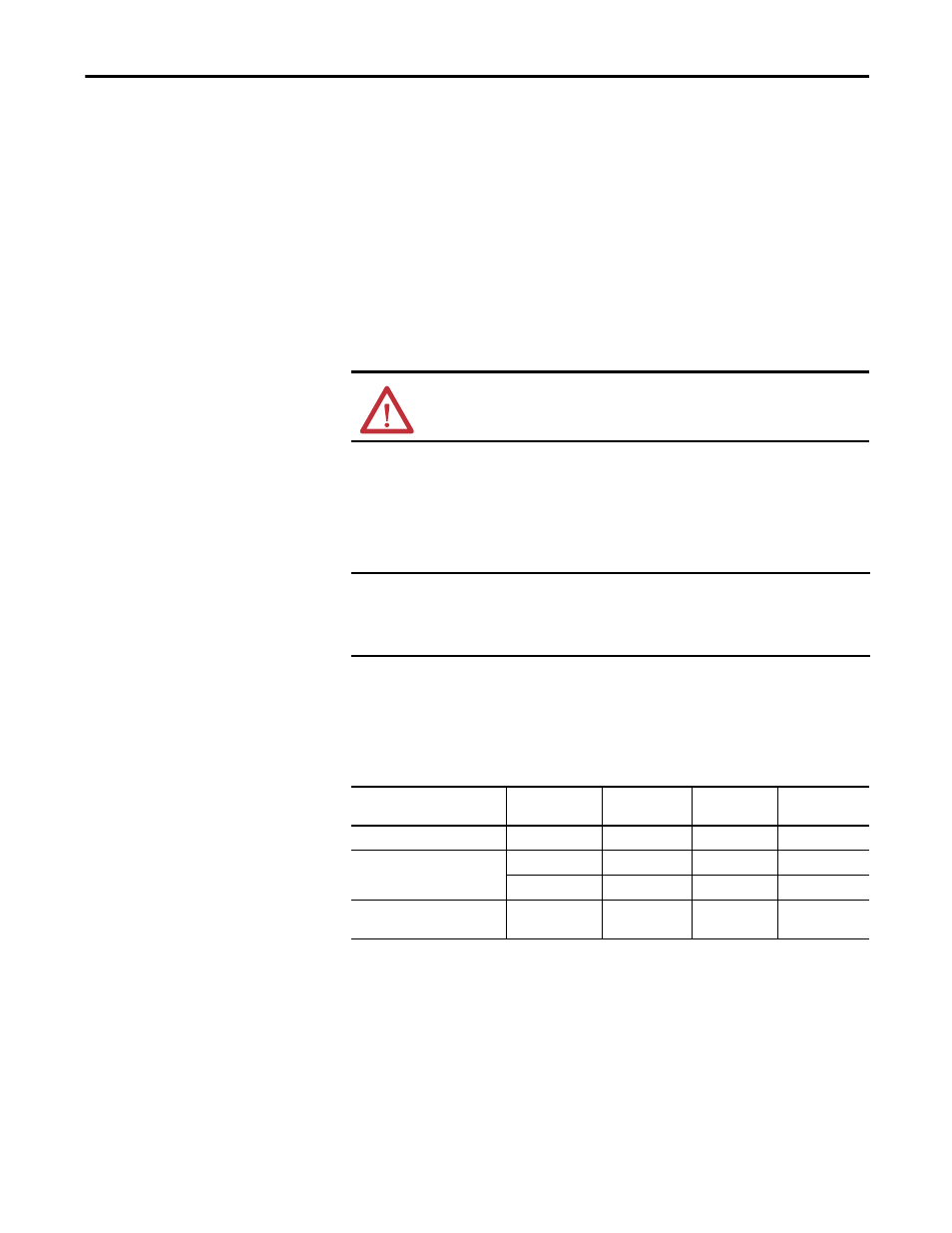
Rockwell Automation Publication 2097-UM001D-EN-P - November 2012
161
Kinetix 300 Drive Safe Torque-off Feature
Chapter 8
Description of Operation
The safe torque-off feature provides a method, with sufficiently low probability
of failure on demand, to force the power-transistor control signals to a disabled
state. When disabled, or any time power is removed from the safety enable inputs,
all of the drives output-power transistors are released from the ON state,
effectively removing motive power generated by the drive. This results in a
condition where the motor is in a coasting condition (stop category 0). Disabling
the power transistor output does not provide mechanical isolation of the
electrical output, which may be required for some applications.
Under normal drive operation, the safe torque-off switches are energized. If either
of the safety enable inputs are de-energized, the gate control circuit is disabled. To
meet ISO 13849-1 (PLd) both safety channels must be used and monitored.
Functional Proof Tests
The functional safety standards require that functional proof tests be performed
on the equipment used in the system. Proof tests are performed at user-defined
intervals, not to exceed one year, and are dependent upon PFD and PFH values.
To proof test the safe torque-off function, you must interrupt power to the inputs
of the safe torque-off function at pins STO-4 and STO-6 and verify that the
drive is in the disabled state.
Proof Test Truth Table
Normal operation of the safe torque-off function, if monitored and verified,
constitutes the proof test. A safe torque-off mismatch results in error code E39.
ATTENTION: Permanent magnet motors may, in the event of two simultaneous
faults in the IGBT circuit, result in a rotation of up to 180 electrical degrees.
IMPORTANT
Users specific applications determine the time frame for the proof test interval,
but it must not exceed one year due to the use of switches internal to the drive,
as required by ISO 13849-1.
Safety Function State
Safety Input 1
(STO-4)
Safety Input 2
(STO-6)
Safety Status
Output (STO-3)
Drive Status
Indication
(1)
(1) Drive display changes to condition shown on enable of the drive (IN_ A3 Enable).
Normal operation
Energized
Energized
Energized
Run
Safe torque-off mismatch
Energized
De-energized
Energized
E39
De-energized
Energized
Energized
E39
Safe torque-off function
engaged
De-energized
De-energized
De-energized
E39