Rockwell Automation 2097-Vxxx Kinetix 300 EtherNet/IP Indexing Servo Drive User Manual User Manual
Page 155
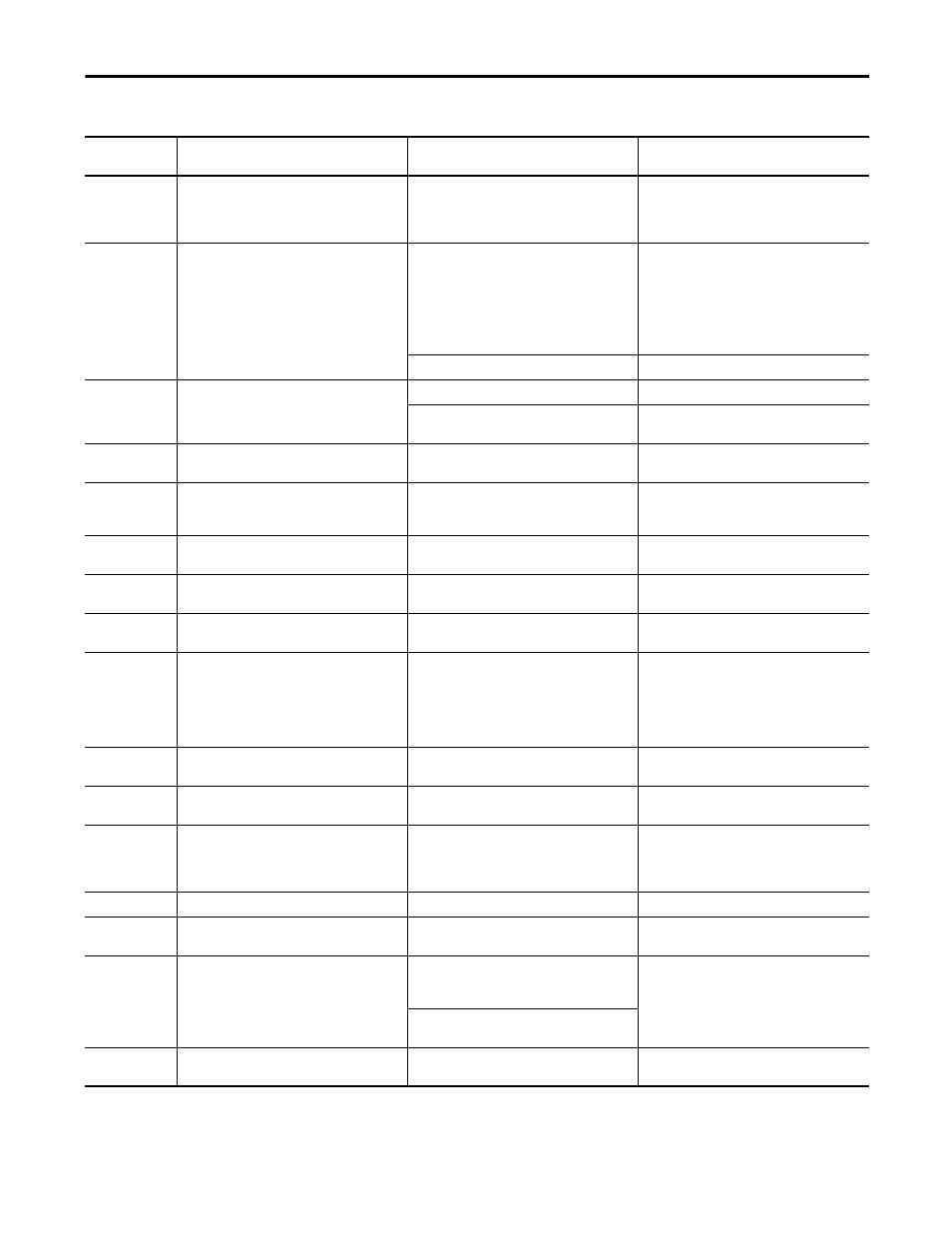
Rockwell Automation Publication 2097-UM001D-EN-P - November 2012
155
Troubleshooting the Kinetix 300 Drive System
Chapter 7
E09
Bus undervoltage.
Low AC line/AC power input.
• Verify voltage level of the incoming AC power.
• Check AC power source for glitches or line drop.
• Install an uninterruptible power supply (UPS)
on your AC input.
E10
Bus overvoltage.
Excessive regeneration of power.
When the motor is driven by an external
mechanical power source, it may regenerate too
much peak energy through the Kinetix 300 drives
power supply. The system faults to save itself from
an overload.
• Change the deceleration or motion profile.
• Use a larger system (motor and Kinetix 300
drive).
• Use a resistive shunt.
• If a shunt is connected, verify the wiring is
correct.
Excessive AC input voltage.
Verify input is within specifications.
E11
Illegal Hall state.
Incorrect phasing.
Check the Hall phasing.
Bad connections.
• Verify the Hall wiring.
• Verify 5V power supply to the encoder.
E12
Home search failed.
Home sensor and/or marker is outside the
overtravel limits.
• Check wiring.
• Reposition the overtravel limits or sensor.
E14
Ethernet I/O connection lost.
Ethernet I/O Connection lost.
Check wiring and Ethernet cables and routing.
Check controller program to be sure that I/O is
scanned at correct RPI rate.
E16
Software overtravel.
Programmed overtravel limit has been exceeded.
• Verify motion profile.
• Verify overtravel settings are appropriate.
E18
Overspeed fault.
Motor speed has exceeded 125% of maximum
rated speed.
• Check cables for noise.
• Check tuning.
E19
Excess position error.
Position error limit was exceeded.
• Increase following error limit or time.
• Check position loop tuning.
E23
Drive Thermal Protection
The internal filter algorithm protecting the drive
from overheating has tripped.
• Reduce acceleration rates.
• Reduce duty cycle (ON/OFF) of commanded
motion.
• Increase time permitted for motion.
• Use larger Kinetix 300 drive and motor.
• Check tuning.
E26
Index parameter out of range.
Parameters specified in the index table are beyond
system capabilities.
Verify index parameters, such as position and
velocity.
E27
Absolute move fault
Initiated move without being homed.
When using an absolute encoder home the axis
before attempting an absolute move.
E30
Encoder communication fault.
Communication was not established with an
intelligent encoder.
• Verify motor selection.
• Verify the motor supports automatic
identification.
• Verify motor encoder wiring.
E31
Encoder data.
Encoder data is corrupted.
Replace the motor/encoder.
E39
Safe torque-off while enabled.
The safety circuit was opened while drive was
enabled or while attempting to enable.
Check safety circuit.
E43
Drive enable input.
An attempt was made to enable the axis through
software while the Drive Enable hardware input
was inactive.
Verify that Drive Enable hardware input is active
whenever the drive is enabled through software.
The Drive Enable input transitioned from active to
inactive while the axis was enabled.
E44
Controller changed to PROG mode.
Program downloaded or turned key on logix
controller to program position.
Place controller back in RUN mode, clear faults.
Table 66 - Error Codes (continued)
Error
Code
Anomaly
Possible Cause
Action/Solution