Rockwell Automation 1771-QDC, D17716.5.87(Passport) CLAMP AND EJECT MODE User Manual
Page 188
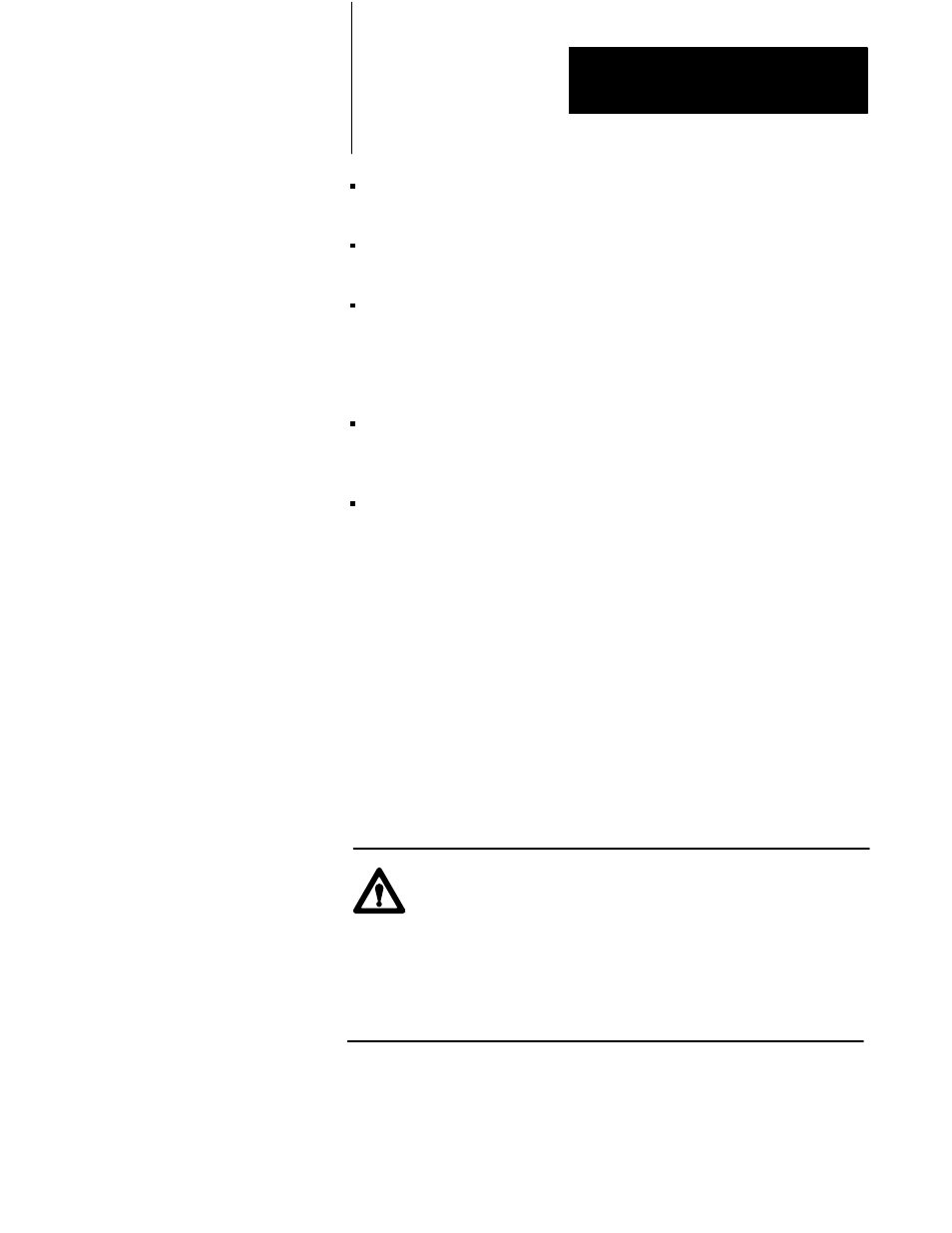
Tune Your Machine
Chapter 10
10-15
Decreasing available ejector circuit volume after your clamp is fully
open
Adjusting flow through a variable pump after clamp operations are
complete
Configuring your ejector hydraulic circuit to a “rest” or “pre-load” state
prior to switching directional valves through the PLC processor and
continuing the Ejector Profile
When configuring End-of Profile (Stroke) Set-output Values, remember:
The QDC module ignores End-of Profile (Stroke) Set-output Values on
all profiles (strokes) that are “bridged” to the next logical profile
(stroke)
After the QDC module outputs End-of Profile (Stroke) Set-output
Values, these outputs remain in effect until the QDC module is
commanded to initiate another movement, or until the “stop” command
is asserted
Acceleration and Deceleration Ramp Rates
The default (zero) ramp rate values entered in chapter 7 disabled the QDC
module’s ramping capabilities. This had the effect of forcing your QDC
module to “step” from setpoint to setpoint during each profile (stroke).
If required by your application, you may configure your QDC module to
ramp its outputs during any profile (stroke). The QDC module uses
configured acceleration and deceleration ramp rates when moving all of its
outputs from setpoint to setpoint during (not prior to) execution of any
profile (stroke).
ATTENTION: The QDC ramp rates are not affected until the
QDC module is actually executing the profile with configured
ramp rates. Ramp rates entered into LPC have no effect until
the clamp actually enters the Mold Protection Zone. The
QDC ramp rates are time based and use of excessively slow
(small setpoint) ramp rates inhibit effective closed-loop control,
reduce ERC calculation accuracy, and limit QDC control
capability. Use ramps only if machine operation mandates.