Rockwell Automation 1771-QDC, D17716.5.87(Passport) CLAMP AND EJECT MODE User Manual
Page 155
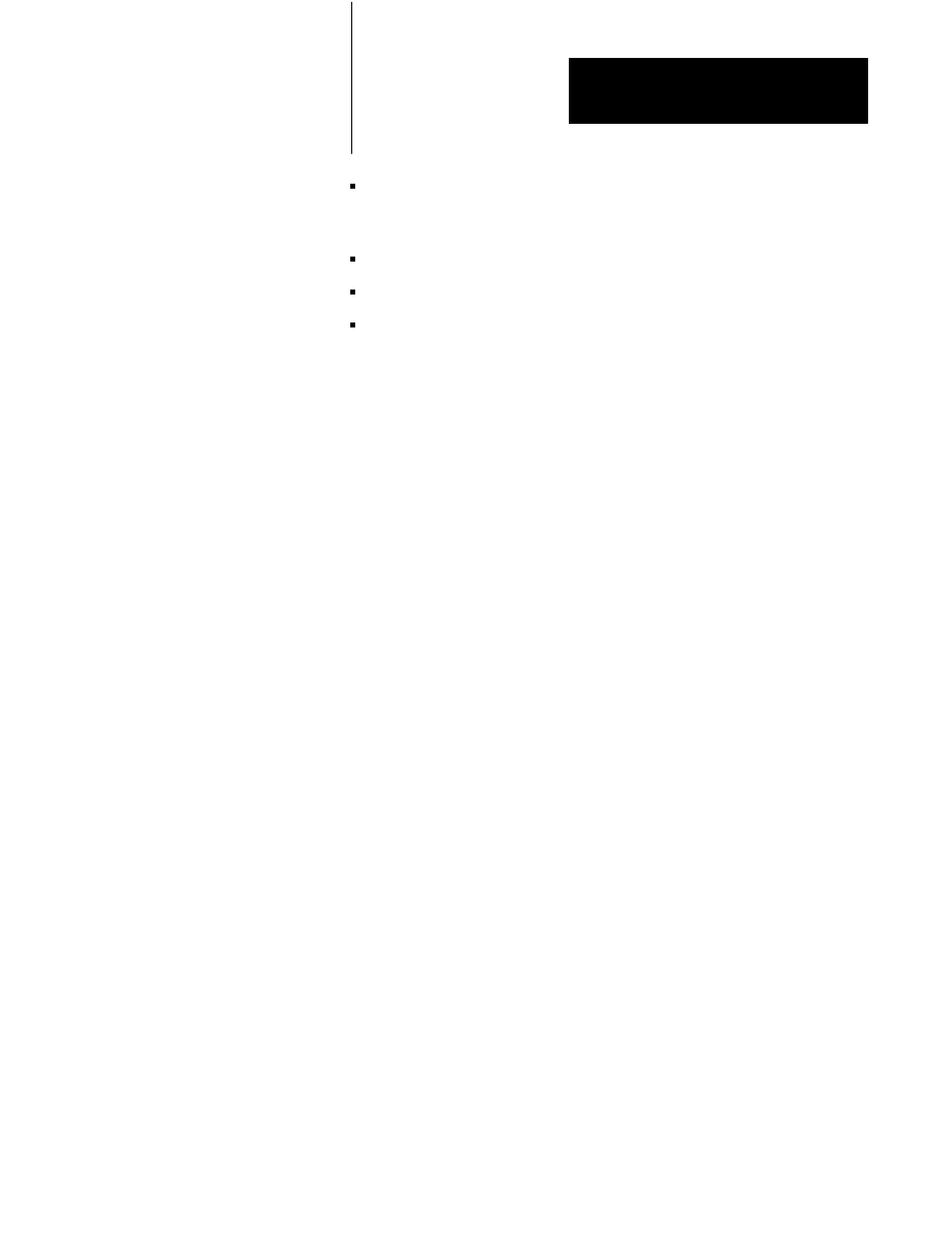
Span Your Clamp and Ejector Valves
Chapter 9
9-19
Identify all end-of segment position setpoints (OPC11, OPC14, OPC17,
OPC20, OPC23, OPC26, OPC29, OPC32, OPC35, OPC38). These
should remain unchanged from the initial settings
Identify Mold Full Open Position Setpoint (OPC62)
Identify Start OSC Position Setpoint (OPC61)
Select Start OSC on Zone Overrun (OPC03-B11 = 0)
If current settings do not match our recommended values from previous
chapters, we suggest you correct these values now using the download
procedure discussed in chapter 4.
Span Your Clamp Open Pressure Valve(s)
Span your Clamp Open Pressure vs. Position Profiles for smooth operation
at the highest desired clamp pressure. Do this by finding the optimum
values for FOC41-44, SOC41-44, TOC41-44, and OSC41-44 using the
values given above and the procedure below.
Optimal pressure reference values are determined using set-output.
1.
Jog your clamp to the full open position (mold halves mated).
2.
Align all other machine hydraulics to simulate Clamp Open. For
example, if certain pumps are enabled during Clamp Open
operations, enable them at this time. If a certain valve alignment
exists during Clamp Open, line the valves up accordingly at this time.
Important: If valve alignment or pressure availability is different for
Clamp Open and the Open Slow portion of clamp open, the following
procedure should be repeated twice: once for high speed Clamp Open, and
once for Open Slow. (FOC, SOC, and TOC values are filled in for high
speed Clamp Open; and OSC values are filled in during OSC
configuration.)
3.
Enter a value that should produce minimum pressure into the
set-output word (DYC09, DYC10, DYC11, or DYC12)
corresponding to the selected valve for Clamp Open pressure control.
Enter all other unselected valve set-output values to what you would
normally use during Clamp Open (reference FOC09-12, SOC09-12,
TOC09-12, OSC09-12).