Rockwell Automation 1771-QDC, D17716.5.87(Passport) CLAMP AND EJECT MODE User Manual
Page 148
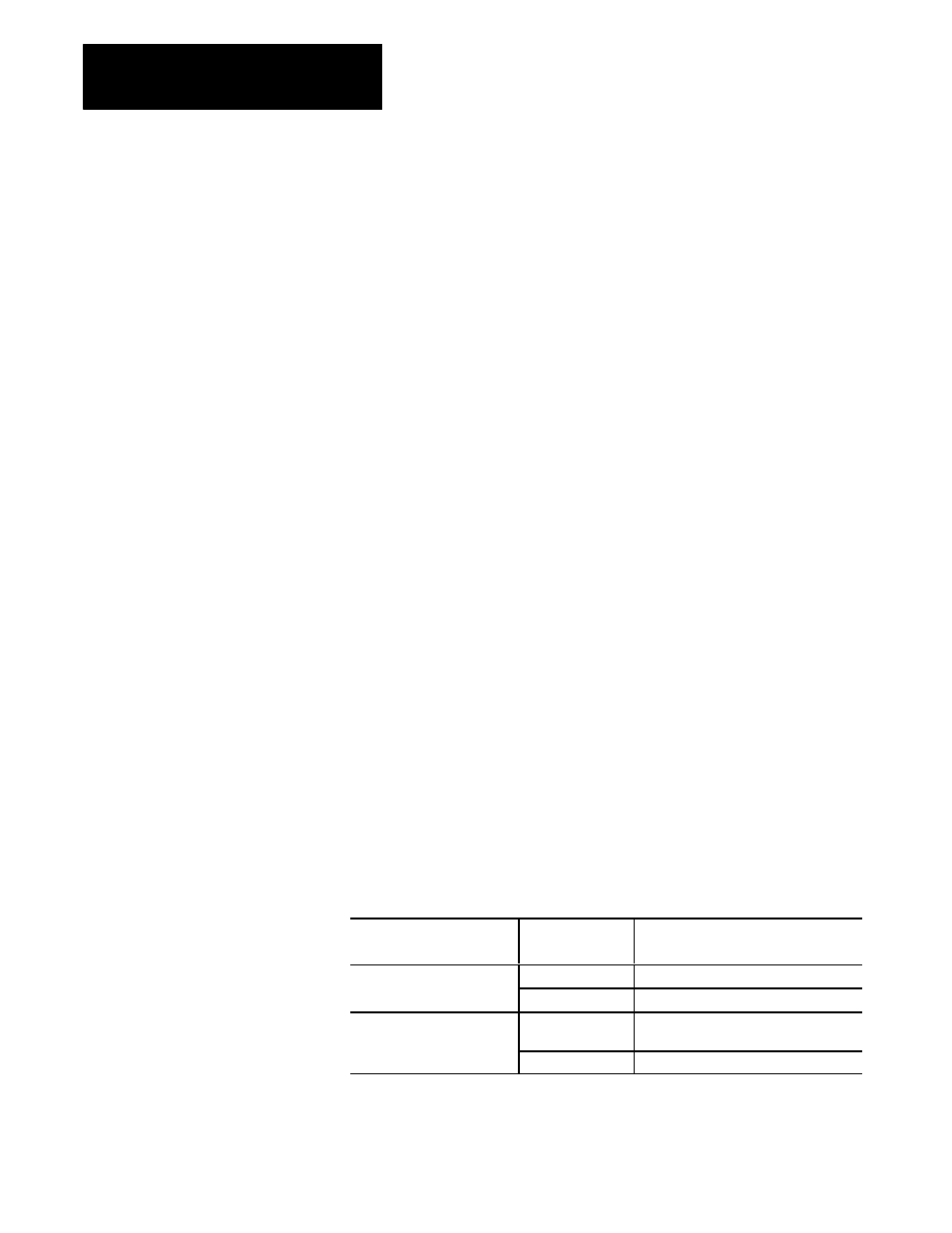
Span Your Clamp and Ejector Valves
Chapter 9
9-12
Test Your Clamp Close Pressure Valve(s) for Linearity
1.
Select pressure setpoints for Clamp Close that are typical of the
pressures you would run during normal machine operation. Enter
these setpoints into CPC10, CPC13, and CPC16 (Pro-Set 600
addresses N43:246, N43:249, and N43:252).
2.
Download changes to the QDC module (refer to chapter 4 for detailed
instructions).
3.
Jog your clamp to the full open position.
4.
Enable First Clamp Close (DYC02-B00, Pro-Set 600 address
B35/400). The clamp should move from its start position through the
First Clamp Close profile, and then execute Low Pressure Close. If
no motion is observed, check the following:
- Verify that none of your clamp or ejector overtravel alarms are set.
The QDC module inhibits clamp close if SYS07-B00 through
SYS07-B05 are set
- Verify that the ejector is inside the ejector position for clamp close
enable (EPC63)
- Verify that no programming error codes exist in SYS61 and
SYS62
5.
Upon completion of Clamp Close, observe the pressure reported back
for 1st clamp close segment 2 (CPS13, Pro-Set 600 address
N43:665). If the observed pressure is not approximately equal to the
setpoint entered in CPC13, then check:
- Was your valve and solenoid alignment the same for Clamp Close
profile execution and Clamp Close action in set-output?
If the observed pressure CPS13 is still not representative of the setpoint
(within 20% of CPC13), your pressure valve is not linear over the desired
range of operation.
If:
And Your Selected
Valve is:
Then:
CPS13 was less than CPC13 Direct Acting
Increase FCC44, SCC44, TCC44 by 5%
Reverse Acting
Decrease FCC44, SCC44, TCC44 by 5%
CPS13 was more than
CPC13
Direct Acting
Decrease FCC44, SCC44, TCC44 by 5%
Reverse Acting
Increase FCC44, SCC44, TCC44 by 5%
Repeat steps 2 through 5 as necessary.