4 structure of a can bus system (example), Canopen, 4 structure of a can bus system – Lenze EMF2175IB User Manual
Page 21
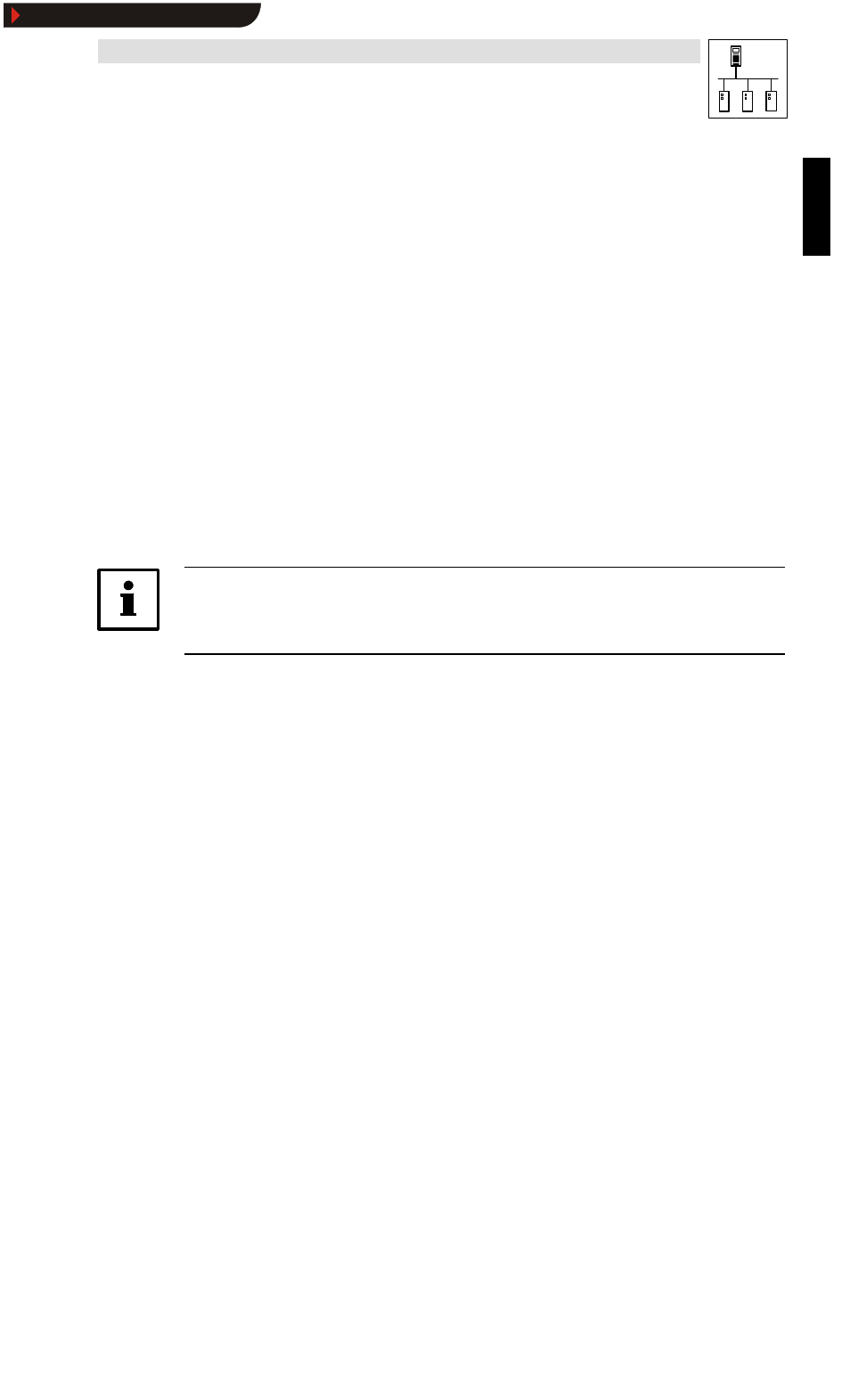
CANopen
4
Installation
4-5
L
BA2175 EN 2.0
4.4
Structure of a CAN bus system
(Example)
The CAN bus system is designed as 2 conductor type (twisted pair) shielded with additional mass
and termination at both ends of the line (see
(
^
4-6)
).
Data can be send and received as follows:
•
Max. 3 process data channels (PDO = Process Data Object)
– Process data are send via the process data channel and are used for high-speed and
high-priority control tasks. Typical process data are, for instance, setpoints and actual
values for a controller.
•
2 parameter data channels(SDO = Service Data Object)
– Parameters are transferred at lower priority than process data. Parameters are set or
changed during, for instance, commissioning or changing the product.
– Parameters are accessed via the parameter data channel of the 2175 fieldbus module to
the Lenze controller codes or corresponding CANopen objects (detailed description in
chapter CANopen parameter setting).
– 2 masters can be connected to the controllers because of the 2 parameter channels. Thus,
parameters can be changed directly at the controller during operation of a machine or
system networked via PLC, using a PC (e.g. with the user software Global Drive Control) or
a keypad. The second parameter data channel can be accessed with an offset of 64 via the
address set (switch or L-C0009). For instance, if a PLC addresses the controller with
address 1 and a second commanding unit address 65, the same controller will be
addressed. Please note that the last telegram determines a parameter when it is accessed
by two units ( see “ Server SDO Parameters”
(
^
6-35)
).
Note!
Please note that the last telegram determines a parameter when it is accessed by two units.
See chapter 5, if you do not use the front switch to enter baud rate and address.
Show/Hide Bookmarks