Delta MMC120 User Manual
Page 67
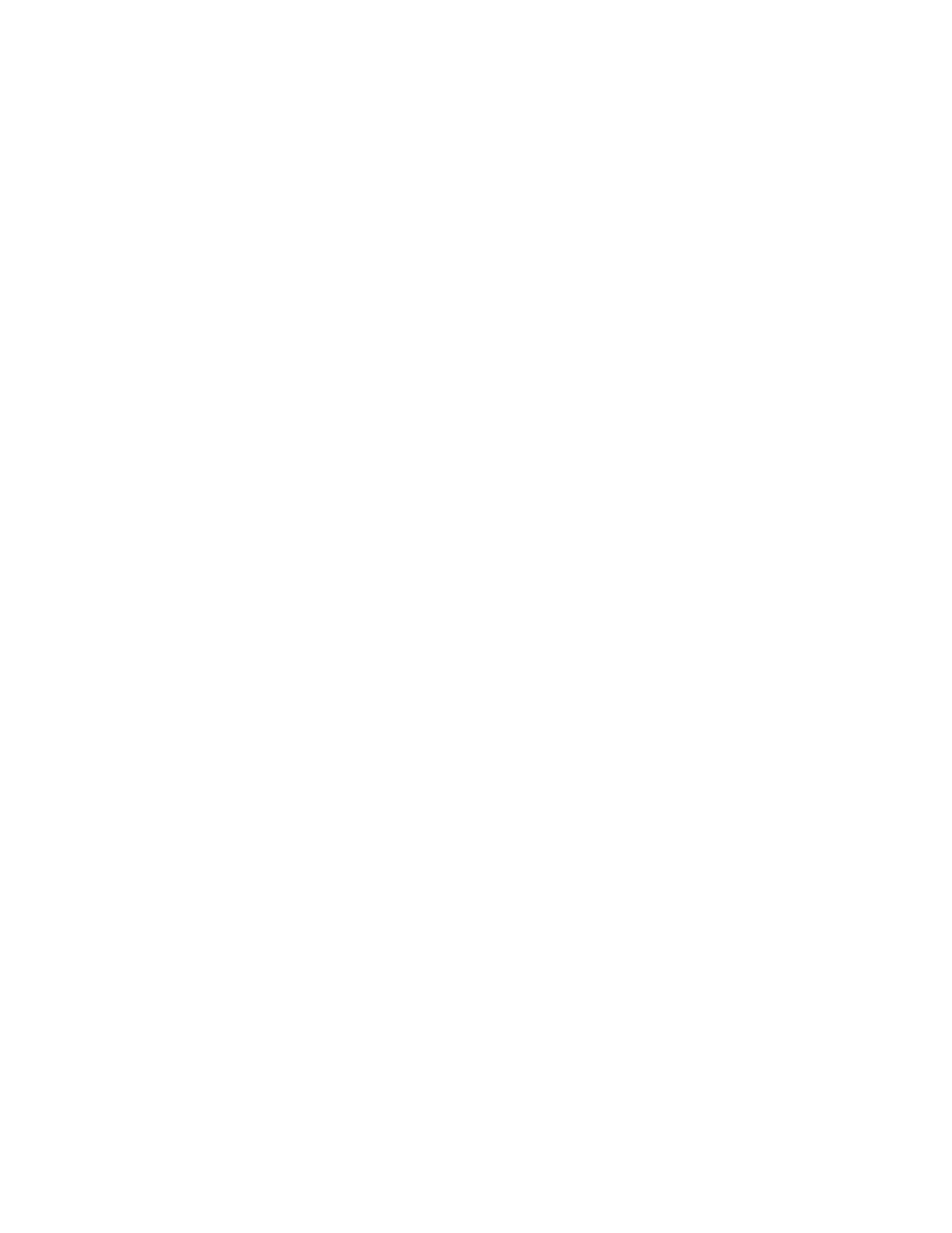
67
by the Motion Controller and initializing the Motion Control Module with those
parameters.
The Motion Controller provides a
STATUS
word for each axis. If an error bit in the
STATUS
word, the Programmable Controller is responsible for shutting down the axis
drive power. It must have a watchdog timer that will shut down the drives if a time-out
occurs.
Write to the Motion Controller only once per scan, otherwise the newest data will
overwrite the previous data.
Error Handling
The motion controller reports errors to the Programmable Controller within one control
loop of detection. Errors are reported by setting bits in the affected axis’s
STATUS
word
and turning on the appropriate LEDS. The Programmable Controller is responsible for
checking errors by reading the
STATUS
words. It is up to the Programmable Controller
to determine what should be done if an error is detected.
The system must be able to shut down the axis drive power using a normally open output
that is held closed when the system is running. This contact should be in series with an
operator emergency off button. If power to the rack is lost, the contact will open and the
axes will stop. If an error occurs in the motion controller the contact can be deactivated,
which stops the axes. Usually the Programmable Controller will not take so drastic a step
until it has determined that all control is lost. An
Halt
command to the axis with an error
can take care of most error conditions.
When two axes are making a coordinated move and one axis starts moving slower than it
should, it is best to issue a
Halt
command to both axes to stop all movement until the
problem with the faulty axis has been resolved.
You can also use
AUTO STOP
detection by setting the appropriate bits in the SOFT
STOP the HARD STOP bytes corresponding to the error bits in the
STATUS
word.
MMC120 Module Problems
Problems and Solutions
Control program cannot access parameters or operate module
1. Module not configured properly—active LED off. Configure the module as a 4-
input and 4-output register module with binary format.
2. Make sure the Programmable Controller is accessing the correct I/O registers.
Red LEDS 2, 3, 4, 6, 7, or 8 are on
This indicates the transducer is not responding to the module. Every millisecond the
module interrogates the transducer’s position. If a return response is not seen after about
two milliseconds, the internal counters overflow, and red LED 4 or 8 will be latched. If a
return response is not seen after six milliseconds, red LED 2 or 6 will be latched. If the