Synchronizing axes – Delta MMC120 User Manual
Page 57
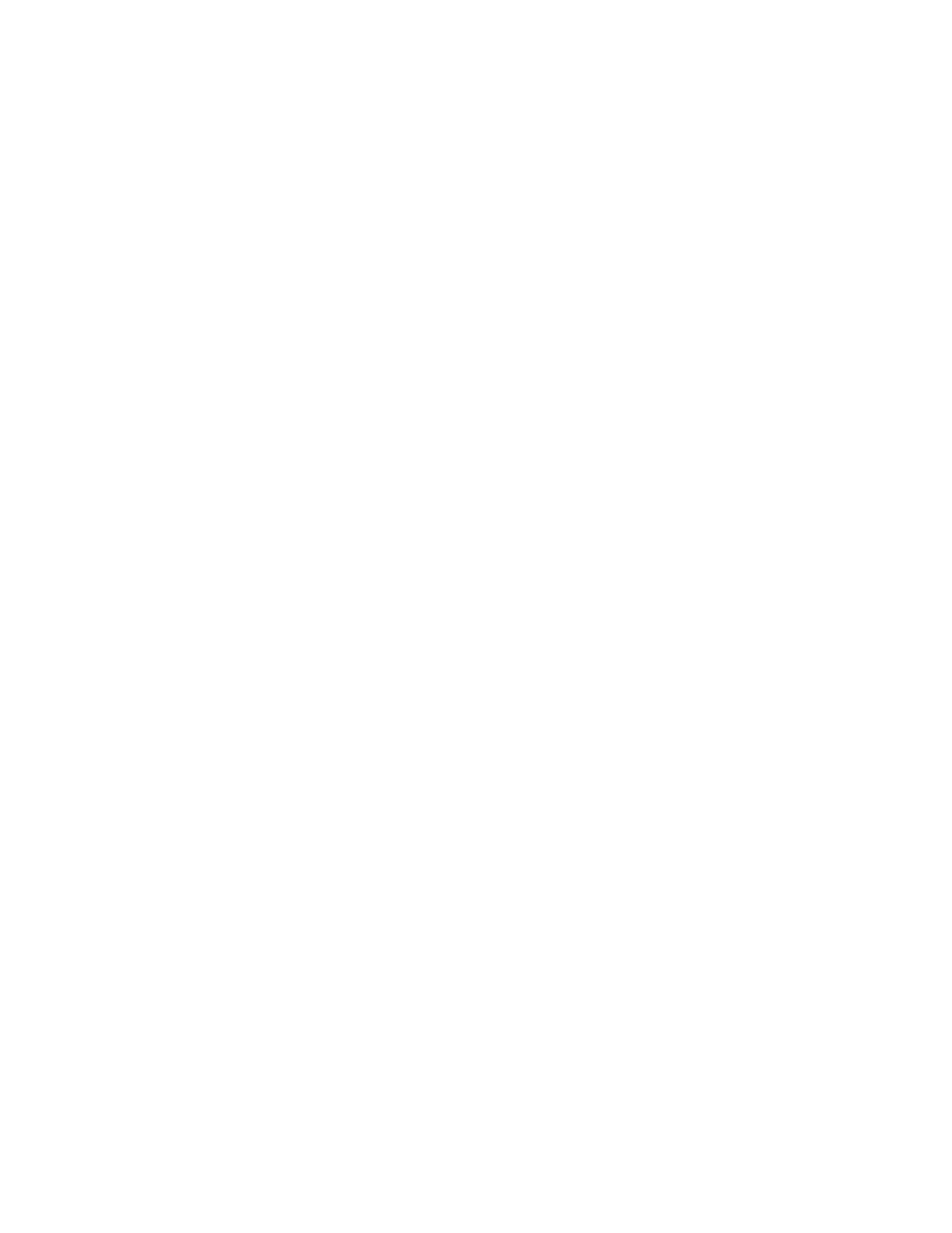
57
ACCEL 10000
12000
15000
18000
DECEL 10000
12000
15000
18000
SPEED 10000
12000
15000
18000
Profile
8
9
10 (0A) 11 (0B)
MODE
1
1
1
1
ACCEL
100
100
100
200
DECEL
100
100
100
200
SPEED 20000
25000
30000
35000
Profile 12 (0C) 13 (0D) 14 (0E) 15 (0F)
MODE
1
1
1
1
ACCEL
200
200
200
100
DECEL
200
200
200
100
SPEED 40000
45000
50000
10000
Synchronizing Axes
Axis synchronization is achieved by setting the Sync bit in the
MODE
word on both axes
and then issuing a
Go
or
Relative Move
command to the last axis.
The following requirements exist when synchronizing axes:
•
Both axes must be initialized, as indicated by the Parameter Initialized bit in the
STATUS
word. Do this by issuing the
Set Parameters
command.
•
The low eight
MODE
bits of both synchronized axes must match exactly.
•
Synchronized commands (
Go
and
Relative Move
) must be issued to the second axis.
•
Synchronized commands issued to the first axis are ignored.
•
The
MODE
,
ACCELERATION
,
DECELERATION
,
SPEED
, and
COMMAND
VALUE
fields must be set on both axes before any synchronized commands are
issued.
Internal to the MMC120, the synchronization is accomplished as follows:
•
The axis with the longest travel distance is designated the “master”. If both axes are
moving the same distance, then first axis is designated the “master”. The other axis is
designated as the “slave”.
•
The maximum speed of the master axis is limited so neither of the synchronized axes
will go above their requested
SPEED
.
•
The master then moves toward its destination using its own
ACCELERATION
,
DECELERATION
, and the speed calculated in the above step.
•
At the same time, the
TARGET POSITION
of the slave axis is ratioed to the target
position of the master based on the distance each is traveling.
•
If either synchronized axis is halted during the move, the other axis will halt as well.