Delta MMC120 User Manual
Page 126
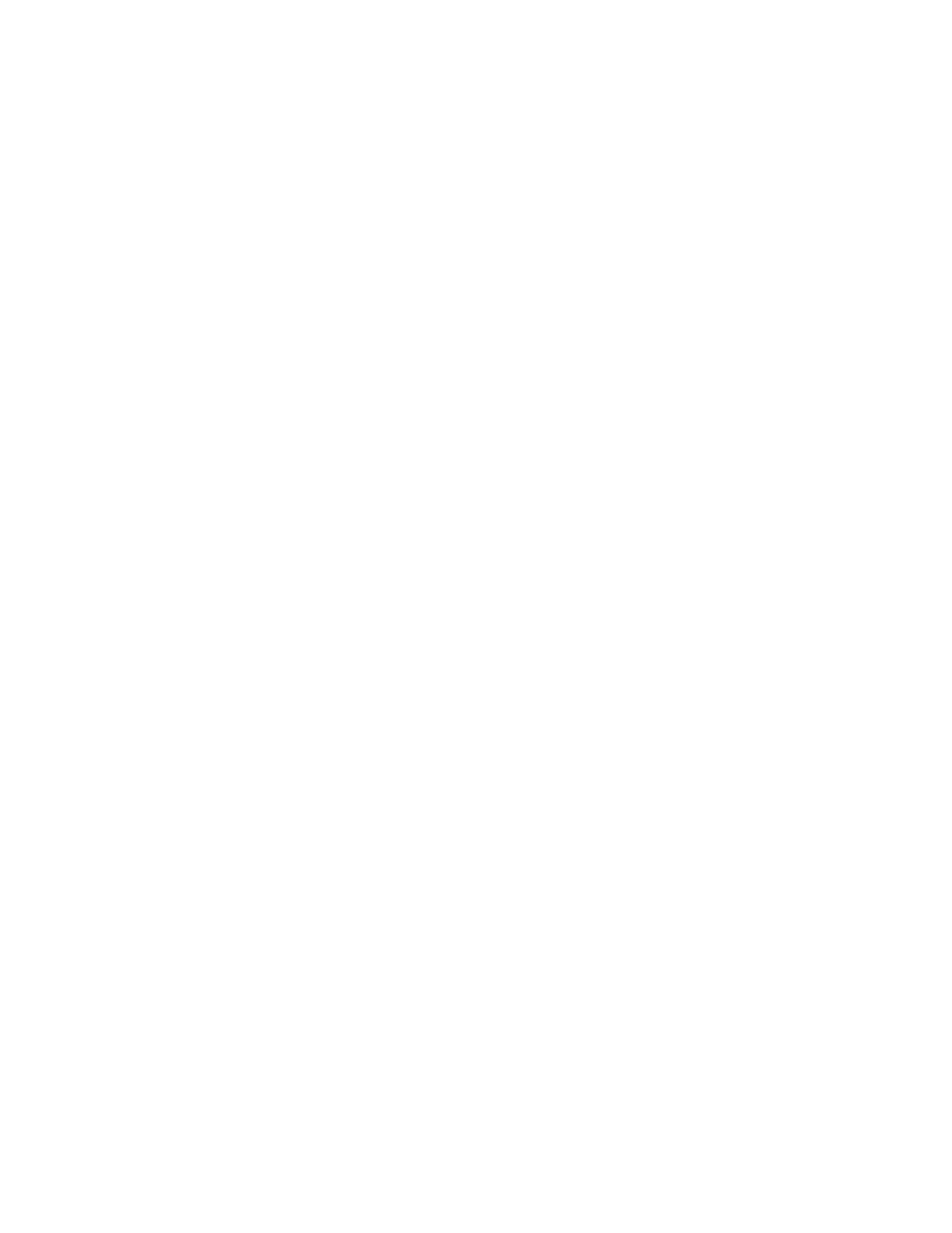
126
a 16-bit number. See
Valid 16-bit Positions
for details on this limitation. This bit is also
set if—when recirculations are used—
TRANSDUCER COUNTS
is calculated to less
than zero.
ACTUAL POSITION
will be displayed as 65535 in the overflow case, and as
zero (0) in the underflow case. It causes either an Open Loop ramp down (Soft Stop), or
a Hard Stop, depending on the setting of
AUTO STOP
bits 2 and 10. This bit will stay
on until a new command is given to the axis.
To recover from this error condition you must move the axis, either manually or with an
Open Loop Command
, until the
ACTUAL POSITION
becomes valid again.
This error occurs for one of two reasons:
1. The overflow case (Actual Position displayed as 65535) happens because the
transducer is longer than can be accommodated by the 16 bit Actual Position Field
given the scaling of the transducer counts. To fix this, you can either reduce the
SCALE
parameter; increase the Prescale Divisor in the
CONFIGURATION Word
;
or, if you are using a PWM type transducer, increase the number of recirculations
specified in the
CONFIGURATION Word
(without increasing the number of
recirculations in the transducer).
2. The Underflow case (Actual Position displayed as 0) happens because the number
of recirculations specified in the
CONFIGURATION Word
is too large. To fix
this, decrease the number of recirculations specified in the Configuration Word
(without increasing the number of recirculations in the transducer).
Bit 7 - Integrator Windup
This bit is set when the integrator value is larger than 20% or 80%, depending on the
setting of the Integrator bit in the Configuration word. It causes no action, a Soft Stop, or
a Hard Stop, depending on the setting of
AUTO STOP
bits 7 and 15. This bit will stay
on until a new command is given to the axis.
Bit 8 - Following Error
This bit is set when the difference between the
TARGET POSITION
and the
ACTUAL
POSITION
is greater than the MAXIMUM ERROR parameter. It causes no action, a
Soft Stop, or a Hard Stop, depending on the setting of
AUTO STOP
bits 8 and 16. This
bit will stay on until a new command is given to the axis.
Bit 9 - Acknowledge
This bit will toggle after the motion controller receives a valid command or Status Area
Request. This can be used to verify that the motion controller has received the command.
Bit 10 - Initialized
This bit is set after a
Set Parameter ('P') command
is successfully executed. Until this bit
is set, the axis will not respond to any
GO ('G') commands
. This bit is cleared whenever
the module is reset.